University of Washington Department of Environmental Health
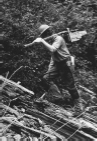
THE SUBTOPICS IN THIS CATEGORY REFLECT HAZARDS in the forestland work environment, and factors that may, directly or indirectly, affect health and safety risks. Research is necessary to understand the new risks that are associated with the industry, technology, and work practices. The organization of work is increasingly recognized as an important component in promoting health and safety, but insufficient research is available to provide guidance to managers, employers, and employees. Individual behaviors can contribute to the overall risk for injury on the work site. And lastly, training is essential to the successful implementation of workplace changes designed to prevent injury and illness.
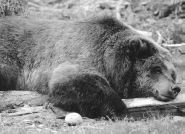
Loggers and foresters are subject to many hazards associated with working in the forest. Some key Northwest environmental hazards identified in this project were remote location, climate and weather, animals, plants, insects, terrain, stand characteristics, fire, and other forest users. The extent of some of these hazards differ depending on the region.
[NIOSH NORA: None]
IMPORTANCE
Workers in Northwest forests can experience a range of terrain and stand characteristics, including the challenges of steep slopes, dense stands, snags, wind falls, thick underbrush and a maze of downed wood. These conditions affect the individual worker, work organization and the operation and design of equipment and vehicles, such as helicopters. The extent of environmental hazards differs depending on the region. For example, Alaskans appear to have more problems with animals and terrain, while more populated areas such as western Washington and Oregon have greater concerns with other forest users, including recreationalists and environmental activists, who may pose a danger to the worker and themselves.
One telephone interview participant provided a good sense of the dangers associated with Alaskan logging operations. He noted that workers who fall and buck timber in this state are at considerable risk for injury. Some of the causes include operating in an old forest, which may consist of decayed, dead and broken timber located on steep and unstable ground. In order to remove a merchantable tree, numerous other dead trees may have to be removed. He also noted that, since helicopters can only carry a certain weight, workers must buck the trees on steep terrain placing the worker at risk for slipping timber, mud slides, and unreliable footing.
RESEARCH OPPORTUNITIES
- Identify plants that pose a harm to workers
- Assess the impact of temperature extremes
on the body and on injuries
- Develop improved barrier lotions for poison
oak
- Design new shoe tread for all weather
conditions and develop improved footwear
- Develop guidelines for movement through
non-trailed lands
- Determine the impact of small-diameter trees
on safety
- Correlate fatalities to stand characteristic
data
- Identify the characteristics that make snags
hazardous
- Evaluate causes documented in fatality and
accident reports (for example, role of species,
size and number of rocks, tree grade)
- Develop new logging techniques which
incorporate methods to mitigate selective
cutting hazards
TRAINING OPPORTUNITIES
- Provide bear safety and wilderness survival
training
- Educate workers on woods work preparation
including proper dress, water, etc.
- Conduct fire safety training
ADDITIONAL INFORMATION
Apperson C, Walvogel M. Bite, sting, and envenomization hazards in agriculture and forestry. In: Safety and Health in Agriculture, Forestry, and Fisheries (Langley RL, McLymore RL, Meggs WJ and Roberson GT eds). Rockville: Government Institutes, Inc., 1997. pp. 59-65.
Kemp P. Weather and terrain hazards in helicopter logging. In: Helicopter Logging Safety: NIOSH Alaska Interagency Working Group for the Prevention of Occupational Injuries, 1998.
National Wildfire Coordinating Group: Wildland Fire Education Working Team. Online: http://www.nwcg.gov/teams/wfewt/wfewt.htm
Northwest Territories Wildlife and Fisheries. Safety in Grizzly and Black Bear Country. Online: http://www.enr.gov.nt.ca/_live/documents/documentManagerUpload/SafetyInGrizzlyandBlackbBearCountry.pdf.
Timber harvesting tasks are complicated and inherently hazardous, and can result in an incident, even when the utmost care is taken by management and the worker. Project participants shared their knowledge of these activities, and identified specific high risk tasks, such as timber falling, log hauling, chain-saw operation, thinning, hazardous materials handling, trucking, and helicopter logging (both for helicopter aircrew and ground crew). Frequently, concerns related to equipment. The harvesting crew has to work closely among skidders, cables, processors, trucks, and other heavy equipment, and the risks presented by the presence of this potentially dangerous equipment can be exacerbated by terrain, type of logging (i.e., selective logging) and limited landing space. Another frequently cited hazard was rolling, falling, or flying objects (typically trees and limbs). These hazards can result in struck-by incidents that are fatal or that cause disabling injuries.
[NIOSH NORA: None]
IMPORTANCE
In recent years, the forest resources industry has achieved great improvements in the prevention of injury and illness; however, certain tasks continue to place workers at extremely high risk. The Bureau of Labor Statistics’ 1984 analysis of 1086 logging employees in the US found the top five activities at the time of injury were falling (23%), limbing (15%), choker setting (14%), bucking (12%), and skidding (9%).34 Although statistics for Alaska, Idaho, Oregon and Washington are limited in this area, the incidents identified in British Columbia may provide insights for the US Northwest’s operations. In British Columbia, from 1991 to 1995, the top four logging occupations by number of serious workers’ compensation claims were fallers (33%), loaders and sorters (17%), logging laborers (12%), and foreman (10%). Log truck drivers suffered 9% of serious claims and 19% of fatal claims, over the same period. For this same group, incidents frequently resulted from being struck by an object, chain saw, or trees and parts of trees (33%); falling from a tree, log, or vehicle, (21%); and overexertion (11%).
Helicopter logging is a useful means for harvesting timber in the Northwest where terrain is often steep, rugged, or roadless. Unfortunately, in the past two decades, this newly emerged industry has seen high rates of incidents, which often result in death. Of the 65 helicopter accidents from 1980 to 1995, 25 resulted in fatalities: to the pilot (18), logger passengers (5), and ground crew (2). The helicopter logging industry has been working closely with the Alaska NIOSH field station to identify hazards and prevention measures, and 32 have seen a drop in incidents in recent years, demonstrating the success of government-industry teamwork.35
Participants in the telephone interviews, Workshop, and surveys suggested measures to reduce the risk of injury, such as using appropriate equipment for the terrain and the job; conducting routine equipment inspection and maintenance; and increasing awareness, and good skills. Participants noted that the available personal protective equipment has limited effectiveness for protecting forestland workers.
RESEARCH OPPORTUNITIES
- Examine the dynamics of falling trees
- Assess harvesting systems and hazard
abatement
- Analyze current harvesting practices to
determine which activities increase safety
- Determine frequency and timing of hazards
- Evaluate and adapt successful international
solutions
- Survey training impact on near-miss rates
- Develop a reporting structure for near-misses
and identify how many near-misses occur
prior to an incident
- Investigate ergonomic issues in saw handling
- Conduct hazard assessment of manual timber
felling
- Conduct review of accidents and causes
over the past ten years
- Develop a new method for identifying logs
to replace the branding hammer
- Modify saw design to include a fire-control
device
- Identify good handling techniques for chain
saws
- Develop methods to improve lockout/tag
out procedures
- Review transportation injuries, including
prevalence and causal factors
- Identify methods to reduce road hazards,
including brush clearance and curve markings
- Investigate the long-term effects of chemical
exposure on respiratory and dermal systems
TRAINING OPPORTUNITIES
- Educate worker and supervisor to perform
collaborative review of new task
- Provide guidance on work practices that
reduce strength requirements
- Ensure that workers understand the felling
process and how cuts affect the fall
- Instruct workers on proper machinery
inspection and maintenance
- Couple sale of equipment with training
- Inform workers about the need for and proper
use of personal protective equipment
- Develop helicopter and plane crash survival
training
- Provide defensive driving instruction
ADDITIONAL INFORMATION
NIOSH. Preventing Injuries and Deaths from Skid
Steer Loaders. DHHS 98-117 Cincinnati, OH:
NIOSH, 1998.
NIOSH. Helicopter Logging Safety: NIOSH Alaska Interagency Working Group for the Prevention of Occupational Injuries, 1998.
Tippens R, Landly R. Epidemiology of forestry injuries and illnesses. In: Safety and Health in Agriculture, Forestry, and Fisheries (Langley RL, McLymore RL, Meggs WJ and Roberson GT eds). Rockville: Government Institutes, Inc., 1997. pp. 59-65.
Workers’ Compensation Board of British Columbia. Logging Industry Focus Report. November, 1996.
American Forest & Paper Association homepage: http://www.afandpa.org.
Mississippi State Extension Service. Forest Herbicide Safety. Online: http://msucares.com/pubs/publications/p1874.pdf.
OR OSHA. Online: http://www.cbs.state.or.us/osha/index.html.
Workers’ Compensation Board of British Columbia. Forestry Publications Catalog. Online: http://www2.worksafebc.com/publications/OHSRegulation/Part26.asp.
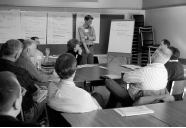
Most forestry and logging workers develop skills through on-the-job training from experienced coworkers. Loggers need to learn complex skills related to the task, tree site, machinery, and equipment. Further research is needed to identify the best ways to communicate safety and health information to workers in the forest, as well as those individuals who may affect the job, such as landowners, management, government officials, and others. Participants identified several effective methods of training, including tailgate sessions, videos, internet, checklist, and hands-on experiences. They also emphasized that these training sessions can be valuable opportunities for workers to share their knowledge, both with each other and with trainers.
[NIOSH NORA: Control Technology & Personal Protective Equipment, Intervention Effectiveness Research]
IMPORTANCE
Effective skills training is a key prevention and intervention tool as expressed by participants of the telephone interviews, Workshop, and surveys. In fact, skills training emerged as a top priority issue in the Workshop, and personal interviews identified many training improvement suggestions. Most forestry and logging workers develop skills through on-the-job training from experienced coworkers. The development of skills and techniques as a means for improving safety outcomes is an association that has not been well studied, yet inadequate or inappropriate training is frequently cited as a cause of injury in forestry.36 Safety training per se was not viewed as highly beneficial, but safety training that is incorporated into a broader skills training program was considered to be an effective means of reducing injury and illness.
Workers in the Northwest forest industry rely on training provided by their employers, trade associations, contract logger associations, unions, and state and federal government programs. Yet, the recommendations that were raised suggest that there are gaps in reaching some workers and there should be an increased emphasis on skills training. Specific training issues raised by participants included: risk communication, formalized skills training, hazard recognition, training appropriate to work and region, emergency medical aid, effective educational tools, bilingual materials and an executive training program. It was also suggested that additional funds are needed to support training efforts.
RESEARCH OPPORTUNITIES
- Determine if safety practices are influenced
by skills training
- Perform training needs assessment
- Identify obstacles to training
- Evaluate effectiveness of behavior-based safety
training
- Develop training methods that are economical
and include incentives for their implementation
- Identify the characteristics of successful
training programs and what makes them work
- Develop strategies to get information to
remote areas
- Identify the resources needed for employers to
conduct good training programs
- Develop training that is appropriate to specific
worksite and workgroup
- Assess if advanced wilderness first aid courses
improve injury outcomes
TRAINING OPPORTUNITIES
- Replicate Swedish model with graded, multiyear
training
- Develop certification and apprenticeship
programs
- Provide continuous training, particularly on
new equipment and changing technology
- Conduct safety training for top management
- Implement individualized training in the field
- Increase first aid and other emergency
procedure training
- Instruct workers about hazard recognition
- Conduct tailgate sessions
- Teach injury response planning
- Provide guidelines for risk assessment and
decision-making
- Develop self-training methods
- Design incremental training to avoid over training
and burnout
- Conduct pre-employment job skills testing
to assess worker's training needs
- Partner new worker with experienced workers
TRAINING MATERIALS
- Integrate more senses into training, using scale
models, sight and sound, and hands-on training
- Develop materials for safety meetings
- Use pocket-size worker guides with color,
illustrations, and useful format
- Design various formats for video, computer,
on-the-job instruction, train-the-trainer
sessions, and trainer teams
- Compile a resource list of available training
sources and libraries
- Use videos with short graphic messages that
identify specific hazards associated with each
job task
- Incorporate checklists into training manuals.
- Use the internet for training
- Provide accident scenarios and possible
solutions
ADDITIONAL INFORMATION
Forest Resources Association, Inc. Fifth Report on
the Status of Statewide Logger Training and
Education Programs in Thirty-Two Forested
States. (Report 99-A-2). Rockville, MD:
American Pulpwood Association, 1999.
Cohen A, Colligan M. Assessing Occupational Safety and Health Training. DHHS 98-145. Cincinnati, OH: NIOSH, 1998.
Joint FAO/ECE/ILO Committee on Forest Technology, Management, and Training. Safety and Health in Forestry are Feasible! (JCJ-Seminar 7– 10 October 1996) Konolfingen, Switzerland, 1999.
US NIOSH. A Model for Research on Training Effectiveness. DHHS 99-142. Cincinnati, OH: NIOSH, 1999.
Forest Resources Association, Inc. Online: http://www.forestresources.org/.
Associated Oregon Loggers’ Oregon Professional Logger program. Online: http://www.oregonloggers.org/Opl_Program.aspx
BC Workers Compensation Board Forestry Publications & Resources. Online: http://www.worksafebc.com/publications/.
National Skills Standards Board literature database. Online: http://www.nssb.org/cgi-bin/l-search.cfm [The NSSB was active from 1994 to 2003].
Washington Contract Loggers Association’s Accredited Logger program. Online: http://www.loggers.com/mlp.htm
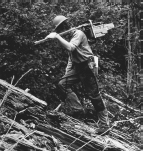
The most basic level of health promotion lies in the hands of individual workers. The behavioral sciences study workers’ actions as influenced by knowledge, perceptions, motivations, skills, and environment. The field of behavioral safety has been applied in the forest industry with good results and indicates that the science of occupational psychology is an important direction for future research.
[NIOSH NORA: None]
IMPORTANCE
Timber harvesting requires technical skill, teamwork attitude, strength, agility, and quick mental responses. Along with all these demands, workers hold the responsibility for behavior that will save themselves and their coworkers from injury or loss of life. The concept that people’s attitudes and behaviors affect their personal safety is intuitive and well documented, yet the contribution of an individual’s behavior to their overall risk is not well understood. The field of behavioral safety has been applied to managers and employees in the forest industry with positive results, and indicates that the science of occupational psychology is an important direction for future research and holds a place within a safety program.
A member of the industry noted the importance of integrating behavior-based training into the workplace. He commented that, as an industry, we “…should provide as safe environment as possible and try to maintain a conscious level of safety in each individual…. The real problem is people being aware and alert of safety issues to themselves and others. Not just knowing safety first, but knowing and acting. Since [we] have started behavioral safety…there has been a reduction in accidents.”
Participants expressed concern about the following behaviors they consider are hazardous in Northwest forestlands: substance abuse, crew attentiveness, risk taking, safety attitude, violence in the workplace, and personal accountability.
RESEARCH OPPORTUNITIES
- Develop strategies to identify and overcome barriers to wearing hearing protection
- Investigate the relationship between substance abuse and injury
- Identify measures that decrease substance abuse
- Develop methods to identify and measure positive safety behaviors
- Create methods and incentives to overcome resistance to modifying work habits
- Design behavior research to determine risk
perceptions and attitudes toward
taking safety precautions
- Investigate causes of workplace violence
TRAINING OPPORTUNITIES
-
Conduct substance abuse interventions
- Implement behavior-based safety training
techniques
- Resolve workplace violence through conflict
resolution and mediation
- Use diagrams and fatalgrams (notice of fatal
accidents) to keep industry informed about
accidents
ADDITIONAL INFORMATION
Cambridge Center for Behavior Studies: Behavioral
Safety. Online: http://www.behavior.org/interest.php?id=16#tabs.
Behavioural Safety. Online: http://www.behavioural-safety.com.
Journal of Occupational Health Psychology homepage: http://www.apa.org/journals/ocp.html.
Journal of Organizational Behavior Management.
WISHA. Workplace Violence: Awareness and Prevention for Employers and Employees (F417-140-000). Online: http://www.wa.gov/lni/ipub/i417-140-000.htm.
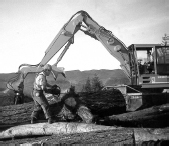
Organization of work refers to how work processes are structured and managed. In addition to the long recognized job stress associated with aspects of work organization, studies are now identifying contributions to other health problems, including musculoskeletal disorders and cardiovascular diseases. Research is needed to better understand how the organization of work is influenced by the changing economy and workplace, and how the potential effects impact worker safety and health.
[NIOSH NORA: Organization of Work]
IMPORTANCE
The priority concerns on this topic, which were expressed by constituents, included long hours, speed of work, emotional stress, working alone, ground communications, harvesting design, and the decentralized nature of work. One participant noted the effect of exhaustion on injury rates in his operation. He said that the most common time of day for reported injuries was Monday morning and at the conclusion of workers putting in “bonus hours” on Wednesday afternoon. He suggested that researching the time and date of injuries by job category may provide new knowledge to reduce injuries in the workplace.
During the telephone interviews, a governmental agency representative raised the importance of orientation programs for new employees and for those new to a particular job. He emphasized that this initial training would alert workers to the specific hazards of the tasks; inform them about correct work procedures; and point out the precautionary measures that must be taken to ensure their safety and the safety of their coworkers. He also stated that workers should be able to demonstrate their competence and that diligent supervision of safe work procedures is essential to preventing injuries.
A contractor who was interviewed during this project described how certain tasks were inherently dangerous and the solutions his company found to mitigate the dangers. He noted that “(T)he biggest hazard we have is line skidding on steep ground. I haven’t seen anything come along that will make it any safer. [We] need people who will do the job safely and not take any chances. A lot of this goes back to the fact that we pay higher wages and try to hire the best people available. Safety is one of our biggest longterm costs. It will really get you if you don’t take care of it. We will adopt new equipment if it is as safe and as productive as what we are already doing.”
Other participants recommended that safety is always a priority and should be placed before the prescription for the sale.
RESEARCH OPPORTUNITIES
-
Identify organizational models that may
contribute to workers' safety
- Examine the relationship between work
organization and job type
- Investigate how small companies can be
organized to improve safety
- Examine how work organization can reduce
fatigue
- Determine how many employees work alone,
the hazards of working alone, and how to
reduce the hazards
- Develop a sensor that identifies presence of
worker in operating area
- Develop signal system that tells workers if they
are an appropriate distance from pull
- Establish framework that demonstrates impact
on workers, cost/benefit analysis for required
policies, and how factors can be mitigated
with current technologies
- Look for correlation between fatalities and
injuries and differences in forest prescriptions
ADDITIONAL INFORMATION
Griffiths A. Organizational Interventions. Scan J Work Environ Health 25 (Special Issue):589- 596 (1999).
Hurrell JJ, Murphy LR. Psychological job stress. In: Environmental and Occupational Medicine (Rom WN, ed.) New York, NY: Little Brown and Co., 1992. pp. 675-684.
International Labour Office. ILO Encyclopedia of Occupational Health and Safety. Vol 1, Part II, Section 3, Psychosocial and organizational factors. Geneva, Switzerland, 1998.
Keita PG, Sauter SL, eds. Work and Well-Being: An Agenda for the 1990’s. Washington, DC: American Psychological Association.
US NIOSH. Stress. DHHS 99-101. Cincinnati, OH: NIOSH, 1999.
Back to Table of Contents
Disclaimer and Reproduction Information: Information in
NASD does not represent NIOSH policy. Information included in
NASD appears by permission of the author and/or copyright holder.
More