Version 1 - 10/2013
Instructions
This sample program is provided to assist you as an employer to meet the Logger Safety Initiative Accident Prevention Program requirements. The content of this program must be used. However, we encourage employers to add their company specific policies to this program.
Table of Contents
Training Requirements for Cutters
(1) A worker may not work as a cutter in a logging operation unless;
(a) the worker receives training for cutting that meets the training requirements in section (2), and an experienced cutter certifies in writing that the trainee has successfully completed the training requirements, or
(b) meets the requirements in section (4) and an experienced cutter certifies in writing that the cutter’ experience satisfies training requirements.
Note: This section does not apply to workers who occasionally fall trees such as the falling of guyline trees or tail trees, but the employer must meet all other training requirements in the Safety Standards for Logging Operations Chapter 296-54 WAC.
“New cutter”: cutter with less than 150 working days of experience as a timber cutter.
(2) New cutter training must include the following:
(a) Receive basic training in falling and bucking by working one-on-one with an experienced cutter (trainer) until the trainer determines that the trainee cutter is qualified to work independently under close supervision, but must be a minimum of 30 working days.
(i) Basic training must include completion of the Cutter Training Curriculum and a review of the policies and procedures listed on the Employee Safety Orientation Training Record form in this Accident Prevention Program document.
(b) After completion of basic training under paragraph (a), a trainee cutter must be evaluated on a weekly basis by an experienced cutter for a minimum period of 120 working days.
(c) A training log (see Appendix 8) for the basic training and supervision period must be maintained by both the trainer and the trainee.
(i) The training logs must include the dates of training/supervision, and the name and signature of both the trainer and trainee.
(d) If a new cutter’s employment ends prior to completing the basic training and or the supervision period, a subsequent employer may accept prior training that is properly documented on the training logs. If accepted by a subsequent employer, the trainee would only need to complete the remaining minimum training requirements.
(3) If, at the end of the training and supervision period, the trainee's cutting is consistent with the safe work practices included in the Cutter Training Curriculum, the experienced cutter will certify in writing that the trainee has successfully completed the training requirements.
(a) The Logger Safety Program Cutter Safety Audit Form (see Appendix 7) must be used to evaluate whether a cutter has successfully completed training and as a certificate of training. A completed copy of the Cutter Safety Audit Form must be maintained by the employer and a copy must be provided to the cutter.
(4) Subsection (2) does not apply to a cutter who satisfies all of the following requirements:
(a) A cutter has performed falling duties regularly for at least 150 working days before the evaluation under paragraph (b) of this subsection takes place; and
(b) An experienced cutter evaluates the cutter’s work practices and determines that the cutter is performing the job in a manner that is consistent with the safe work practices included in the Cutter Training Curriculum. The experienced cutter will certify in writing that the cutter’s experience satisfies training requirements.
(i) The Logger Safety Program Cutter Safety Audit Form must be used to evaluate the cutter’s work practices, determine whether a cutter has satisfied training requirements, and as a certificate of training. A completed copy of the Cutter Safety Audit Form must be maintained by the employer and a copy must be provided to the cutter.
Safety Policy and Commitment
This company places a high value on the safety of its employees. We are committed to providing a safe workplace for all employees and have developed this program for injury prevention to involve management, supervisors, and employees in identifying and eliminating hazards that may develop during our work process.
It is the basic safety policy of this company that no task is so important that an employee must violate a safety rule or take a risk of injury or illness in order to get the job done.
Employees are required to comply with all company safety rules and are encouraged to actively participate in identifying ways to make our company a safer place to work.
Supervisors are responsible for the safety of their employees and as a part of their daily duties must check the workplace for unsafe conditions, watch employees for unsafe actions and take prompt action to eliminate any hazards.
Management will do its part by devoting the resources necessary to have a safety program that is effective in practice. We will develop a system for identifying and correcting hazards. We will plan for foreseeable emergencies. We will provide initial and ongoing training for employees and supervisors. And, we will establish a disciplinary policy to ensure that company safety policies are followed.
Safety is a team effort – Let us all work together to keep this a safe and healthy workplace.
(Customize by adding any additional policy items that you may have and/or deleting any that do not apply to your company.)
___________________________________
Owner’s Signature
SAFETY DISCIPLINARY POLICY
We believe that a accident prevention program is unenforceable without some type of disciplinary policies. Our company believes that in order to maintain a safe and healthy workplace that the employees must be cognizant and aware of all company and state safety and health regulations as they apply to the specific job duties required. The following disciplinary policy is in effect and will be applied to all safety or health violations.
(Note: A formal disciplinary policy, such as the following 3 step policy, or a less formal policy found below could be implemented. You may voluntarily choose to use one of the policies in the current form or with changes.
The following steps will be followed unless in the unlikely event that the seriousness of the violation would dictate going directly to Step 2 or Step 3.
- A first time violation will be discussed orally between company supervision and the employee. This will be done as soon as possible.
- A second time offense will be followed up in written form and a copy of this written documentation entered into the employee's personnel folder.
- A third time violation will result in time off or possible termination, depending upon the seriousness of the violation.
OR
Any violation of this accident prevention program or applicable state safety standard may result in disciplinary action or termination.
Safety Responsibilities
Employer Responsibility
- The employer must designate, a supervisor(s) for each jobsite who is both competent and qualified and has the authority to:
- Supervise all personnel at the site.
- Enforce the company's safety and health program.
- Verify that all current and new employees:
- Can safely perform assigned work tasks.
- Have received adequate job safety instruction and training.
- The employer must implement a procedure for monthly safety inspections of all logging sites to identify and correct unsafe working conditions and unsafe work practices (see Monthly Safety Inspection form in Appendix 4).
- The safety inspections must be conducted by a competent and qualified person.
- The safety inspections must include a review of the safety performance of each employee.
- Safety inspections must be documented.
- Documentation must include:
- Person who conducted the inspection and their signature
- Date of the inspection
- Employees at the worksite
- Identified hazards
- The employer must document what actions were taken to correct identified hazards.
- The employer must meet the following training requirements for employees:
- Ensure that all workers on a logging site have received safety orientation and training specific to their job.
- Provide a worker with refresher training if a workplace observation, jobsite inspection or report from another employee reveals that a worker is not performing work tasks safely.
- Closely supervise each employee who is receiving job safety and health instruction and training.
- Require employees to demonstrate the ability to safely perform their work task before permitting them to work independently.
- Document training per the requirements of the Safety Standards for Logging Operations WAC 296-54.
- Ensure that training is provided by persons who are competent and qualified.
- Ensure that training is conducted in a language and manner that the worker will understand.
- Ensure that their trainers understand their roles and responsibilities including:
- Determine the experience level of the trainees;
- Serve as a positive role model for the trainees;
- Provide training that at a minimum meets the training curriculum of the Logger Safety Program;
- Effectively communicate the training curriculum;
- Effectively demonstrate proper work practices as required in the training curriculum;
- Observe and verify that the trainee can perform the proper work practices as required in the training curriculum.
- Ensure that all workers receive four LSI required trainings per year.
- Training materials will be created for LSI and provided to LSI participants to complete. The employer and supervisor, if delegated, and all employees engaged in manual logging operations must receive at least four (4) of the LSI trainings. Training can be conducted by any of the employees or an outside person and can be done as part of required safety meetings.
- LSI participants will complete and document that the training took place. The completion of training will be assessed at the annual comprehensive DOSH consultation or the third party audit.
Employer/Supervisor Responsibility
- Assure that all safety and health rules, regulations and company policies and procedures are understood by conducting new employee safety orientations, on-the-job training and refresher training when an employee demonstrates unsafe job performance.
- Always set a good example!
- Require the proper care and use of all needed personal protective equipment.
- Conduct safety meetings at least monthly and discuss site specific hazards or other relevant safety topics such as near-misses and accidents. Document the subject(s) discussed and the attendance.
- If the safety meeting covered one of the four LSI required trainings, no further documentation is needed.
- Encourage employees to report unsafe acts and unsafe conditions.
- Receive and take initial action on employee safety suggestions or disciplinary measures.
- Train employees (new and experienced) in the safe and efficient methods of accomplishing each job or task as necessary. The required training for each job is included in this program.
- Conduct monthly safety inspections to identify and correct hazards such as unsafe acts and unsafe conditions.
- Conduct an investigation of all serious accidents.
Employees’ Responsibility (all)
- Employees must coordinate and cooperate with the employer and other employees in an attempt to eliminate accidents.
- Employees must promptly report unsafe conditions and practices to their supervisor.
- Employees must be aware of and follow all safe practices that apply to their work. If unsure how to safely do a job task, ask your supervisor or coworker.
- Employees should offer safety suggestions that may contribute to a safer work environment.
- Alcohol, marijuana, narcotics, or illegal drugs are not permitted and cannot be used in or around the worksite and company vehicles. Employees under the influence of alcohol, marijuana, narcotics, or illegal drugs are not permitted on the worksite or in company vehicles. This does not apply to employees taking prescription drugs as directed by a health care provider if the use does not endanger the employees or others.
- Note: The employee must discuss prescription medications with the health care provider to determine if the medication:
- does not impair the employee’s judgment, coordination, motor control, concentration, or alertness, and
- does not endanger the employee or others in the performance of their work.
- Employees must conduct themselves in a workmanlike manner while on the worksite.
- Employees must promptly report to their immediate supervisor each industrial injury or occupational illness, regardless of the degree of severity.
- Employees must not operate machinery unless authorized by your supervisor and properly trained.
- All occupants of a vehicle must have their seat belt securely and tightly fastened while the vehicle is being operated.
General Safety Information and Rules
Introduction
The underlying cause of many logging accidents is lack of safety training. Safety training is concerned primarily with helping the employee develop the needed skills and abilities to use equipment and/or perform a procedure. Training is required to be provided by a competent and qualified person. A competent and qualified person is defined in WAC 266-54-505.
- Competent person - One who is capable of identifying hazards in the surroundings or working conditions which are unsanitary, hazardous or dangerous.
- Qualified person - A person, who by possession of a recognized degree, certificate, professional standing, or by extensive knowledge, training, and experience, has successfully demonstrated ability to solve or resolve problems relating to the subject matter, the work, or the project.
Safety must be taught before the employee is exposed to the hazards of the job.
The following training curriculum must be used and thoroughly explained to each employee involved in cutting timber. The primary purpose of the curriculum is prepare you to work in the safest possible manner, so that you go home safely each and every night.
There are several rules of thumb that you should always keep in mind:
- Never do anything you feel may be unsafe - no matter what anyone says.
- No tree is worth getting killed or injured for.
- If unsure how to do a job safely, stop what you are doing and ask for assistance.
- Never stop learning how to work safer.
- You must avoid distractions and stay focused on the job that you are doing. If you can’t, make your supervisor aware.
- You must maintain situational awareness.
- Situational awareness is being aware of what is happening around you and whether there are actual or potential hazards that pose a threat to your health and safety and the health and safety of those around you.
- An individual’s understanding of what is happening around them is based on their own knowledge, experience, and education, so everyone’s situational awareness is unique.
- A person’s situational awareness can be further reduced in times of high workload, when under pressure to get a job done on time, or when physical and emotional issues are on your mind.
- In these situations, it is essential to maintain a high level of situational awareness in order to assess hazardous work conditions.
- Timber cutting involves numerous detailed steps to get a tree on the ground and conditions can change rapidly; if you aren’t paying attention you could fail to spot hazards or follow safe work practices.
- You must have the right attitude toward safety.
- Always take a positive attitude towards safety.
- Take personal responsibility for your own safety and that of your co-workers.
- Pay attention to training.
- Keep an eye out for hazards. Always ask, “What could go wrong here?”
- Look for opportunities to improve workplace safety.
- Set an example of a good safety attitude for others, especially new employees.
Personal Protection Equipment
Head Protection – High visibility hard hats must be worn to protect against head injuries from falling, flying or thrown objects. The hard hat should be in good condition. If a plastic hard hat is cracked, deeply scratched, or brittle, replace it. If an aluminum hard hat is damaged replace it.
Hearing Protection - Hearing protection must be worn properly and in good condition. Earplugs must be properly inserted to be effective (see illustration). Hearing protectors act as a barrier to reduce sound entering the inner ear. They may be uncomfortable at times and take some getting used to. But wearing them is your best insurance for hearing well in the future.
Eye Protection - Employees must wear approved eye protection when operating chain saws. The most common eye protection used is safety glasses and logger-type mesh screens
Leg Protection - Leg protection is mandatory when operating a chainsaw. In cases of saw kickback, leg protection can prevent serious injury. Leg protection must be made of a cut- resistant material, such as ballistic nylon, and must cover the full length of the thigh to the top of the boot on each leg. Leg protection must be replaced if the cut-resistant material has been damaged. Leg protection can be worn over your pants (chaps) or under your pants (inserts). Both types must be properly secured so they stay in place.
Hand Protection - Employees handling rough materials must wear gloves. Gloves will protect against cuts, lacerations and puncture wounds.
Foot Protection
- Each employee must wear foot protection that covers and supports the ankle, such as heavy duty logging boots.
- All employees who walk on logs must wear sharp-caulked footwear or equivalent
- Each employee who operates a chain saw must wear cut resistant foot protection that will protect the employee against contact with a running chain saw. Leather logging boots, insulated rubber pacs, and rubber boots with cut protection will meet the cut resistant requirement.
Highly visible clothing
- An employee working as a flagger must wear a hard hat and vest or other garment of high visibility colors. Warning vests and hard hats worn at night must be reflective.
Back Injury Prevention
- The first priority is size up the load and whenever possible use. Don’t be afraid to ask for assistance.
- When lifting you want to keep the load as close to the body as possible. The further the load is from the center of your spine in the low back, the greater the compressive force on the spine (vertebrae and discs). For example, a twenty-pound chainsaw held twenty inches away from the body produces about 400 pounds of compressive force on the disc at the pivot point in the low back.
- Make sure you have good footing so you don’t slip while lifting. Bend at the knees and not just from the back, while keeping the feet in a wide base of support. Keep the object as close to the body as possible, keep the back in its normal curve and lift with the legs. Remember to lower objects in the same way. Avoid twisting at the waist when lifting and lowering.
-
Lift smoothly and slowly and never jerk the load. Avoid twisting while lifting and bending forward because it places additional compressive forces on the spine and can cause back ligaments to be overstretched. When carrying a load or repositioning a load, be careful not to twist your body. Turn your body by changing the position of your feet.
- When pulling, face the object with one foot behind the other with your weight evenly distributed over both feet. Pull should come from both arms and both legs while the back should remain straight.
- Whenever possible, choose to push an object rather than pull. Face the object to avoid twisting and position your body close to the object and push with the arms and legs while keeping the back straight.
- Injuries can be caused from slips and falls. Watch your footing. Your corks should be sharp. Don’t jump from machines, vehicles, logs, etc. Maintain three points of contact. • Avoid reaching, especially when pulling. Keep hands close to the body.
Communications and Emergency Medical Plan
- Each cutter must carry a whistle on their person to call for help.
- Each cutter must carry an operable two-way radio on their person for emergency communication.
- There must be at least three cutters at each jobsite so that if a cutter suffers an injury or illness, there will be one person available to render first aid and one person available to implement the emergency medical plan.
- Less than three cutters would only be acceptable:
- when cutting at an active logging site with workers present and arrangements have been made with the logging company to include the following:
- A worker at the logging site must have compatible two-way radio communication, the radio must be operable and the radio channel used by the cutter(s) must be monitored constantly, or
- There are two cutters at the site and they both carry cell phones and have the capability of calling for assistance without leaving the injured or ill cutter.
- Each worksite must have at least one serviceable and operable two-way radio, phone, or radio/phone combination available to reach emergency service. Citizen band radios are permitted only as a secondary means of communication.
- Each worksite must have an emergency medical plan to ensure rapid emergency medical care for employees with major illnesses and injuries (see sample Emergency Medical Plan in Appendix 2). The plan must be in writing and include the following:
- Township, range, and section numbers or latitude and longitude or UMS Grid System coordinates;
- Directions by road, or escort provisions to the site;
- Telephone number of emergency medical services; and
- Provisions for emergency vehicle(s) access, when working behind locked gate(s).
First-Aid
- Each employee must have a valid first aid card. New employees not holding a valid first-aid card must be trained within six months from hiring.
- First aid kit/supplies must be available at each worksite and in each crew vehicle (see requirements for First aid Kits in Appendix 1). The first aid supplies (kit, stretcher, blanket) are stored at the following location(s):
___________________________
___________________________
Arrangement of work areas and checking worker’s well-being
Work areas must be assigned so that:
- Trees cannot fall into an adjacent occupied work area;
- The distance between work areas is at least two tree lengths of the trees being fell.
- A distance of more than two tree lengths is maintained between work areas on any slope where rolling or sliding of trees or logs is reasonably foreseeable.
- Each employee must be within visual, audible, or radio/telephone contact with another person who can assist in case of emergency.
- In any cutting operation there must be at least two employees working as a team.
- Each employee must have visual or audible signal contact with another employee at least every 30 minutes.
- The employer must establish a method of checking the employees in from the woods at the end of each shift, including operators of all movable equipment. Each immediate supervisor must account for his or her crew.
Fire Extinguishers
- Each vehicle must be equipped with at least one fire extinguisher with at least a 5/ BC rating. If fuel is being transported in the crew vehicle, the fire extinguisher must be a minimum rated 10/BC.
Overhead electrical lines clearance 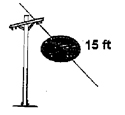
A minimum of fifteen (15) feet of clearance should be maintained between the electrical distribution line and all trees being fell. Contact the utility company before working near power lines where you are not absolutely sure of voltages and clearance requirements or need assistance in removing trees along power lines. Trees along power lines must be directionally fell away from the lines. If a tree contacts a power line, all employees must remain clear of the area until the power company ensures that there is no electrical hazard.
Seat belts (vehicles)
- All occupants of a vehicle must have their seat belt securely and tightly fastened while the vehicle is being operated.
Tools
- All cutters must carry or have in near proximity at all times at least two wedges and ax or suitable tool for driving wedges. Tools must be maintained in serviceable condition. Wedges should be checked before use to make sure they have no hairline cracks or other damage.
- A cutter must meet comply with the following requirements between April 15 and October 15 (closed season), unless the WA DNR designates different dates because of prevailing fire weather conditions:
- Must have a chemical fire extinguisher of at least eight ounce capacity, fully charged and in good working order. The fire extinguisher shall be kept in the immediate possession of the operator;
- The chain saw must have an approved exhaust system;
- Must have a shovel, which shall be kept within two minutes round-trip of the operator.
Roads
- A flagperson(s) must be assigned on roads where hazardous conditions are created from falling trees. Where there is no through traffic, such as on a dead end road, warning signs or barricades may be used instead of a flagperson(s).
Safety Meetings
We believe there is no magic formula for the prevention of injuries – hard work and perseverance are required, with the effective safety meetings being the key to a successful result.
Purpose:
To assist in the detection and elimination of unsafe conditions and work procedures. Keep lines of communication open to address safety issues.
Procedure:
The following guidelines will be followed:
- Daily meetings: These meetings should be held in accordance with the various circumstances involved or when necessity dictates. No set pattern will suit all cases. It is important, however, that the leader talk daily on injury prevention and immediately on witnessing an unsafe act.
- Monthly:
- Safety meetings must be held each time we move to a new jobsite, and at least once a month thereafter. When moving to a new jobsite, site specific hazards should be identified and discussed during the pre-job safety meeting.
- Safety meetings may be used to cover the four LSI approved trainings
- The attendance and subjects discussed shall be documented and maintained on file for one year.
Scope of Activities:
- Discuss results of monthly safety inspections.
- Review injury and near-miss investigations and reports to determine means of elimination.
- Accept and evaluate employee suggestions.
- Review job procedures and recommend improvements.
- Monitor the safety program effectiveness.
- Promote and publicize safety.
Documentation:
A form is available in the Appendix 3 to assist in documenting safety meetings.
Injury or Illness Procedures
- Procedure: Owner or lead person immediately takes charge.
- Supervise and administer first aid on a Good Samaritan basis. Activate EMS (call 911) as soon as you recognize there is a medical emergency.
- If necessary and it is safe to do so, get stretcher and carry injured person(s) to the nearest road or landing.
- In the event of a fatality, probable fatality or in-patient hospitalization of any employee, the employer must report the incident to the Department of Labor and Industries within 8 hours. To report, contact your nearest labor and industries office by phone or in person, or call 800-423-7233. Do not move anything, unless absolutely necessary, pending an investigation.
- Documentation:We are required to conduct a preliminary investigation for all serious injuries; evaluate the facts related to the cause of the incident; and document the findings. The investigation will be conducted by a person appointed by management, the immediate supervisor of the injured person(s), employee representative and any witnesses. The findings shall be documented on our Incident Investigation Report form (see Appendix 6) and discussed at the next safety meeting. The primary purpose of the investigation is to find the cause(s) of an accident and prevent similar occurrences, not to fix blame.
- Accidents and Near Misses:
- All accidents and near misses (close calls) must be reported to your supervisor and should be investigated (see Appendix 5 Accident/Near Miss Report form).
- Review findings at monthly safety meetings or sooner if the situation warrants.
- Share near miss and accident investigation findings with all employees.
Blood Borne Disease Exposure
We have first aid qualified workers but we do not have "designated" first aiders. First aid at the job site is done on a Good Samaritan (voluntary) basis. A patient’s body fluid may carry diseases such as HIV and Hepatitis. If you choose to provide first aid, you should protect yourself from exposure to blood and body fluids by the use of barriers. Appropriate barriers may include protective gloves, mouth barrier and eye protection. If you are involved in a situation involving blood and/or body fluids, you should:
- Avoid contact with blood/OPIM (other potentially infectious materials) by letting the victim help as much as possible, and using barriers.
- Remove clothing, etc. with blood on it after rendering help.
- Wash thoroughly with soap and water to remove blood/OPIM.
- Consult your physician.
Employee Safety Orientation and Training Record
Employee ___________________
Date ________________
Trainer ________________
This checklist is a guideline for conducting new employee safety orientation. The following policies and procedures must be explained before a new employee begins work. Place a check in each box to indicate that the subject has been covered.
__ 1. Review “Safety Policy & Commitment” section
__ 2. Review ‘Safety Disciplinary Policy” section
__ 3. Review “Safety Responsibilities” (Employer, Supervisor, Employee sections).
__ 4. Review “General Safety Information and Rules” section including:
- Personal Protective Equipment o Back Injury Prevention
- Communications and Emergency Plan
- First –aid
- Arrangements of works areas and checking worker’s well-being
- Fire extinguishers
- Overhead electrical lines clearance
- Seat belts
- Tools
- Roads
__ 5. Review “Safety Meetings” section
__ 6. Review “Injury or Illness Procedures” section.
__ 7. Review “Blood Borne Disease Exposure” section.
__ 8. Review Hazard Communication Program (see written program).
__ 9. Review Outdoor Heat Exposure Safety Program (see written program).
__ 10. Explain the process for training “new cutters” and experienced cutters.
I have received and understand the above information:
Employee's signature ____________________
Date: ________________
Cutter Training Curriculum
Cutter’s Name:
Trainer’s Name(s):
I have received and understand the information listed below:
Cutter’s signature:
Date:
After the trainer explains the information, place a mark in each box below. Many of the categories also require the trainee to demonstrate their ability to correctly perform the technique(s). Do not check the box until the trainee has demonstrated that he can perform the technique(s) correctly.
__ Required personal protective equipment - Explained
- High visibility hard hat
- Caulk boots
- Eye Protection
- Leg Protection
- Hearing protection
- Gloves when handling rough materials
__ Safe Chain Saw Use - Explained and demonstrated correctly
Cuts are the most common type of injury caused by chain saws. They can range from minor hand injuries, while filing the chain, to major amputations or death. Cuts can occur if you slip or fall and accidentally touch the chain. The most serious cuts are caused by kickbacks. A saw can "kickback" with surprising force in less than 1/5 of a second. There is no time to react and, if you're poorly positioned, the resulting injuries can be severe.
Cuts can be reduced by following these safety guidelines:
- Power saws must be inspected daily when in use and kept in good repair.
- Keep the saw chain sharp and properly tensioned. A dull and or improperly tensioned chain is more likely to grab and cause a kickback.
- Adjust your saw so that, when idling, the chain is stopped.
- The chain brake must be in good working order. Perform regular maintenance and test it frequently.
- Engage the chain brake before starting the saw or start the saw on the ground, log or where firmly supported. Don’t drop start the saw.
- Wear personal protective equipment.
- When carrying the saw, keep the chain bar to the rear. If you stumble, you won't fall on the chain. Also, the dogs and chain won't hang up in brush.
- The chain saw must be shut down or the chain brake engaged whenever a saw is carried further than 50 feet or whenever terrain, brush and slippery surfaces create a hazard. Note: When carrying the chain saw on your shoulder, the chain saw must be shut down but the chain brake doesn’t need to be engaged.
- Don't work off-balance or with poor footing. Learn to use the saw equally well, right- or left-handed, to avoid working in awkward positions.
- Maintain a firm, but not tense, grip with both hands on the saw while keeping your thumb under the handle. This will stop the hand from slipping onto the chain in cases of kickback.
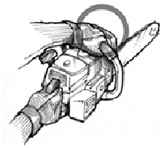
- Don't jerk the saw. Jerking the saw can cause loss of control, uncertain footing and possible back, arm or shoulder strain.
Remember, the tip of the bar causes most kickbacks. Know where the tip of the bar is at all times, especially when bucking and limbing.
- Hold the saw firmly against your body when using it in the boring position. This will reduce impact from kickbacks. Don't bore unnecessarily.
- Avoid standing directly behind the saw or straddle the saw. Work to one side to minimize injury from kickbacks and give yourself more time to react.
- Do not cut directly overhead because it is very difficult to control the saw.
- With the exception of chain brakes and throttle lockouts, chain saws contain few mechanical safeguards. For safe operation, you must develop good saw handling skills.
__ General Work Procedures - Explained
- A competent person, properly experienced in this type of work, must be placed in charge of falling and bucking operations. Inexperienced workers must not be allowed to fall timber, buck logs or windfalls unless working under the direct supervision of an experienced cutter.
- The person in charge of cutting crews must regularly inspect the work of cutting crews and is responsible to ensure the work is performed in a proper and safe manner.
- If a cutter has determined a tree cannot be safely fell, the work must stop until the cutter has conferred with a supervisor or an experienced cutter and determined the safest possible work method or procedure.
Lodged trees must be clearly marked and identified by a predetermined method and all persons in the area must be instructed not to pass or work within two tree lengths of the trees except to ground them.
- Trees with face cuts and/or backcuts must not be left standing unless all the following conditions are met:
- cutter clearly marks the tree,
- discontinues work in the hazardous area,
- notifies other workers who might be endangered;
- and takes appropriate measures to ensure that the tree is safely fell before other work is undertaken in the hazardous area. DON'T work under hung up/cut up trees! Don’t turn your back on a hung up/cut up tree.
- A flagperson(s) must be assigned on roads where hazardous conditions are created from falling trees. Where there is no through traffic, such as a dead end road, warning signs or barricades may be used instead of flagperson(s).
- Changing weather conditions can create additional difficulties for cutters, especially when those conditions change unexpectedly. Wind, rain, fog and snow are a part of logging in Washington. If adverse weather or darkness creates unsafe conditions, all work must be stopped.
- If the wind is strong enough to affect safety or control of trees, stop work until the wind subsides. If the wind is strong enough such that there are large flying branches, move to a safe location as soon as possible.
- Trees along power lines must be directionally fell away from the lines. If a tree does contact a power line, all employees must remain clear of the area until the power company ensures that there is no electrical hazard.
- The minimum distance to be maintained between a working faller and any other worker is two tree lengths. Exception: This rule does not apply to a team of cutters working on the same tree.
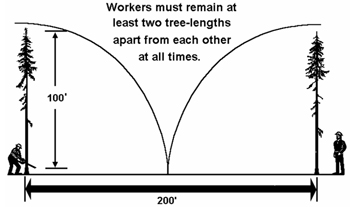
- While manual falling is in progress, all logging machines must be operated at least two tree lengths away from trees being manually fell. Exception: This provision does not apply to logging machines performing tree pulling operations or logging machines called upon by the cutter to ground hazard trees. All cutters must be notified of the logging machines entrance into the falling area and all falling within two tree lengths of the logging machine must stop.
- Employees must not approach a cutter closer than two tree lengths of the trees being felled until the cutter has acknowledged it is safe to do so.
- A cutter must not be placed on a hillside immediately below another cutter or below logging operations where there is probable danger. Do not stack cutters on a hillside. The employer must assign work areas so that trees cannot fall, slide or roll into another occupied work area.
- Cutters must be informed of the movement and location of other employees placed, passing, or approaching the vicinity of trees being fell.
Falling and bucking difficulties. During the course of a work day a cutter can encounter situations that may be considered "difficult." It could be a problem snag, an extreme leaner or a jackpot. With experience, skill and imagination most of these situations are resolved. However, cutters must never overestimate their ability.
In difficult situations assess the problem carefully. Consider the complications and the alternatives. If there is any doubt as to how to get the job done safely, don’t do it. Stop and ask your supervisor or another cutter for advice and/or help.
__ Falling – Planning - Explained
- Before starting to fall timber, you should have a thorough knowledge of the area and of the work procedures used at your logging operation. You must know your position in relation to roads in use and to other equipment and workers in the area.
-
Where felled trees are likely to roll and endanger workers, cutting must proceed from the bottom toward the top of the slope, and uphill from previously felled timber.
- If there is a possibility that the tree could slide back past the stump, it must not be felled directly uphill. If you have to fall trees uphill, plan accordingly. Your escape route should take you far enough away to clear even the limbs, in case the tree slides back. When trees must be felled up- hill, they must be felled at an angle to prevent the possibility of the tree sliding or rolling toward workers. If falling trees over a hump in the ground, remember the butt could come down and back as well.
- When laying out and cutting your strip, there are several things to consider including the lay of the ground and slope, the timber stand's prevailing lean, timber size and height, felling direction to accommodate yarding, and whether you’ll be required to buck the trees fell. The best position will allow timber to fall into the clear.
- Before falling or bucking, check for defects such as rot and cat faces, widowmakers or other overhead material, location of other trees, lean of the tree, wind, etc. If unsafe, stop and ask for another cutter's help or advice with any question about the safe cutting or bucking of a tree or snag.
- While felling a tree, avoid cutting from under the lean.
- Trees must be fell into the open whenever conditions permit. Brushing other trees creates widowmakers, hang-ups, and material being thrown back toward the cutter.
- In all cases, you must assess each tree or snag to be felled. Check for material lying on the ground in the immediate area. Will any logs, saplings or chunks be disturbed by the falling tree and, on contact, create a hazard? Check to see if other standing trees or snags will be involved when the tree being cut falls.
Plan your escape route and an alternative route in case the tree does not fall according to plan. Choose and clear out an escape path in back of, uphill and at an angle away from the stump. Your escape path must allow you to move at least 10 feet from the stump.
- Brush-out at the base of the tree and along your escape route from the base of the tree. Brushing-out means clearing or bucking all nearby saplings, chunks or trees that may fly back and strike you when the tree is felled. Brushing-out permits the free and safe use of tools. It removes kickback hazards and allows a quick and unobstructed path to safety.
- Make sure you have all the tools you'll need for the job, including required ax, wedges and enough fuel in the saw to finish falling the tree.
- Safe falling means planning ahead. It means:
- ensuring that all workers are clear of the hazardous area before falling begins;
- falling each tree in the safest possible manner; falling each tree so that it can be safely bucked when required; and having an escape path
__ The Undercut – Explained and demonstrated correctly
The key to good falling is the undercut. When properly sawn, the undercut will allow the tree to fall freely in a chosen direction. More time spent on a good undercut will avoid many problems later. A clean, uniform undercut must be used on all trees.
The following guide should be used:
- All trees that are over six inches in diameter at breast height must have undercuts.
- The undercut should be one-fourth to one-third of the tree's diameter. Note: For a short stubby snag, the depth of the undercut may need to be about one-half the diameter.
- Undercut opening must be wide enough that the tree is committed to fall properly. The face opening of the undercut should be no less than one-fifth the diameter of the tree. In large trees with "bell" butts, it may be necessary to remove some of the flare to allow easier placement of an undercut.
- The horizontal part of the undercut must be level (except when using an open face undercut). The two cuts that form the undercut must not cross where they meet, except where a Dutchman (swing cut) is required on either side of the cut. (See “Unintentional Dutchman”)
- The undercut must not be made while other workers are in an area into which the tree could fall.
__ The Backcut - Explained and demonstrated correctly
- The backcut must be level and sawn in slightly above the horizontal plane of the undercut. This forms an anti-kickback step.
- Enough holding wood must be left to maintain control of the tree so that it does not break, slip or twist off the stump and fall in an unplanned direction. In general, the width of the holding wood should be about one-tenth the tree diameter.
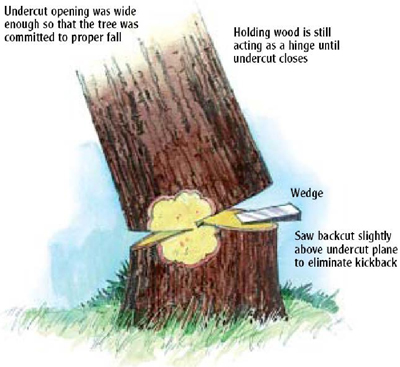
- Cutting holding wood instead of using wedges is prohibited. Swing cuts can only be used by an experienced cutter. Check corners often so you don't cut off a corner.
- In trees with thick bark or those with an accumulation of moss or duff around the butt, it may be necessary to clean the tree to see the amount of holding wood remaining.
- When the tree lifts and is committed to fall, use your escape path and quickly move a safe distance away from the stump and get behind another tree if possible. You should move at least 10 feet from the stump, but there may be an occasional exception. For example, you need to stand on a ledge to fall a tree and the terrain prevents you from moving 10 feet away. Always remember that most serious accidents occur within 10 feet of the stump. Watch the tree and neighboring trees as it starts to fall for any material being dislodged. Keep watching for falling material even after the tree has hit the ground. Neighboring trees that may have been brushed will still be swaying and may dislodge or throw material into the work area. Do not move to the stump or next tree until you have finished your safety check. Note: In some situations, a cutter may have to briefly remain at the stump after the tree is committed to fall in order to complete the backcut.
__ Unintentional "Dutchman" - Explained
An unintentional Dutchman is created when the horizontal cut extends past the sloping cut. The result of unintentional "Dutchman" is that, as the tree starts to fall, the "Dutchman" closes, usually breaking the holding wood and forcing the tree away from its intended direction of fall.
The tree may "barber-chair" or fall among other adjacent standing trees or snags and hang-up. Broken tree limbs or tops may be thrown back toward the cutter in this case.
All trees will barberchair, but the following species should be the most suspect:
- Cottonwood, alder, red cedar, spruce, hemlock, maple
Make sure that you are always cutting with a sharp chain so that you can complete the backcut as quickly as possible.
Many accident investigations have determined that an unintentional "Dutchman" was a contributing factor to the accident.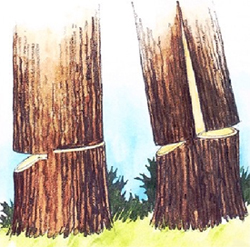
Causes of "Barber-Chair"
- lack of proper undercut;
- heavy lean or pressure on a tree;
- single saw kerf in the undercut;
- failing to side-cut or side-bore leaners;
- natural splits, shakes or other deformities, wind; and
- tree falling across a hog-back, stub snag or making contact with standing timber.
__ Intentional "Dutchman" (Swingcut) - Explained
An intentional "Dutchman" has been used by cutters to overcome some falling problems. When a tree could not be "pulled" or "thrown" by other means, cutters have used an intentional "Dutchman," but only after understanding and evaluating the hazards involved. Even for the most seasoned and skillful cutter, the amount of pull or throw created by the "Dutchman" cannot always be determined. This could mean losing control of the tree. For this reason, the use of an intentional "Dutchman" is not recommended, except under special conditions.
__ Falling Danger Trees - Explained
Where possible, danger trees must be felled:
- progressively with the falling of other timber;
- before falling live trees; and
- into open areas.
Danger trees that will reach the work area should be fell as soon as an opening will permit it. Don’t overlook danger trees along cutting lines or in leave areas. If it is unsafe to hand fall a danger tree, your supervisor must prearrange other methods such as the use of explosives or machinery, so you don’t have to bypass a danger tree. Avoid wedging a danger tree as it may break off or material may fall. Fall danger trees in the direction of lean whenever possible.
Avoid "pushing" a danger tree, other than to overcome a falling difficulty. The top may break off or the danger tree may buckle in the middle and fall in your direction. The whole danger tree could sway and fall back onto the faller. Never push a danger tree with another danger tree. Most danger trees can be felled progressively with other timber.
A cutter must not fall a danger tree or snag alone when at least two persons are necessary to minimize hazards.
As a cutter, it is imperative that you be able to identify danger trees in your surrounding work area that would create a hazard. Because timber fallers are usually the first workers to approach a danger tree or snag during the harvest activity, they are at greatest risk of having an accident.
Danger tree is defined as (WAC definition in the Safety Standards for Logging Operations): Any tree of any height, dead or alive, that poses a hazard to workers because of rot, root, stem or limb damage, lean, or any other observable condition created by natural process or man-made activity.
Some trees, although dead, may not be a danger trees if they have a sound top, trunk, and roots. Identifying these dead but safe trees requires careful observation. Mortality may have been caused by canker, diseases, insects, fire, adverse weather or lightning. Needle and small twig retention is evidence of recent death, which may be an indicator of stability. Fire-scorched trees may remain stable for many years if the trunk and root systems are not badly burned.
However, not all fire-scarred trees may be safe. Pre-existing defects may be charred and difficult to detect, rendering a tree that was dangerous before the fire even more dangerous afterward.
If the fire burned the root system, it may be damaged, and need to be classified as a danger tree. Similarly, trees infected with root rots have weakened root systems that automatically classify them as a danger tree. Root disease pockets can be identified by looking for trees with fading crowns that are adjacent to windthrown trees with root decay. The windthrown trees will usually have very small root balls.
Danger trees could also be live or dead trees with unstable tops or upper portions. Although the roots and main portions of the trunk are sound, these reserve trees pose high hazard because of defect in live or dead wood higher up in the tree. Ground vibration from falling trees, wind, flying debris, heavy equipment or other industrial activity can dislodge slabs, chunks, limbs, or the entire upper portion of the tree.
Danger trees could also be live or dead with unstable trunk or roots, with or without bark. This includes “soft” snags as well as live trees with unstable roots caused by root rot or fire. They are considered the most dangerous type. Unexpected collapse could occur from any portion of the roots or trunk.
If the intent is to leave a danger tree in a logging unit, then workers must remain a safe distance away. A safe distance would be outside the potential hazard area of the danger tree (see examples below).
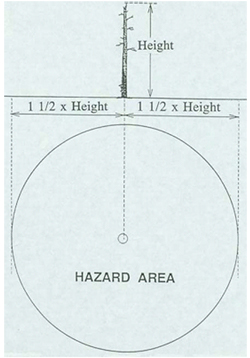

__ Common Falling Difficulties - Explained and demonstrated correctly
Tree sits back. Just as the cutter is completing the backcut, the tree starts to sit back on the bar. This can happen because:
- the cutter misjudged the tree's lean or weight of limbs;
- the stump contained hidden rot;
- an unexpected gust of wind took it backwards; or
- the cutter didn't start a wedge in the backcut as it was being sawn.
If enough holding wood remains, the tree can still be wedged over in its intended direction. Be sure to clean the bark away above and below the backcut, to allow wedges to bear on solid wood.
Sometimes the tree may be leaning backwards heavily and you can't start wedges in the backcut. In this case, you have three choices:
- Re-fall the tree.
- "Push" the tree over by falling another tree into it.
- Notify your "buddy" of the problem, then notify your supervisor.
Re-Fall the Tree. If you decide on option one through three, then you must take extra care when working on the cut-up tree. Also, because the falling plan has now changed, you must clear another escape route before starting to cut again. The best way to do this is to face the cut-up tree and brush-out the escape route toward it, always keeping an eye on the tree in case it starts to fall. Never Turn Your Back on a Cut-up Tree!
After the escape route is cleared, you can then begin re-falling the tree using a second undercut.
There are different methods that could be used, however the following method will allow for most control being maintained because a proper undercut, backcut and holding wood can be sawn in above the original cuts. Maintain the vertical distance between the first falling cuts and the new falling cuts to at least the distance of the tree's diameter. A danger exists that a vertical split can occur between the first and second set of cuts.
- "Pushing" Trees."Pushing" a tree by falling another into it is a dangerous practice. It should be done only to overcome a falling difficulty, such as when:
- the tree has settled back and the cutter is unable to start wedges;
- the tree is limb-tied to another;
- the tree is leaning against another.
"Pushing" is dangerous because a gust of wind or vibration from nearby equipment can cause the cut-up tree to fall in an unexpected direction. If the cutter only brushes the tree being pushed, that tree may sway and fall over into the area where the cutter is standing. Also, dry tops or limbs can be broken off and thrown back toward the cutter.
Guidelines for "Pushing" Trees:
- Assess the situation carefully. The pusher tree should be at a good angle no more than 20 degrees off the imaginary center line behind the tree being pushed.
- Locate a safe escape route and an alternative escape route if necessary. While making the escape route, face the cut-up tree and brush-out toward it. Never turn your back on a cut-up tree!
- Face the cut-up tree when sawing undercuts and backcuts in the pusher tree.
- Take extra care regarding undercuts and holding wood. Make sure you have control of both trees. Check for "Dutchman."
- Direct all your efforts to falling the cut-up tree safely. Never do unrelated work under or in the area of a cut-up tree.
- Notify your "Buddy" and Supervisor. If, for some reason, you can't fall the hazardous tree, you must adhere to the following rules.
- Trees with face cuts and/or backcuts must not be left standing unless all the following conditions are met:
- cutter clearly marks the tree,
- discontinues work in the hazardous area,
- notifies other workers who might be endangered;
- and takes appropriate measures to ensure that the tree is safely fell before other work is undertaken in the hazardous area. DON'T work under hung up/cut up trees! Don’t turn your back on a hung up/cut up tree.
- If you don't feel qualified to deal with a particular falling difficulty, ask for help. It is not a mark against you. Knowing the limit of your skills is one of the signs of a good cutter. Much better to ask for help early before that minor difficulty becomes a serious problem.
__ Leaners - Explained
Most trees have some lean. If the lean is slight and in the same direction as the falling face opened up, falling is straightforward. However, if the tree is leaning heavily, or must be felled against the lean, the situation is more hazardous and requires special consideration.
- While felling a tree, avoid cutting from under the lean.
__ Heavy leaners – Explained and demonstrated correctly
A tree with a heavy lean develops enormous tension in the wood directly behind the lean. When an undercut is sawn into the tree in the direction of the lean this tension increases. As soon as a conventional backcut is started, the tension is immediately relieved and the tree starts to fall. However, too much holding wood remains and, instead of the holding wood breaking off normally, the tree trunk will split vertically from where the backcut was started. A huge slab will develop and kick backward at the same time, causing a "barber- chair." This whole process can take only a few seconds. The results can be disastrous for an unprepared cutter.
In falling heavy leaners, do not attempt a deep undercut. The undercut should be no more than one-quarter of the tree's diameter. To prevent barber-chairing, leave the part of the wood which is most under tension, located behind the lean, until more of the holding wood is sawn out. Two methods may be used in removing the excess holding wood.
Side-notching. After the undercut block has been removed, the sides of the tree are sidecut or sidebored. The remaining holding wood of the backcut will be sawn faster, with less likelihood of the tree splitting.
Boring the backcut. After the undercut block has been removed, the tip of the saw bar is bored into the tree above the horizontal plane of the undercut. The faller must ensure that they leave a few inches of holding wood between the start of the boring cut and the back of the undercut. It may be necessary to bore in from both sides if the tree is wider than the length of the bar.
The saw is worked backwards, cutting from the inside out, until the point is reached where the normal backcut would have been started.
While boring, the wood directly behind the lean will be under enormous tension, as all other holding wood has been severed. Trees have been known to fall before the saw has cut through, pulling a large section of root out of the ground.
__ Extreme leaners and leaners with splits in the butt – Explained
For extreme leaners and leaners with splits in the butt, the faller is advised not to bore through the butt. The bar will get struck in the super-compressed, tensioned or split wood of the butt.
Those types of leaners can be extremely hazardous. The following is a procedure to deal with them:
- Make sure the lay of the tree (the direction it wants to go) is unobstructed.
- Don't try to swing the tree.
- Brush-out an escape route and an alternative route if necessary.
- Put in as deep an undercut as possible, one-eighth to one-quarter of the tree's diameter.
- Cut the corners of the backcut. Start with the corner opposite to your escape route. Don't cut too close to the corners, however, as the saw may get struck.
- Start cutting the backcut. Cut as rapidly as possible.
- Watch for barber-chair or root pull. Sections of root can be pulled out and flail around.
- Continue cutting until the tree breaks off and begins to fall.
If the tree is too hazardous to be felled with the above procedure, an alternative method, such as blasting, should be used.
___ Falling Against the Lean – Explained and demonstrated correctly
On occasion, falling against the lean may be necessary to:
- keep the tree away from sensitive areas such as streams;
- avoid needless breakage;
- place the tree in a favorable bucking position;
- avoid falling the tree into other adjacent standing trees;
- keep the tree from falling on a road grade;
- keep the tree in lead to accommodate yarding;
- avoid crossing the lead or falling pattern.
Making strict guidelines for falling a tree against its lean is difficult because of the variations in lean, height, diameter, species, terrain, and conditions. In extremely cold weather, for example, frozen wood becomes brittle and undependable as holding wood. Falling against the lean under these conditions is hazardous.
Make a habit of plumbing each tree before falling, even if you feel sure you know where the lean is.
A large tree with heavy lean may be felled against its lean by inserting wedges in the kerf of the backcut and driving the wedges alternately as the backcut is sawn. In some cases, a hydraulic jack used in conjunction with wedges would be an advantage. Always use eye protection when driving wedges. Keep your head above the wedge or away from its path should the wedge come out of a cut.
Most trees can be felled away from their lean by using normal falling wedges and by keeping extra holding wood.
On small timber, there may not be enough room for the saw bar and wedges.
- Saw the backcut first.
- Remove the saw and drive in wedges before the undercut is sawn out.
- Put in the undercut.
- Keep only enough holding wood as is necessary.
- Finish falling with wedges.
In some cases the tree may be leaning in two directions (see illustration). Be careful not to cut off the holding wood on the leaning side; the tree may settle on the saw bar. More holding wood is maintained opposite to any side lean. This will help draw the tree away from any side lean.
__ Falling Against the Lean – Using a hydraulic jack - Explained
Hydraulic jacks can be used to solve a variety of falling difficulties. A jack (or jacks) may be necessary to lift and force a large tree against its lean.
Points to Remember:
- When necessary, two workers must be present at the tree during hydraulic tree jacking to lend assistance.
- Make sure the jack is large enough for the job. All hydraulic tree jacks must be equipped with a check valve and the pump must be equipped with an operable pressure gauge.
- Jack plates must be used with hydraulic tree jacks and the base plate must be seated on solid wood inside the bark ring as close to level as possible.
- All boring cuts should be level.
- Stand to one side when jacking.
- Wedges must be used as a follow-up method while using tree jacks, and continuously moved in as the tree is jacked.
- Jacking a tree straight uphill is prohibited when the tree may slide back past the stump.
- On slopes over 50% grade, tree(s) must at least be quartered to a degree that prevents employees from being exposed to the possibility of sliding or rolling trees or logs.
__ Trees Tied Together – Explained and demonstrated correctly
Trees standing close together and tied in by limbs should be felled together (see illustration). If the cutter cannot see all the limbs they must assume the trees are tied together and, therefore, should be felled together. Under such conditions, if wedges are used to drop the front tree, a limb or dry top may break and fall, endangering the cutter.
Procedure
- Cut up the front tree and place wedge. Make sure you maintain enough holding wood.
- Start falling the second tree, allowing both trees to fall together.
Each situation of this kind must be carefully considered. If it appears particularly hazardous, talk with your supervisor first.
__ Hang-ups - Explained
Many fatal-accident investigations reveal that the fallers involved had created "hang-ups" in their area. They were working under one of these hang-ups when struck by it.
Hang-ups are caused by:
- poor planning of the work area;
- loss of directional control.
Losing control of the falling tree can be caused by:
- cutting off the corner of holding wood;
- stump pull or rot;
- "Dutchman" left in undercut;
- wind;
- failing to use wedges where required.
If trees are hung-up in another tree, special care must be taken when falling the tree supporting those that are hung-up.
- Assess the situation carefully.
- If possible, keep the trunk of the supporting tree between you and the hang-up(s). In other words, if the hang-up is held by limbs on one side of the supporting tree, fall the supporting tree from the opposite side.
- If you are on steep ground, and the hang-ups are on the uphill side of the supporting tree, fall the tree by blasting or another safe alternative method.
Man-made hang-ups can be prevented by careful planning and the use of proper felling techniques.
__ Windfalls and windfall roots - Explained
Windfall roots should not be approached from the root wad side. Avoid standing directly behind or downhill of a root wad. Never assume that a windfall root wad is safe because it has been down for a long time. It may still flip over unexpectedly. When bucking off a root wad, leave a short log on the root wad to prevent it from tipping toward you.
__ Burned Timber - Explained
Falling and bucking burned timber requires extreme caution. Roots of some trees could be burned off or they may have burned out centers. The trees may fall as soon as they are exposed to wind. The falling face should be kept straight.
Bark may be loosened by fire and fall unexpectedly. Walking on burned logs is more dangerous because support limbs may be weakened or partly burned off. Burned holes and exposed roots create additional tripping hazards. Large rocks, long butts and chunks may roll downhill after fire has undermined their support.
__ Bucking – Explained and demonstrated correctly
- Before bucking a tree/log or blowdown/rootwad, look for: side bind, pivot points, elevated butts, and tops that could cause log movement.
- Clear an escape path so you can get away if a log moves. When bucking, never have your back up against a solid object, such as a root wad, large blowdown, or rock bluff, that would block your escape path. Your first step is the most important, so always have good footing and maintain your balance. Watch for limbs, saplings, or vine maple that could spring back when bucked off. Always stand on the uphill side of a log that could roll.
- Determine whether the log can be bucked safely before starting the job. Remember, no tree or log is worth getting hurt for! If unsure how to do your job safely, stop and ask another cutter for assistance and or advice.
- Never work in an area where bucking activity might pose a hazard to yourself or other workers. The hazard might come from falling snags, branches, rolling logs or the movement of equipment or material.
- Avoid bucking "Runaways" located below logs which could roll or slide.
- Ensure all workers are clear of the hazardous area before bucking.
- Examine the tree before making a cut to determine which way the log may roll, drop or swing when the cut is completed.
- Make sure all obstructions to safe bucking and all escape routes are cleared before bucking.
- Cut only from a position that will not expose you to a risk of injury.
- Check the soundness of the log. Look for pivot points and natural skids.
- Never start a bucking cut if you consider the log to be in a dangerous position.
- Never start a bucking cut if there's a chance you can't finish it.
- If it becomes too dangerous to complete a cut, the log must be marked and identified by a pre-determined method.
- Keep a firm grip on the saw with both hands. Instead of over-extending or holding the saw in one hand, re-position yourself. One hand operation should only be used when two handed operation creates a greater hazard.
- Cutters should not use the chain saw to cut directly overhead or at a distance that would require the operator to relinquish a safe grip on the saw.
- Choose cuts and log lengths that enable you to avoid hazards caused by a poorly-chosen cut.
- Always buck from the high side of the log.
- Never buck below logs previously bucked.
- Two or more persons should not buck a tree at the same time if the release will result in movement.
- If a tree is lying in a position that makes it too dangerous to buck at a desirable length, buck it at a safe length.
- When a falling tree brushes a snag, or other weak, unstable tree, leave the tree unbucked until the snag or defective tree is felled.
- Always be on the lookout for limbs or other objects hanging above in standing limber.
- Only experienced cutters should buck windfalls.
- Buck the bottom windfalls of a "jackpot" first to avoid top logs or material from rolling.
- Watch for loose bark when walking on windfalls; it could cause a serious fall.
__ Bind – Explained and demonstrated correctly
Bind can be expected in most felled trees. Bind is made worse by uneven terrain and other material already on the ground. Bind can be present in combinations of top and side bind, or bottom and side bind.
Many serious accidents have occurred because cutters failed to recognize side bind while bucking. They positioned themselves on the side to which the bucked log "sprung" or swung upon release. When safe, buck from the side that is away from the bind, and take out the bind at the safest spot along the tree/blowdown.
The best defense a cutter has to avoid injury and equipment damage is to examine the felled tree carefully. Determine any bind which may be present and what will happen when the bucked log is released. In general, you should start by cutting compression wood and finish by cutting the tension wood. A wedge shaped cut may need to be made if the tree is under a heavy bind.
__ Pivot Points - Explained
A pivot point is any feature on the ground that may cause a falling tree or log to react in an unexpected manner. Pivot points can be stumps, rocks or any protrusion that affects a log's balance or natural tendency to roll. They're usually encountered in bucking and can be dangerous if not recognized.
As a bucked log is released, an unseen pivot point could cause one end of the log to slide or roll downhill and the other end to move uphill. If the cutter hasn't noticed the pivot and planned accordingly, they could be seriously injured.
__ Limbing – Explained and demonstrated correctly
- Use enough bar when limbing. Remember: the end of the bar and chain causes most kickbacks.
- Be ready for limbs under tension. These may try to flip the saw toward you as the limb is sawn off.
- Avoid touching other limbs with the backside or nose of the chain.
__ Boring – Explained and demonstrated correctly
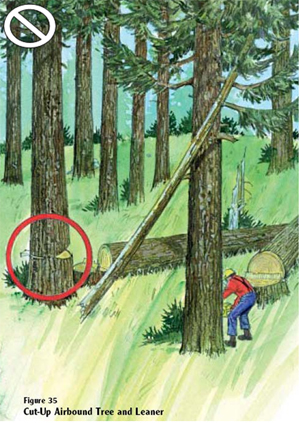
Boring is useful in certain specific situations when falling heavy leaners, for example, or in bucking where there is excessive bind. However, boring can be dangerous. If proper procedures aren’t followed, boring can cause severe kickback.
Points to Remember:
- Make sure of firm footing.
- Keep both hands on the saw.
- Hold the saw close to your body, but still to one side.
- Don’t bore unnecessarily.
__ Cut-Up Trees - Explained
Many investigations of fatal accidents reveal that the fallers who were killed had numerous cut-up trees in their working area. The "cut-ups" were sitting back on a wedge or on the stump until one of them came down unexpectedly.
Cut-up trees are death traps. They can be felled by:
- a gust of wind;
- the wind dying down;
- vibration of other felled trees;
- vibration of moving equipment;
- contact by skidding equipment;
- contact by another falling tree.
__ Domino Falling - Explained
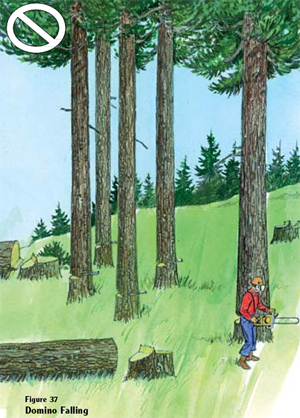
Domino falling is an extremely dangerous work practice. Usually confined to small timber, it has taken many lives in the logging industry. Domino falling of trees, including danger trees, is prohibited. Domino falling does not include the falling of a single danger tree by falling another tree into it to overcome a falling difficulty.
Domino felling is defined as the partial cutting of multiple tree which are left standing and then pushed over with a pusher tree.
Accident investigations have revealed that, in some cases, cutter had several trees cut up and left standing. In each case, the cutter intended to push the cut- up trees over with a pusher tree. Unfortunately, one of the cut-ups came down unexpectedly.
In some cases, the cut-up tree came down and killed the cutter before the cutter was able to drop the pusher tree. In others, the pusher tree caused one or more of the cut-up trees to fall back on the cutter. Domino falling is dangerous. Don't do it. Don't condone any fellow worker who uses domino falling.
Hazard Communication Program Overview
Purpose:
The purpose of the Hazard Communication Program is to ensure that the hazards of all chemicals produced or imported by chemical manufacturers or importers are evaluated, and that information concerning their hazards is transmitted to affected employers and employees before they use the products.
Procedure:
- Inventory Lists - Know the hazardous chemicals in your workplace that are a potential physical or health hazard. Make an inventory list of these hazardous chemicals; this list must be a part of your written program.
- MSDS - Make sure there is a material safety data sheet (MSDS) for each chemical and that the inventory list and labeling system reference the corresponding MSDS for each chemical.
- Labeling System - Each container entering the workplace must be properly labeled with the identity of the product, the hazard warning, and the name and address of the manufacturer.
- Information and Training - Determine appropriate ways in which to inform and train employees on the specific chemicals in your workplace and their hazards.
- Written Program - Develop, implement and maintain a comprehensive written hazard communication program at the workplace that includes provisions for container labeling, material safety data sheets, and an employee training program.
Employees must be made aware of where hazardous chemicals are used in their work areas. They also must be informed of the requirements of the Hazard Communication Standard, the availability and location of the written program, the list of hazardous chemicals, and the material safety data sheets.
The safety and health regulations specifically requires employers to train employees in the protective practices implemented in their workplace, the labeling system used, how to obtain and use MSDS's, the physical and health hazards of the chemicals, and the recognition, avoidance and prevention of accidental entrance of hazardous chemicals into the work environment.
Written Hazard Communication Program
General: It is our policy to provide and maintain a safe and healthy workplace for all employees including those who work with potentially hazardous chemicals.
If you work with or around potentially hazardous chemicals, this program affects you. The Hazard Communication Standard is intended to inform you of any potential chemical hazards from products you may come in contact with at the jobsite.
Container Labeling:
All containers of chemical products received at this company, and all containers used as secondary containers, will contain a label listing their hazards, both physical and health hazards. If the label is missing, contact (Add name or title of responsible person here) so that he/she may determine what the product is that has been received, and where it should be stored. DO NOT ATTEMPT TO USE ANY CHEMICAL THAT IS NOT READILY IDENTIFIABLE.
Material Safety Data Sheets (MSDS):
(Add name or title of responsible person here) has the MSDS on file from the various chemical manufacturers for all hazardous chemicals used in connection with this workplace. The MSDS sheets list information available about any particular chemical: health hazards, emergency and first aid procedures, how the chemical could enter the body, the safe handling and use of the chemical, name of the manufacturer, etc. The The MSDS file may be found in these locations:
- (Enter location here)
- (Enter location here)
Employee Information and Training:
(Add name or title of responsible person here) will provide training to all employees and new hires on the proper use of hazardous chemicals and potential hazards. They will be responsible for providing the following informational training to all employees:
- Hazardous chemicals present in the workplace.
- Location of the various chemicals.
- Emergency procedures in case of contact with hazardous chemicals.
- How to read labels.
- Location of the MSDS files and how to read MSDS.
- Symptoms of over-exposure and personal protective measures to be used.
- Non-routine tasks that may be encountered.
Hazardous Materials Inventory List:
Note: Hazardous chemicals include such things as: diesel, gasoline, motor oil, bar oil, 2 cycle oil, etc.
1.
2.
3.
4.
5.
6.
Outdoor Heat Exposure Safety Program
As your employer, we are responsible to determine whether we have employees who may work under conditions that increase the risk of developing heat related illness. The main environmental factors include: air temperature, relative humidity, radiant heat from the sun, conductive heat sources such as the ground, air movement and workload severity and duration. Generally, any employee who works in moderate to high temperature and/or humidity conditions, and performs physical activities that elevate the heart rate and/or causes increased perspiration, needs to be prepared for potential heat related illness. This includes jobs such cutting timber. As an employee, you are responsible for monitoring your personal factors for heat-related illness including consumption of water or other beverages to ensure hydration.
The information in this program will be used for training supervisors and employees. L & I regulations require that affected employees receive annual training and it must be completed by May 1st. Affected employees hired between May 1 and Sept. 30 must receive training prior to any work assignments. Your supervisor will monitor on-site temperature and clothing requirements to determine if Table 1 applies. The following might be used for temperature readings: thermometer, psychrometer, or hygrometer.
Table 1: Outdoor Temperature Action Levels |
|
All other clothing |
89 degrees |
Double-layer woven clothes including coveralls, jackets and sweatshirts |
77 degrees |
Non-breathing clothes including vapor barriers clothing or PPE such as chemical resistant suits |
52 degrees |
We will adhere to requirements for first aid supplies, first aid training and heat related illness training, Logging operations will have a written emergency medical plan per WAC 296-54 –513- 9 to ensure prompt medical attention, and a stretcher to carry an ill worker to a place accessible to EMS. All work sites will have reliable communication, such as a cell phone, so EMS services (911) can be reached.
We will ensure that a sufficient quantity of drinking water is readily accessible (as much as 2 gallons per person when exposed to temperature at or exceeding the temperature in Table 1) to employees at all times; and that all employees have the opportunity to drink at least one quart of drinking water per hour. If necessary, we will make arrangements to replenish water supply during the day. Your supervisor may send someone to purchase/obtain more drinking water. Your supervisor will tell you where the water is located.
Staying hydrated is extremely important. The body naturally sweats to cool itself. Sweating can use up a significant amount of fluid, which must be replaced continuously throughout the workday. If fluid is not regularly replaced, a worker will become dehydrated, increasing the risk for heat illness.
It is very important that you protect yourself and other workers by learning the signs and symptoms of heat illness and how to treat it.
How do you protect yourself from heat illness?
- Learn the signs and symptoms of heat illness and take them seriously.
- Drink plenty of water or sports drinks, even when not thirsty. Up to 4 cups per hour during the workday.
- Try to do the heaviest work during the cooler parts of the day.
- Adapt the pace of work to the heat – take more breaks, go slower when possible.
- Build up a tolerance to the heat and your work slowly. The more you work in heat, the more your body gets used to it. This is called becoming acclimatized to heat, and can take 4-10 days depending on the person and working conditions.
- Wear light-weight, loose-fitting, light-colored, breathable (e.g. cotton) clothing.
- Take regular breaks in the shade. Generally there will be sufficient rest/break time when “gassing up” your saw or during lunch. However additional breaks will be provided as necessary. For example you may be instructed to sit out several turns to get additional rest/cooling. PPE, like leg protection, should be removed during rest breaks.
- Avoid alcohol, caffeinated drinks (coffee/pop) and heavy meals before or during work.
- Keep an eye on co-workers for symptoms of heat stress and notify a supervisor immediately.
- If you start feeling ill, stop what you are doing immediately and take steps to cool down. Immediately tell your supervisor.
The three major forms of heat stress are heat cramps, heat exhaustion and heat stroke. Heat exhaustion is a serious problem, and heat stroke can kill you.
Heat-related illness |
Signs and Symptoms |
First Aid |
Heat Cramps |
- Muscle cramps or spasms
- Grasping the affected area
- Abnormal body posture |
- Drink water or sports drinks
- Rest, cool down
- Massage affected muscle
- Get medical evaluation if cramps persist |
Heat Exhaustion |
- Heavy sweating
- Pale, cool skin
- Headache
- Weakness
- Dizziness |
- Move to shade or air conditioned vehicle and loosen clothing; do not leave him or her alone
- Spray water or apply cool, wet cloths to head and torso
- Lay on back and elevate legs
- Encourage person to drink cool liquids, preferably a sports drink
- If no improvement, call 911 |
Heat Stroke |
- Any of the above but more severe
- Hot, dry skin (25-50% of cases
- Altered mental status with confusion or agitation
- Can progress to loss of consciousness and seizures.
- Can be fatal |
- Call 911
- Move the victim to a cool shaded area; do not leave him or her alone
- If a shaded area is not available; the blanket with our first aid supplies can be used to block the sunlight.
- Cool the person rapidly using whatever means you can. Fan the person, spray with cool water, or wipe with a wet cloth or cover with a wet sheet, immerse in a tub of cool water.
- Apply icepacks to the person's neck, armpits and in the groin.
- If responsive, lay on back. If unresponsive, place in recovery position (on side).
- If responsive and not nauseous, give sips of water
- Monitor airway and breathing - administer CPR if needed |
Safety Meeting/Training Date: ____________
Employees trained: _________
Appendix 1
First Aid Kits
WAC 296-54-51530
- The employer must provide first-aid kits:
- At each worksite where trees are being cut (e.g., falling, bucking, limbing);
- At each active landing/logging site; and
- In the absence of readily accessible first-aid supplies such as first-aid kits, first-aid stations, first-aid rooms or their equivalent, all transport vehicles, log trucks, speeders, road graders and similar equipment must be equipped with not less than a ten package first-aid kit; and
- The number of first-aid kits and the content of each kit must reflect the degree of isolation, the number of employees, and the hazards reasonably anticipated at the worksite.
- Following is the minimally acceptable number and type of required first-aid supplies to meet the requirements of subsection (1)(a) and (b) of this section.
- Gauze pads (at least 4 x 4 inches).
- Two large gauze pads (at least 8 x 10 inches).
- Box adhesive bandages (band-aids).
- One package gauze roller bandage at least 2 inches wide.
- Two triangular bandages.
- Wound cleaning agent such as sealed moistened towelettes.
- Scissors.
- At least one blanket.
- Tweezers.
- Adhesive tape.
- Latex gloves.
- Resuscitation equipment such as resuscitation bag, airway, or pocket mask.
- Two elastic wraps.
- Splint.
- Stretcher.
- Transport vehicles, log trucks, speeders and road graders must have at least the following number and type of first-aid supplies:
- 10 package kit. 1 pkg. adhesive bandages, 1” (16 per pkg.).
- 1 pkg. bandage compress, 4” (1 per pkg.).
- 1 pkg. scissors and tweezers (1 each per pkg.).
- 1 pkg. triangular bandage, 40” (1 per pkg.).
- 1 pkg. antiseptic soap or pads (3 per pkg.).
- 5 pkgs. employer's choice.
Appendix 2
Emergency Medical Plan
WAC 296-54-513 (9) Each worksite must have an emergency medical plan to ensure rapid emergency care for employees with major illnesses and injuries
Employer ________
Office ____________
Phone Number ____________
Job Site Cell Phone Number(s) ______________
Is there cell phone service at the job site: Yes __ No__
If no, provide directions to the nearest location for cell service: _______________
Job Site Location
____________________________
Latitude Longitude Township Range
____________________________
Section 1/4 Section
Directions to site _______________
Property ownership _____________
County _______________
Emergency Medical Services
Ambulance Phone Number: 911 or
Helicopter Phone Number: 911 or
Working behind locked gate(s)? No __ Yes __
If yes, describe procedure for emergency vehicle
access _____________
Appendix 3
Safety Meeting Record
A safety meeting must be held each time you move to a new jobsite and monthly after the initial jobsite meeting.
Company ________________
Date ___________
Location/Jobsite ________________
Is this the first safety meeting at a new jobsite? Yes __ No __
If yes, list and discuss any site-specific hazards (i.e. danger trees, steep slopes, small landing(s), poor deflection, etc.) _________________
Topic(s) Discussed ______________
Employees Present _______________
Meeting Conducted By ____________
Topics for Discussion
Slips and falls
Working on steep slopes
Proper distance between work areas
Proper communication
Emergency Medical Plan
First aid techniques and equipment
Accidents and near-misses
Personal protective equipment
Unsafe conditions or unsafe acts
Seat belts
Snags/Danger trees
Proper lifting and pulling technique
Driving safety
Proper undercut, backcut and hinge
Saw and chain maintenance
Domino falling
Bucking hazards
Hung-up trees
Barricades/Flaggers
Escape path
Kickback
Appendix 4
Cutting - Monthly Safety Inspection Checklist
Name of the person conducting the inspection: |
Jobsite Location: |
Date: |
Cutter name(s):
1. ____________________ |
2. |
3. ____________________ |
4. |
Inspection (✓) |
Yes |
No |
Comments (If no, list cutter's number and corrective action required) |
Jobsite first aid supplies (first aid kit, stretcher, blanket, splint) |
|
|
|
Written jobsite Emergency Medical Plan |
|
|
|
Start-up and monthly safety meetings documented |
|
|
|
Valid first aid card |
|
|
|
Hard hat (hi-vis & no damage) |
|
|
|
Caulk boots (sharp caulks, provides ankle support and in good condition) |
|
|
|
Eye protection (screen, safety glasses or goggles) |
|
|
|
Hearing protection (muffs or earplugs) |
|
|
|
Gloves |
|
|
|
Whistle (carried on the person and works) |
|
|
|
Two-way radio (carried on the person and works) |
|
|
|
Man check. Visual or audible/radio contact at least every 30 minutes |
|
|
|
Must be at least 3 cutters working at the site to facilitate emergency response (less than 3 would be acceptable if arrangements have been made with another onsite company and radio communication is monitored constantly or each cutter carries a cell phone and they have the capability to call for assistance without leaving the injured or ill cutter) |
|
|
|
Cutter’s first aid supplies in near proximity (2 trauma bandages or equivalent) |
|
|
|
Leg protection (covers to the top of the boot & no damage to the cut protection material |
|
|
|
Road blocked or flagger(s) used if tree(s) can reach the road |
|
|
|
Wedges in near proximity (minimum of 2 wedges & in good condition) |
|
|
|
Axe in near proximity (sharp, handle tight and in good condition) |
|
|
|
Saw gas in approved container |
|
|
|
Saw chain brake and trigger lock working properly |
|
|
|
Saw chain is sharp and properly tensioned |
|
|
|
Saw is in good condition |
|
|
|
During operation, saw is gripped with the cutter's thumb under the handlebar |
|
|
|
At least 2 tree lengths between work areas |
|
|
|
Area around the tree is assessed for hazards (danger trees, widowmakers, loose objects) |
|
|
|
Work area around the tree is brushed out |
|
|
|
Escape path is established that will allow the cutter to move at least 10 feet from the stump |
|
|
|
Tree is assessed for lean, overhead hazards & defects |
|
|
|
Proper undercut is completed (cuts meet/no kerf dutchman, horizontal cut is level, depth of ¼ to about 1/3 the tree diameter, cleaned out, face opening at least 1/5 the tree diameter) |
|
|
|
Undercut is used on trees over 6 inches DBH |
|
|
|
Backcut is placed above the horizontal face cut |
|
|
|
Hinge. Corners are maintained, adequate width across the stump |
|
|
|
Escape path is used once the tree is committed to fall. Cutter should move at least 10 feet from the stump and look up and watch for falling limbs, tops, etc. |
|
|
|
Domino falling is avoided (setting up multiple trees) |
|
|
|
Demonstrates directional control (uses proper wedging technique & hinge width) |
|
|
|
Avoids unnecessary brushing of timber |
|
|
|
Follows proper procedures for pushing a tree that is limb tied or to overcome another falling difficulty (brush out around both trees, establish an escape path from the pusher tree, cut-up the first tree and drive in a wedge(s), while cutting the “pusher tree”, don’t turn your back on the cut-up tree) |
|
|
|
Danger trees felled progressively with standing timber |
|
|
|
Danger trees felled in the direction of lean and into open areas whenever possible |
|
|
|
Lay of the tree is sized up before limbing/bucking (looks for bind, pivot points and potential log movement) |
|
|
|
Establishes an escape path before starting a bucking cut |
|
|
|
Limbs cut flush to log |
|
|
|
Additional comments:
Signature of person completing the inspection: ____________
Appendix 5
Accident/Near Miss Report Form
Employee name _____________________
Date and time of incident ______________
Task being performed at time of incident
__________________________________
Incident reported to __________________
Date & time incident reported __________
Describe what part of the body was injured and injuries in detail
__________________________________
Name(s) of witness(es) _______________
__________________________________
Describe, step by step the events that led up to the incident and how the incident occurred:
__________________________________
Could anything be done to prevent accidents of this type? If so, what?
__________________________________
_____________________________
Signature of employee
Date: _____________
Appendix 6
Incident Investigation Report
Instructions: Complete this form as soon as possible after an incident that results in serious injury or illness.
(Optional: Use to investigate a minor injury or near miss that could have resulted in a serious injury or illness.)
This is a report of a:
__ Death
__ Lost Time
__ Dr. Visit Only
__ First Aid Only
__ Near Miss
Date of incident: ______________
This report is made by:
__ Employee
__ Supervisor
Step 1: Injured employee (complete this part for each injured employee) |
Name: |
Age: |
Job title at time of incident: |
Months with this employer:
______ |
Months doing this job:
______ |
Nature of injury: (most serious one)
- Abrasion, scrapes
- Amputation
- Broken bone
- Bruise
- Burn (heat)
- Concussion (to the head)
- Crushing Injury
- Cut, laceration, puncture
- Illness
- Sprain, strain
- Other
|
Step 2: Describe the incident |
Exact location of the incident: |
Exact time: |
Names of witnesses (if any): |
What personal protective equipment was being used (if any)? |
Describe, step-by-step the events that led up to the injury. Include names of any machines, parts, objects, tools, materials, and other important details. |
Description continued on attached sheets: __ |
Step 3: Why did the incident happen? |
Unsafe workplace conditions: (Check all that apply)
- Inadequate guard
- Unguarded hazard
- Safety device is defective
- Tool or equipment defective
- Lack of needed personal protective equipment
- Lack of appropriate equipment / tools
- Unsafe rigging
- No training or insufficient training
- Other:
|
Unsafe acts by people: (Check all that apply)
- Operating without permission
- Operating at unsafe speed
- Servicing equipment that has power to it.
- Making a safety device inoperative
- Using defective equipment
- Using equipment in an unapproved way
- Unsafe lifting by hand
- Not “in the clear”
- Distraction, teasing, horseplay
- Failure to wear personal protective equipment
- Failure to use the available equipment / tools
- Other: _
|
Why did the unsafe conditions exist? |
Why did the unsafe acts occur? |
Were the unsafe acts or conditions reported prior to the incident? |
Yes __ No __ |
Have there been similar incidents or near misses prior to this one |
Yes __ No __ |
Step 4: How can future incidents be prevented? |
What changes do you suggest to prevent this incident/near miss from happening again? |
__Stop this activity __Guard the hazard __Train the employee(s)
__Train the supervisor(s) __Redesign task steps __Write a new policy/rule
__Enforce existing policy __Routinely inspect for the hazard __Personal Protective Equipment
__Other: ___________________ |
What should be (or has been) done to carry out the suggestion(s) checked above?
______________________________
Description continued on attached sheets: __ |
Step 5: Who completed and reviewed this form? (Please Print) |
|
Written by: |
Title: __________________
Date: _________ |
Names of investigation team members: |
Reviewed by: |
Title: __________________
Date: _________ |
Appendix 7
Logger Safety Program
Cutter Safety Audit Form
This form to be used by:
- trainers to evaluate whether a cutter has successfully completed training and as a certificate of training if the cutter passes the audit; and by
- third party auditors to evaluate if a cutter has been properly trained and follows safe work practices.
Cutter’s name:
Date:
Cutter’s address & phone number:
Trainer/Auditor name (circle the one that applies)
Trainer/Auditor phone number:
Note: In each of the sub-sections below, there is a space for “Comments”. Use the “comments” space to list your reasons for marking “unacceptable” or to provide positive feedback if the cutter “meets acceptable standards.”
1. First Aid & Emergency Procedures and Equipment |
First aid training |
__ Meets acceptable standards
- Cutter has a valid/current certificate of first aid training
__ Unacceptable
__Comments:
|
First aid supplies |
__ Meets acceptable standards
- First aid supplies are appropriate per WAC 296-54-51530
__ Unacceptable
__ Comments_ |
Personal first aid kit
(bleeder kit) |
__ Meets acceptable standards
- Must contain at least two trauma bandages or equivalent absorbent gauze material and a means to secure the material in place.
- Must be clean and dry.
- Must be in near proximity at all times.
__ Unacceptable
__ Comments: |
Whistle for signaling an emergency |
__ Meets acceptable standards
- Must carry a whistle on the person.
__ Unacceptable
__ Comments: |
Man check and responding to an emergency |
__ Meets acceptable standards
- Must be at least three cutters at the site unless arrangements have been made with an onsite logging company to provide emergency assistance or there are two cutters at the site and they both carry cell phones and have the capability of calling for assistance without leaving the injured or ill cutter.
- Cutter must have visual, audible or radio contact with another employee at least every 30 minutes
__ Unacceptable
__ Comments: |
Two-way radios |
__ Meets acceptable standards
- Each cutter must carry an operable two-way radio on their person.
__ Unacceptable
__ Comments: |
Cutter requirements for first aid, emergency procedures and equipment
__ Pass
__ Pass with the following recommendations for improvement:
__ Fail for the following reasons: |
2. Personal Protective Equipment Hardhat |
Hardhat |
__ Meets acceptable standards
- Must meet the requirements of ANSI Z89.1-1986, “American National Standard for Personnel Protection-- Protective Headwear for Industrial Workers-- Requirements.”
- No cracks, deep scratches, large dents or other significant damage, suspension in good condition, plastic hard hat isn't brittle.
- High visibility color
__ Unacceptable
__Comments:
|
Eye/Face protection |
__ Meets acceptable standards
- Maintained in good condition
- Cutter may use eye or face protection including safety glasses/goggles, goggle with mesh screens, or mesh screens/shields attached to the hardhat
__ Unacceptable
__ Comments_ |
Hearing protection |
__ Meets acceptable standards
- Earplugs or earmuffs worn/inserted properly and in good condition
__ Unacceptable
__ Comments: |
Leg protection
“Chaps” or inserts worn underneath the pants are acceptable |
__ Meets acceptable standards
- Must be constructed of cut-resistant material.
- The leg protection must cover the full length of the thigh to the top of the boot on each leg to protect against contact with a moving chain saw.
- The cut-resistant material must not be damaged.
__ Unacceptable
__ Comments: |
Foot protection |
__ Meets acceptable standards
- Must be in good condition
- Boots must have sharp calks, must not have more than 3 missing calks, must cover and support the ankle, and must be cut resistant.
- Leather logging boots, insulated rubber pacs, and rubber boots with cut protection will meet the cut-resistant requirement.
__ Unacceptable
__ Comments: |
Cutter requirements for personal protective equipment
__ Pass
__ Pass with the following recommendations for improvement:
__ Fail for the following reasons: |
3. Evaluation of cutting practices from the previous day
When available and safe, look at 10 stumps. 8 of 10 stumps (or 80% of the stumps looked at) must meet acceptable standards to pass this section of the audit. |
Work area |
__ Meets acceptable standards
- Work area was brushed out
- Proper and clear escape path was available to allow cutter to move at least 10 feet away from the stump
__ Unacceptable
__Comments: |
Undercuts |
__ Meets acceptable standards
- Proper depth
- Level
- Proper width
- Cuts meet
__ Unacceptable
__ Comments_ |
Backcuts |
__ Meets acceptable standards
- Level
- Placed above the horizontal face cut
- Adequate hinge across the stump
__ Unacceptable
__ Comments: |
Evaluation of cutting practices from the previous day
__ Pass
__ Pass with the following recommendations for improvement:
__ Fail for the following reasons: |
4. Chain saw and hand tools Chain saw |
Chain saw |
__ Meets acceptable standards
- Full wrap handlebars and adequate falling dogs, functioning chain brake and throttle lockout.
- Chainsaw and bar length compatible with average timber size.
- Chainsaw in good operating condition, and all safety features functioning and idle properly adjusted.
- Spare bar and chain readily available.
__ Unacceptable
__Comments: |
Chain saw filing and chain tension |
__ Meets acceptable standards
- Chain is sharp, properly filed/grinded and tensioned
__ Unacceptable
__ Comments_ |
Axe or suitable tool for driving wedges |
__ Meets acceptable standards
- Handle is secure and in good condition.
- Must carry or have in near proximity of the tree being fell.
__ Unacceptable
__ Comments: |
Wedges |
__ Meets acceptable standards
- Minimum of 2 wedges.
- Must carry or have in near proximity of the tree being fell.
- Appropriate size for the timber type
__ Unacceptable
__ Comments: |
Chain saw and hand tools
__ Pass
__ Pass with the following recommendations for improvement:
__ Fail for the following reasons: |
5. Chainsaw operation |
Starting the saw |
__ Meets acceptable standards
- Saw is started with the chain brake engaged or where firmly supported. Drop starting is prohibited. Note: Resting the bar on a log/stump while starting is considered “firmly supported.”
__ Unacceptable
__Comments: |
Grip |
__ Meets acceptable standards
- The chain saw is held with the thumbs and fingers of both hands encircling the handles during operation.
- One hand operation is used only when two handed operation creates a greater hazard.
__ Unacceptable
__ Comments_ |
Firm footing & balance |
__ Meets acceptable standards
- The chain saw is not used in a position or at a distance that could cause the operator to become off-balance, to have unsteady footing, or to relinquish a firm grip on the saw
__ Unacceptable
__ Comments: |
Carrying the saw |
__ Meets acceptable standards
- The saw is carried in a manner that will prevent operator contact with the cutting chain.
- The chain saw is shut down or the chain brake engaged whenever a saw is carried further than 50 feet or whenever terrain, brush and slippery surfaces create a hazard. Exception: When the cutter is carrying the chain saw on his shoulder, the chain saw must be shut down but the chain brake doesn’t have to be engaged.
__ Unacceptable
__ Comments: |
Chainsaw operation
__ Pass
__ Pass with the following recommendations for improvement:
__ Fail for the following reasons: |
6. Arrangement of work area and planning |
Distance between work areas |
__ Meets acceptable standards
- Trees can't fall into an adjacent accupied work area.
- The distance between work areas is at least two tree lengths of the trees being fell.
- A distance of more than two tree lengths is maintained between work areas on any slope where rolling or sliding of trees or logs is reasonably foreseeable.
- Trees must not be fell if the falling tree can strike any yarder line and endanger workers.
__ Unacceptable
__Comments: |
Work location |
__ Meets acceptable standards
- Where felled trees are likely to roll and endanger workers, cutting must proceed from the bottom toward the top of the slope, and uphill from previously fell timber.
- A cutter must not be placed on a hillside immediately below another cutter or below other logging operations where there is probable danger.
__ Unacceptable
__ Comments_
|
Traffic control on roads |
__ Meets acceptable standards
- When applicable, flaggers are used or the road is blocked
__ Unacceptable
__ Comments: |
Arrangement of work area and planning
__ Pass
__ Pass with the following recommendations for improvement:
__ Fail for the following reasons: |
7. Falling the tree - preparation (must observe 10 trees) |
Prepare to Fall the Tree
Acceptable procedure:
__ Tree assessed from top to bottom for defects or hazards
__ Tree lean assessed from high side
__ Escape path brushed out to allow cutter to move at least 10 feet away from the stump
__ Windfalls, logs or other debris that could be thrown by the falling tree is cut away
__ Danger trees/Snags felled progressively with other trees and as soon as an opening is available.
__ Work area around the base of the tree is brushed out.
__ Tree felled to the open whenever conditions permit (avoids brushing standing timber).
__ Axe and wedges are in near proximity.
__ Saw has an adequate amount of gas.
|
__ Meets acceptable standards
__ Unacceptable
__Comments: |
Falling the tree- preparation
__ Pass
__ Pass with the following recommendations for improvement:
__ Fail for the following reasons: |
8. Falling the tree (must observe 10 trees) |
Falling procedure
Acceptable procedure:
__ Good tree assessment from high side
__ While felling a tree, avoid cutting from under the lean.
__ The undercut must not be made while other workers are in an area into which the tree could fall
__ Should use sight lines to construct undercut with saw dogged in
__ Undercut is large enough to safely guide trees and eliminate the possibility of splitting. Undercuts must be used on all trees over 6 inches DBH.
__ A tree with no perceptible lean, having an undercut depth of one-fourth of the diameter of the tree and a face opening equal to one-fifth of the diameter of the tree would meet the requirement.
__ Checks & cleans out undercut
__ Backcut is level and sawn in above the horizontal face cut.
__ Backcut leaves enough hinge wood to hold the tree to the stump during most of its fall so that the hinge is able to guide the tree's fall in the intended direction
__ Holding wood is maintained across the entire stump (swing cuts can only be used by an experienced person)
__ Safe work practices followed to ensure corner is not cut- off
__ Wedge(s) is set and then driven in if there is a possibility of tree setting back
__ When tree is committed to the fall, cutter uses his escape path and moves a safe
distance away from stump. Note: A cutter should move at least 10 feet from the stump, but there may be an occasional exception. For example, a cutter needs to stand on a ledge to fall a tree and the terrain prevents the cutter from moving 10 feet away. Note: In some situations, the cutter may have to briefly remain at the stump after the tree is committed to fall in order to complete the backcut.
__ Waits for canopy to settle down before returning to the stump or next tree
__ When felling a small diameter tree against the lean, the following procedure can be followed:
- backcut may need to be sawn first
- wedge(s) is set
- undercut is sawn while leaving adequate hinge wood
- tree is wedged over
__ When felling a short stubby tree
- The undercut should be large and deep (up to 50% of the diameter)
__ On slopes over 50% grade, tree(s) must at least be quartered to a degree that prevents employees from being exposed to the possibility of sliding or rolling trees or logs.
__ Avoids domino falling
- Domino falling of trees, including danger trees, is prohibited. Domino falling doesn’t include the falling of a single danger tree by falling another single tree into it to overcome a falling difficulty such as limb tied trees or when a tree sets back and the cutter isn’t able to start a wedge.
__ Trees with face cuts and/or backcuts must not be left standing unless all the following conditions are met:
- The cutter clearly marks the tree;
- Discontinues work in the hazardous area;
- Notifies all workers who might be endangered; and
- Takes appropriate measures to ensure that the tree is safely fell before other work is undertaken in the hazardous area.
|
__ Meets acceptable standards
__ Unacceptable
__Comments:
|
Falling the tree
__ Pass
__ Pass with the following recommendations for improvement:
__ Fail for the following reasons: |
9. Bucking (must observe at least 10 bucking cuts) |
Bucking |
|
Safe work procedures |
|
Note: If trees aren't being bucked, ask cutter to identify safe work practices. Cutter must identify at least six (6) of the following SWPs to meet acceptable standards.
__ Checks surrounding area for potential chain reactions such as sliding and rolling logs
__ Rechecks canopy
__
Assess tree stability before stepping onto the tree
__
Checks for obstacles that could cause the tree to pivot, roll or move
__ Determines high side and direction of gravity pull
__ Identify the binds
__ Bucked log lengths at or near the pivot points
__
Determine and brushed out a safe bucking position on the high side
__
Ensured stable footing
__
Logs must be completely bucked through whenever possible. If it becomes hazardous to complete a cut, then the log must be marked and identified by a predetermined method.
__
Escape path established and used. Cutter should never have his back up against a solid object, such as a root wad, large blowdown, or rock bluff, that would block his escape path.
|
__ Meets acceptable standards
- Includes faller assesses the area for overhead hazards, assesses the tree for bind and stability, ensures there are no loose objects above or behind
__ Unacceptable
__Comments:
|
Bucking
__ Pass
__ Pass with the following recommendations for improvement:
__ Fail for the following reasons: |
10. Heavy Leaner - falling |
Questions if situation not available
Ask: What are the hazards?
- Stump pull
- Barber chair
- Pinched saw (must correctly list 2 of the 3 hazards to meet acceptable standards)
Ask: What falling cuts would you use to prevent the hazards?
- As large an undercut as the tree will allow, up to but not more than ¼ tree diameter
- Side notching
- Could also bore just behind holding wood to reduce pressure before finishing backcut
(must correctly list 2 of the 3 procedures to meet acceptable standards)
|
__ Meets acceptable standards
- Includes assessing tree as a heavy leaner.
- Undercut no more than ¼ tree diameter.
- Adequate precautions taken to prevent barber-chairing (may include side notching or boring the backcut).
- Cutter watches for stump pull.
- Tree felled with lean.
__ Meets acceptable standards
- Correctly listed hazards and safe work procedures
__ Unacceptable
__Comments: |
Heavy leaner - falling
__ Pass
__ Pass with the following recommendations for improvement:
__ Fail for the following reasons: |
Overall audit result |
__ Pass
__ Pass with with a required corrective action plan for improvement. (See attached corrective action plan)
__ Fail (See attached explanation for failing the audit and corrective actions that need to be taken to pass.) |
Signature of trainer or auditor:
_______________________
Signature of trainee/cutter:
_______________________
Appendix 8
Daily Training Log for New Cutter Training
Cutter’s name:
Trainer’s name(s):
Day |
Date of basic training |
Curriculum topic(s) that were covered
(enter topic numbers) |
Comments on performance
of the new cutter |
Cutter's signature |
Trainer's signature |
1 |
|
Topics 1 & 2 must be covered on day 1 |
|
|
|
2 |
|
|
|
|
|
3 |
|
|
|
|
|
4 |
|
|
|
|
|
5 |
|
|
|
|
|
6 |
|
|
|
|
|
- Required personal protective equipment
- Safe chain saw use
- General work procedures
- Falling- Planning
- The undercut
- The backcut
- Unintentional "Dutchman"
- Intentional "Dutchman" (swingcut)
- Falling danger trees
|
- Common falling difficulties
- Leaners
- Heavy leaners
- Extreme leaners and leaners with splits in the butt
- Falling against the lean
- Falling against the lean - Using a hydraulic jack
- Trees tied together
- Hang-ups
|
- Windfalls and windfall roots
- Burned timber
- Bucking
- Bind
- Pivot points
- Limbing
- Boring
- Cut-up trees
- Domino falling
|
Weekly Evaluation Training Log for New Cutter Training
Cutter's name: _____________________________________
Trainer's name(s): __________________________________
Week |
Date of
evaluation |
Curriculum topic(s)
that were reinforced
(enter topic numbers) |
Comments on cutters
performance
If ther cutter is
"not meeting
requirements,"
an action
plan for improvement
must be developed
(see back of page) |
Cutter's
signature |
Trainer's
signature |
1 |
|
|
__ Meeting
requirements
__ Not meeting
requirements |
|
|
2 |
|
|
__ Meeting
requirements
__ Not meeting
requirements |
|
|
3 |
|
|
__ Meeting
requirements
__ Not meeting
requirements |
|
|
4 |
|
|
__ Meeting
requirements
__ Not meeting
requirements |
|
|
5 |
|
|
__ Meeting
requirements
__ Not meeting
requirements |
|
|
6 |
|
|
__ Meeting
requirements
__ Not meeting
requirements |
|
|
- Required personal protective equipment
- Safe chain saw use
- General work procedures
- Falling- Planning
- The undercut
- The backcut
- Unintentional "Dutchman"
- Intentional "Dutchman" (swingcut)
- Falling danger trees
|
- Common falling difficulties
- Leaners
- Heavy leaners
- Extreme leaners and leaners with splits in the butt
- Falling against the lean
- Falling against the lean - Using a hydraulic jack
- Trees tied together
- Hang-ups
|
- Windfalls and windfall roots
- Burned timber
- Bucking
- Bind
- Pivot points
- Limbing
- Boring
- Cut-up trees
- Domino falling
|
Week |
Action plan for improvement |
Cutter's initials |
Trainer's initials |
1 |
|
|
|
2 |
|
|
|
3 |
|
|
|
4 |
|
|
|
5 |
|
|
|
Publication #: 7/2014
Disclaimer and Reproduction Information: Information in
NASD does not represent NIOSH policy. Information included in
NASD appears by permission of the author and/or copyright holder.
More