There are approximately 125 Washington State apple-packing companies (Teamsters 1997).
Three Yakima valley fruit packing companies (Standard Industrial Classification 0723)
participated in this pilot study characterizing the musculoskeletal hazards in the apple
packing industry and worker self-reported work-related discomfort. For privacy purposes,
the companies will be referred to as Company 1, 2, and 3. Data collection took place on
April 20, April 29, and May 4, 1999 at companies 1, 2, and 3, respectively. The
participating companies varied by size and the type of packing process used (Table 1).
Companies 1 and 2 were similar in size but differed in the type of packing processes used,
Company 2 used manual packing only. All companies housed packing operations in
concrete tilt-up warehouses with concrete floors. The buildings were generally unheated,
although area heating was provided in some parts of the warehouse. Workers were provided
with lunchroom/break rooms.
Evaluations were conducted at each company during the first shift of the day (Company 3 was the only company operating 2 shifts). On the days of evaluation, Company 1 had 73 full time equivalent (FTE) workers and Company 2 had 52 FTE. Company 3 had 90 FTE per shift, or 180 production workers total. Based on the information collected on the days of sampling, an estimated daily production rate for each company was calculated by dividing the number of standard sized boxes packed on first shift by the number of FTE employees working on first shift (Table 2). The information regarding FTE and packed boxes varies daily; consequently, the production rate determined for the days of our evaluations may not reflect usual production or staffing levels.
Company 3 was the most automated of the three participating companies. Company 2 paid packers piece rate pay while Companies 1 and 3 paid straight salary. Workers at all companies had two 15-minute breaks and a 30 minute lunch period during an 8 hour work shift. None of the participating companies were unionized. Management at all three companies identified back injuries and upper extremity musculoskeletal disorders as occupational health concerns.
Table 2 Participating Company Overview
Co. |
Fruit |
FTE/
Shift |
Company Reported Injuries |
Packing Process |
Pay Type |
# Boxes Packed During Shift* |
Daily Production Rate**** (Boxes/FTE) |
1 |
Apples and Pears |
73 |
Slips/Falls
Back and
Wrist/Hand
Injuries |
Manual Tub Pack
Semi-auto Tray
Semi-auto Bag
(stand) |
Hourly Rate |
2,678** |
48 |
2 |
Apples and Pears |
52 |
Slips/Falls
Back and
Repetitive
Motion
Injuries |
Manual Tub and
Conveyor Pack |
Piece Rate |
3,733 |
72 |
3 |
Apples |
90 |
Back and
Wrist/Hand
Shoulder
Injuries |
Semi-auto Tray
Semi-auto Bag (sit) |
Hourly Rate |
4,609*** |
58 |
* Based on the number of standard boxes packed during observed 8-hour shift
** In addition 1,154 Costco boxes, 105 Wal-Mart bins, and 25 grocery store bins were packed
*** In addition 2,446 Costco boxes were packed
**** Production rate is calculated by dividing the number of standard boxes packed by the first shift FTE, assuming 1 tote = 16 standard boxes; 1 Wal-Mart bin = 1 standard box; 1 Costco box = 0.25 standard box.
4.1.1 Company 1
On the day of our evaluation 73 workers were present at the work site. Thirty-nine workers met the selection criteria for the study, and 95 percent of these volunteered to participate in the study. The company engaged in both manual and automatic packing. Workers packed in a standing position and primarily packed into three and five pound bags. A total of 8,352 three-pound bags and 13,665 five-pound bags were filled on the day of the site assessment. A total of 1,108 tray pack boxes; 1,570 bag boxes; 1,154 Costco boxes; and 130 other units (105 Wal-Mart bins and 25 grocery store bins) were filled. Agritech, Inc., manufactured the conveyor and packing line equipment.
4.1.2 Company 2
On the day of our evaluation 52 workers were present at this work site. Thirty-three workers met the selection criteria, and 91 percent of these volunteered to participate in the study. The company engaged in manual packing processes; workers were packing apples from tubs into trays and bags by hand. During the day of the site assessment, 3,505 standard sized boxes with trays and 228 boxes with bags were packed. Van Doren Sales, Inc manufactured the conveyor and packing line equipment. Workers were paid by piece rate at this company.
4.1.3 Company 3
On the day of our evaluation, 90 first-shift workers were present at the work site. Seventy three workers at the company met the job title selection criteria. From the 73 eligible workers, 40 were selected randomly from workers in the job titles included in the study criteria. Thirty-two workers agreed to participate in the study (1 declined and 7 were found to be assigned at non-criteria jobs on the day of the study). Company 3 used an automatic packing process, primarily tray packing. During the first shift, 4,311 standard sized boxes with trays (3,608 boxes TP and 703 HP) and 2,446 one-layer Costco boxes were packed. Also 298 bag boxes (221 boxes of 3-pound bags and 77 boxes of 5-pound bags) were packed. The semi-automatic bagging was conducted at sitting stations. Van Doren Sales, Inc., manufactured the conveyor and packing line equipment. The company was in the process of installing several new packing lines, but these lines were not in operation at the time of this study.
A total of 105 workers across all three companies agreed to participate in the study. Twenty of the participants were working in the job title of sorter, 67 were working as packers, and 13 were working as segregators. Five workers from Company 3 were not engaged in sorting, packing, or segregating on the day of the evaluation and were excluded from further analysis. The number of sorters participating in the study ranged from five to nine per packing house, while the number of packers and segregators ranged from 22 to 23 and three to five respectively (Table 3). The sorters' mean age for Company 1 (57 years old) was considerably higher than the other two companies. The mean age of packers was high (45 years old) at Company 2. The female/male ratio of participants was similar in all companies, but the proportion of Hispanic workers who participated from each company varied between 22 and 100 percent. Most packers and sorters were female, while nearly all segregators were male. Subjects had been employed in the industry for seven to 18 years on average, although segregators tended to be more recently in the industry. Fifteen workers (15 percent) reported working second jobs during the packing season. Other jobs included orchard work (seven), other fruit/vegetable packing (two), and custodian (two). Outside activities, such as sports, crafts, and other hobbies, that might have musculoskeletal hazards were reported by 64 percent of workers, with an average duration of 5 hours per week. Ninety-eight percent of the workers were right handed.
Table 3 Study Participants
Company |
Job Title |
N |
Mean Age (Range) |
Percent Female |
Percent Hispanic |
Years at Packing Houses Mean (SD) |
Second Job* # (%) |
Other** Activities # (%) |
1 |
Sorter |
9 |
57 (43-69) |
100 |
0 |
12.1 (12.1) |
0 (0%) |
7 (78) |
|
Packer |
23 |
37 (19-67) |
78 |
22 |
6.3 (5.8) |
2 (9%) |
17 (74) |
|
Segregator |
5 |
28 (19-48) |
20 |
60 |
4.7 (3.6) |
1 (20%) |
4 (80) |
Total-1 |
|
37 |
40 (19-69) |
76 |
22 |
7.6 (7.9) |
3 (8%) |
28 (76) |
2 |
Sorter |
6 |
48 (28-62) |
100 |
67 |
14.0 (10.1) |
1 (17%) |
3 (50) |
|
Packer |
22 |
45 (22-75) |
100 |
55 |
20.5 (15.7) |
4 (18%) |
14 (64) |
|
Segregator |
3 |
28 (25-32) |
0 |
100 |
2.5 (2.3) |
0 |
3 (100) |
Total-2 |
|
31 |
44 (22-75) |
90 |
61 |
17.5 (14.9) |
5 (16%) |
20 (65) |
3 |
Sorter |
5 |
45 (27-57) |
80 |
100 |
5.4 (5.7) |
1 (20%) |
3 (60) |
|
Packer |
22 |
38 (18-66) |
91 |
100 |
8.4 (3.9) |
2 (9%) |
9 (41) |
|
Segregator |
5 |
26 (23-31) |
0 |
100 |
0.3 (0.2) |
4 (80%) |
5 (100) |
Total- 3 |
|
32 |
37 (18-66) |
75 |
100 |
6.9 (5.1) |
7 (22%) |
16 (50) |
|
|
|
|
|
|
|
|
|
TOTAL |
|
100 |
40 (18-75) |
80 |
59 |
10.3 (10.8) |
15 (15%) |
64 (64) |
* second job held during packing season; does not include those working elsewhere during non-packing season.
** Other activities include ball sports, auto repair, gardening, fishing, wood shop, shooting, knit/sew/crochet, craft work, walking, running, bowling, biking, musical instrument.
Some of the study survey instruments were designed to assess long-term health effects while others measured activities that occurred the day observations were made. Packing house workers may be assigned to different jobs on different days depending on production needs, resulting in a mixed job title history for many workers. Therefore it was not possible to analyze specific job titles for long-term exposure or outcomes. The findings are organized with long-term and general effects presented first, followed by more detailed findings for specific job titles.
Each participating company provided OSHA 200 incidence logs (described below) for the years 1994-1998. Companies also gave the Field Group permission to contact the Department of Labor and Industries to obtain workers’ compensation rates for their companies for the years of interest. The company-specific rates were obtained in order to compare state-reported workers' compensation rates to company-maintained OSHA 200 rates as well as to the fruit and vegetable packing risk class workers' compensation rate. Apple packing houses are categorized in the fruit and vegetable packing risk class; consequently, the industry-wide rate may not be an accurate reflection of the workers' compensation experience of apple packing houses alone.
The OSHA 200 log is an injury reporting form completed by each company annually to meet state and federal record-keeping requirements. All “recordable” injuries must be listed on the form. An injury is considered recordable if it is work-related; is a fatality, or a work related illness; results in loss of consciousness, restriction of work, transfer to another job, or lost workdays; or requires medical treatment beyond first aid. The OSHA 200 annual work-related injury incidence rate is calculated by dividing the total number of reported injuries by the total hours worked by all company employees during the reference year (L&I, 1997). The annual state-reported workers' compensation claim rate is based on the number of workers’ compensation claims accepted for payment divided by the total employee hours worked that year.
The industry-wide workers’ compensation rate has been decreasing over the past several years. Companies 1 and 2's state-reported workers’ compensation claims rates have also been decreasing, with Company 1 down from 25.9 in 1994 to 15.5 in l998 and Company 2 having a similar reduction from 20.4 to 7.5 over the same time period (Table 4). Company 3's workers’ compensation rate increased from 9.1 in 1994 to 16.3 in 1998. Change in rates could be influenced not only by the number of injuries occurring, but also by an increased number of new workers (who often have an increased injury rate), by a change in worker awareness, or by an increased willingness to report injuries or initiate a claim. Company 3 experienced a significant increase in both production and process automation during this period. The OSHA 200 rates are similar to the workers' compensation rate for Companies 1 and 2, but Company 3 workers' compensation rates are higher than the OSHA 200 rates.
Table 4 Workers Compensation and OSHA 200 Rates
Year |
Company 1 |
Company 2 |
Company 3 |
Industry Wide WC Rate** |
WC |
OSHA200 |
WC |
OSHA200 |
WC |
OSHA200 |
1994 |
25.9 |
25.9 |
20.4 |
17.9 |
9.1 |
2.0 |
22.2 |
1995 |
28.2 |
29.2 |
12.5 |
7.5 |
9.0 |
3.9 |
19.5 |
1996 |
25.2 |
22.4 |
14.4 |
12.9 |
14.2 |
2.6 |
19.3 |
1997 |
19.5 |
19.5 |
14.6 |
15.9 |
12.2 |
* |
17.9 |
1998 |
15.5 |
19.9 |
7.5 |
7.5 |
16.3 |
3.0 |
16.3 |
WC = state reported workers compensation claims rate
OSHA 200 = company reported recordable injury rate rates are number of injuries per 100 full-time workers
* Incomplete OSHA 200 log
** Includes all fruit and vegetable packing houses statewide
Musculoskeletal Injury Reporting. The companies OSHA 200 logs were further reviewed to identify injuries of a musculoskeletal nature over a five-year period. Only injuries of a strain, sprain, or repetitive character were included in this portion of the analysis. Accidents involving slips, trips, falls, or being struck by or caught in objects were excluded from this analysis. The musculoskeletal injury rate was calculated using the same method discussed above (L&I, 1997). Injuries were most frequently reported to the back, wrist/hand, and shoulder (Table 5). The OSHA 200 data could not be analyzed by job type because of inconsistencies in injury recording within and between companies.
Table 5 OSHA 200 Musculoskeletal Injury Rates by Body Site (1994-1998)
Company |
Total OSHA 200 injuries |
MS Injuries (%) |
MS Injury |
Back Injury |
Wrist/Hand Injury |
Shoulder Injury |
Neck Injury |
Other MS Injury |
1 |
52 |
36 (69) |
16.4 |
6.8 |
5.4 |
0.5 |
0.9 |
2.7 |
2 |
48 |
19 (40) |
5.0 |
1.1 |
0.5 |
1.1 |
0.8 |
1.6 |
3 |
63 |
22 (35) |
0.8 |
0.5 |
0.1 |
0.1 |
0 |
0.1 |
TOTAL |
163 |
77 (47) |
2.2 |
0.9 |
0.5 |
0.2 |
0.1 |
0.5 |
rates are number of musculoskeletal injuries per 100 full-time workers
4.3.2 Subject Interviews
Study subjects were interviewed to obtain information with regard to their work and general health history, self-reported symptoms, and their perception of health and safety risks at work.
4.3.2.1 General Health History
Study subjects were asked about height and weight, whether they had ever had certain disorders diagnosed by a medical doctor, and whether they were currently taking any medication for pain. Ten subjects reported a tendentious diagnosis (two sorters and eight packers) and six reported a carpal tunnel syndrome (CTS) diagnosis (six packers). Most of these disorders were reported by workers from Company 2 (five CTS and six tendentious), with the remaining cases from Company 1. Current use of pain medication was reported for
discomfort related to the back (15), hands (two), wrist (two), neck (five), arms (four), shoulder (four), and headaches (four).
Certain diseases or conditions, including diabetes, thyroid conditions, and high blood pressure, may predispose a person to musculoskeletal disorders (Putz-Anderson, 1988). The percent of study participants who reported these disorders was compared with the prevalence of each disease in the U. S. population. The study population's self-reported rates of high blood pressure, and thyroid conditions were similar to those reported in the United States population (Table 6). Diabetes rates were similar to published rates of various groups of US women (American Heart Association 2001, Resnick 2000, Canaris 2000).
Table 6 Participant Health Conditions Compared to U.S. Population
Condition |
Study Population |
U.S. Population |
Diabetes |
7% |
|
Diabetes (non-Hispanic white females) |
|
5% |
Diabetes (Mexican-American females) |
|
11% |
High Blood Pressure |
19% |
20% |
Thyroid Condition |
10% |
10%* |
Overweight or obesity |
67% |
55% |
* up to 10% of women
Study participants' height and weight were used to calculate a body mass index. Overweight subjects were identified based on body mass index ranges. The study population was classified 67% overweight or obese compared to 55% for the general United States adult population. A modest increase in low back pain risk has been found for high body mass index (Leboeuf-Yde, 1999). There may be a somewhat higher risk of low back pain for this study group compared to the general population because of the greater proportion of overweight subjects.
4.3.2.2 Self-Reported Symptoms
The self-reported symptoms section of the interview questionnaire included questions about problems with the neck, shoulder, back, elbow/forearm, hand/wrist, hip, knee, foot/ankle, and related workers' compensation claims. A problem was defined as more than three occurrences or one occurrence that lasted more than one week within the last year. A work related health problem was reported for at least one body site by 53% of the participants. Subjects indicated that pain or discomfort in the back, shoulder, neck, and hand/wrist were the most frequent and serious problems. More than half of back, hand/wrist, and shoulder injuries were work-related. Most problems were reported to be from chronic rather than acute (sudden) injuries. For example, only 8 of 48 back problems reported were from acute (sudden) injuries. Subjects often reported first noticing their musculoskeletal problems while working at their current job (Table 7).
Table 7 Symptom Reporting by Body Site
Body Site |
N |
# Workers Reporting a Problem |
Problem Work Related |
Problem from Sudden Injury |
Problem First Noticed on Current Job |
Most Problematic Body Site |
Back |
98 |
48 |
26 (54%) |
8 (16%) |
35 (73%) |
25 (52%) |
Shoulder |
98 |
38 |
21 (55%) |
8 (21%) |
35 (92%) |
15 (39%) |
Neck |
99 |
30 |
13 (43%) |
10 (33%) |
19 (63%) |
12 (40%) |
Hand/Wrist |
94 |
38 |
20 (53%) |
9 (24%) |
29 (76%) |
12 (32%) |
Elbow/Forearm |
99 |
30 |
7 (23%) |
6 (20%) |
23 (77%) |
8 (27%) |
Hip |
99 |
22 |
8 (36%) |
10(45%) |
19 (86%) |
4 (18%) |
Knee |
99 |
19 |
8 (42%) |
6 (32%) |
12 (63%) |
5 (26%) |
Foot/Ankle |
99 |
23 |
7 (30%) |
6 (26%) |
15 (65%) |
6 (26%) |
4.3.2.3 Risk Perception
One hundred participants completed the risk perception interview questions. Sixteen percent of the workers stated that they had no concerns about their jobs. The remaining 84% listed 180 different concerns. Of those, one half of the responses referred to specific movements resulting in body pain. Generally, workers were similar in their reporting of work activities that they perceived to be risk factors for upper body discomfort. Some examples of the responses to the open-ended questions about activities that cause musculoskeletal pain included:
"Repetitive motion - going to get joint ache and muscle ache."
"Lifting and turning apples and putting them in the bins hurts my wrists."
"If you pick up a box wrong, you could get hurt."
"When the boxes or the trays are stuck, we have to pull them."
"Your back has a lot of wear and tear from bending."
One quarter of the responses referred to air quality factors, such as chlorine, carbon
monoxide, and other airborne contaminants. Other concerns included wet floors, equipment
safety, noise, temperature, and work pace. Overall, responses to the question "what specific
tasks of your job do you think are hazardous?" were similar across all workers. While most
workers at each company identified musculoskeletal hazards, differences in risk perceptions
between companies may be related to the type of equipment, plant layout, type of salary,
and degree of automation.
The proportion of responses that identified musculoskeletal risks as a hazard was somewhat
lower in Company 1 than in Companies 2 or 3. Air quality hazards were raised more
frequently in Company 1 than at the other two companies. Workers at Company 1 also
identified equipment malfunctions, unprotected sharp edges, and awkward height of
machinery as hazardous.
Company 2 had a different production layout and pay structure. Packers were paid piece rate and many packers said they preferred a faster production pace because they had more control over their income. Packing materials, such as unfolded boxes, trays, and tissues,
were stacked on the ground and on racks above each packer. Concerns about hand and wrist pain were lowest in Company 2, but these workers did cite problems with bending and reaching for materials.
Company 3 was the most automated and both workers and management emphasized “production” as a priority. In addition, all the machinery was quite new. Two thirds of the responses for workers from Company 3 related to body pain. Female packers listed bagging 10 pound bags of apples as hazardous, as well as pushing and pulling stuck boxes and trays out of the machinery.
Worker Actions to Prevent Injuries: Workers were asked to list things that they could do to prevent injuries or exposures at work. One quarter of participants said that there was nothing that they personally could do to prevent an illness or injury at work. One half of these responses came from Company 1. One third of all the recommendations for health and safety improvements were general comments about personal responsibility with regard to safety, such as “be careful” or “watch out”. These comments were probably directed at avoiding acute accidents, rather than chronic musculoskeletal disorders.
Other themes raised by the question, “what can you do to prevent injuries?” included properly handling materials, using good work practices, maintaining clean floors, following company rules regarding restricted areas, informing management of problems, using personal protective equipment, and following the dress codes. One quarter of Company 1 participants suggested that it was important to make time for recovery from the work tasks, such as resting at home to conserve muscles for work. They also indicated a need to be properly trained to do the job, and especially how to lift properly. Workers in Company 3 mentioned the need to maintain a reasonable work pace and not push too hard. Packers from Company 2 and Company 3 mentioned the need to avoid lifting materials from floor level, while Company 3 workers mentioned the need to limit the weight of bags of apples as well as avoid pushing and pulling stuck trays and boxes out of the machinery.
Company Actions to Prevent Injuries: Workers were asked about things that they believe the company could do to prevent exposures or injury at work. Fifteen percent of the participants stated that there was nothing the company could do to make the workplace safer. Non-negative responses to the question were divided between things the companies already were doing to keep workers safe, and things they should do to improve workplace safety. Participants stated that their employers already had rules, safety meetings, and provided personal protective equipment such as gloves. Workers also mentioned that companies warned workers to be careful, posted signs, and conducted training sessions on safe work practices.
Workers made several suggestions to improve the health and safety of the workplace including improving the ventilation, modifying the location of packing materials, and slowing the pace of work. Purchasing new equipment or repairing existing equipment, improving forklift safety, and keeping the warehouse floors clean were also mentioned. A number of workers stated that women should not have to do heavy work such as lifting boxes. Workers also suggested the companies consider reducing the weight of the boxes, ensuring that the distribution of work among workers was fair, increasing the number of workers, and investigating job rotation.
4.3.3 Across Shift Body Discomfort
A body discomfort survey was administered to participants at the beginning and end of the shift on the same day that job observations were conducted. The pre/post shift discomfort map was administered to a total of 16 sorters, 49 packers, and 8 segregators. Each participant was asked to rate their comfort/discomfort on a scale of 1-5 (1= happy face; 5= frowning face) on 12 parts of a body map. Participants were also asked to record the specific job they were assigned to for that day. Work assignments varied somewhat from day to day depending on production requirements, especially for packers who may pack trays one day and bags the next. On the day of sampling at Company 2, some packers packed both bags and trays that day and were designated as “manual packers”.
The pre/post shift discomfort survey was designed to characterize self-reported symptoms that may be related to or exacerbated by that shift’s work activities. Since this tool was designed to measure discomfort for only one shift, the specific job assigned for that shift could be assessed. For example, the different packer types could be differentiated with this survey tool. In contrast, the self-reported symptoms interview addressed symptoms that occurred over time and did not differentiate between specific symptoms that might relate to one specific job.
The mean change in discomfort across the shift for each of the 12 body sites was calculated for each job category (Table 8). A mean change value of +1 across the shift indicates that a worker scored that body site one rank higher (higher = greater discomfort) on average at the end of the shift than the beginning of the shift. Semi-automatic packers had by far the highest across shift discomfort rating with a mean of 1.4 for all body sites, while sorters and manual packers both had a mean change of 0.5. Segregators had very little change from pre- to post-shift (all-body site mean of 0).
Table 8 Self–Reported Across Shift Discomfort
Job Type |
N |
Across Shift Change-All Body Sites Mean (SD) |
Highest Risk Body Sites |
Lower Back |
Upper Back |
Hand/
Wrist |
Neck |
Shoulder |
Elbow |
Sorter |
11 |
0.5 (0.6) |
0.8 |
1.4 |
0.8 |
1.1 |
1.5 |
0.8 |
Manual Packer |
20 |
0.5 (0.6) |
1.0 |
0.9 |
0.6 |
0.6 |
0.6 |
0.4 |
Semi-Automatic Packer |
17 |
1.4 (1.1) |
1.7 |
1.9 |
1.6 |
1.3 |
1.8 |
1.4 |
Segregator |
8 |
0.0 (0.6) |
0.0 |
0.0 |
0.5 |
-0.3 |
-0.1 |
0.3 |
Despite similarities in the overall production processes across all companies, there were substantial differences in specific aspects of some of the work. The work tasks performed by sorters and segregators and their work station configurations were similar at all three companies. However, differences were found in packing tasks, equipment, and work station layouts across the companies. Because of these differences in packer tasks, the job title “packer” was subdivided into manual vs. semi-automatic and by the type of container (bags or trays).
4.4.1 Sorting
The number of workers sorting fruit at an given packing house ranged from 6 to 12 on average. Sorters had worked in the industry for an average of 10 years (Table 3). The sorting tables consisted of a cross-flow rolling table situated at a height of 36 to 38 inches and a width of 19 to 22 inches. Fruit judged to be minority grade was placed on one of two smaller conveyor belts located above the sorting table at a distance of 21 to 24 inches. Culls and damaged fruit were tossed down a chute located to the side of each worker at the rim of the sorting table. Rotten fruit was tossed into a bucket located on the floor near the sorter. Workers were observed frequently bending and twisting their necks while inspecting the apples. Some shorter sorters stood on a wooden box to reduce their reach to the fruit. Chairs or stools were provided for some sorters; however, most sorters were observed standing throughout the shift. Floor mats were seen at some workstations, with varying degrees of cushioning quality to serve for anti-fatigue purposes. Workers at Company 3 placed bubble wrap padding on edges of the sorting table to reduce pressure points from sharp edges.
The sorting cycle consisted of only one task: picking up an apple and placing it on a
conveyor, chute, or bucket. The full cycle took a mean time of 3 seconds, with Companies
1 and 3 lasting 2 seconds, while Company 2 lasting 4 seconds (Table 9). Variability might
be explained by the quality of fruit processed that day. The production rate was highest at
Company 2.
Table 9 Mean Cycle Time Sorting Apples, by Company
Job |
Description of Tasks |
All Companies |
Company 1 |
Company 2 |
Company 3 |
N |
Mean |
SD |
N |
Mean |
SD |
N |
Mean |
SD |
N |
Mean |
SD |
Sorter |
Inspect Apples |
238 |
3 |
4 |
80 |
2 |
2 |
60 |
4 |
7 |
78 |
2 |
2 |
Figure 2 Sorter with Extended Reach to Place Apple on Conveyor
4.4.1.1 Job Task Observations
The primary risk factors related to sorting included neck position, static standing posture, and upper extremity motions of the hand/wrist, forearm, and elbow (Table 10). The results of the observations show that workers were sorting apples with their neck flexed >15 degrees during most of the shift (85% of shift time). Sorters were also standing stationary 67% of the shift time. Other predominant risk factors include: hand deviation, forearm twisting, elbow extension and wrist flexion/extension. Of hand/wrist postures, hand deviation occurred most frequently, and sorters spent more time deviating the right hand more (68%) than the left hand (52%) (Appendix E). Across the three companies, the majority of the risk factors on the right side were greater than the left side. Some sorters preferred to use gloves during sorting. The influence of gloves on dexterity and grip force was not assessed. Some workers from all companies spent some time leaning their torso onto the edge of the table while sorting.
Table 10 Percent of Shift Risk Factors were Observed – Sorters
Body Part |
Risk Factor |
% of Shift |
Neck |
Neck extend/flex>15deg. |
85% |
Hand/Wrist |
Hand Radial/ulnar deviation |
60% |
|
PPE-gloves/wrist band |
32% |
|
Wrist flex/extend |
31% |
|
Hand Pinch grip |
18% |
Elbow |
Forearm twist/rotate |
39% |
|
Full elbow extension |
38% |
Back |
Stand stationary |
67% |
|
Sitting |
23% |
|
Torso contact stress |
17% |
4.4.1.2 Self-Reported Symptoms
Fifty-seven percent of sorters interviewed reported a work-related problem for at least one body site. The following criteria for work-relatedness was used: 1) occurred at least once a week or lasted one week or more, 2) did not start as the result of an acute trauma, 3)
occurred in the last year and 4) was first noticed on the current job. Nearly half of back and shoulder problems were classified as work-related (Table 11). Most notably, not all work related problems had workers compensation claims filed. Fifty-five percent of the reported back symptoms were severe enough to seek medical treatment in the last year. Nine of 20 sorters reported neck symptoms; however, 5 of these cases were due to a sudden injury. Sixty-six percent of the sorters with hand/wrist symptoms reported similar symptoms to that often used to describe carpal tunnel syndrome (pain that caused they to awake from sleep or pain up arm). Hand/wrist, neck, and back problems were most severe in terms of workdays missed with 25, 14, and 11 days missed, respectively. The sorters who experienced days of missed work reported that their hand/wrist problems began when they were working as packers. More hand/wrist problems (3 additional) would be classified as work-related if the criteria were expanded to include problems first noticed during a packing job (sorting is often considered a light duty job for injured packers). One-third of the sorters reported that their hand/wrist and back symptoms affected the pace they could work.
Table 11 Self-reported Symptoms – Sorters (n=20)
|
Back # (%) |
Hand/Wrist # (%) |
Neck # (%) |
Shoulder # (%) |
Elbow # (%) |
Problem reported (no.) |
11 |
9 |
9 |
11 |
3 |
Problem work related |
5 (45%) |
2 (22%) |
1 (11%) |
5 (45%) |
0 |
Workers comp claim filed |
3 (27%) |
2 (22%) |
0 |
2 (20%) |
0 |
From sudden injury |
1 (9%) |
3 (33%) |
5 (55%) |
1 (10%) |
0 |
Started with current job |
6 (5%) |
6 (67%) |
4 (44%) |
8 (80%) |
1 (33%) |
Pain down leg |
1 (9%) |
NA |
NA |
NA |
NA |
Pain down arm |
NA |
NA |
4 (44%) |
NA |
NA |
Pain wake from sleep |
NA |
5 (56%) |
NA |
NA |
NA |
Pain up arm |
NA |
1 (11%) |
NA |
NA |
NA |
Trouble opening jars |
NA |
9 (100%) |
NA |
NA |
NA |
Medical treatment in last year |
6 (55%) |
4 (44%) |
2 (22%) |
3 (30%) |
0 |
Missed work |
3 (27%) |
2 (22%) |
2 (22%) |
1 (10%) |
1 (33%) |
Total person-days work
missed
|
11 |
25 |
14 |
2 |
2 |
Affected work pace |
4 (36%) |
3 (33%) |
NA |
NA |
NA |
Had surgery |
1 (9%) |
2 (22%) |
0 |
1 (10%) |
0 |
4.4.1.3 Risk Perception
Sorters noted they were most concerned about hand and wrist and other repetitive motion. Also, sorters were more likely to complain of problems with their arms as compared to other workers. Sorters from Companies 1 and 3 suggested that slowing the work pace would be useful in preventing injuries.
4.4.1.4 Across Shift Body Discomfort
Sorters indicated that the areas of greatest across shift discomfort were the upper back, shoulders, and neck (Figure 3) with the upper back and shoulder producing highest across shift discomfort scores, 1.4 and 1.5, respectively (Table 8). The across shift discomfort score for the neck was 1.1.
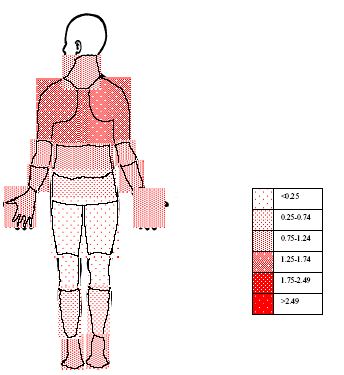
Figure 3 Sorter Across Shift Body Discomfort Map (n = 11)
4.4.1.5 Discussion of Sorting Job
Little ergonomic research and intervention have been done from a human factors perspective in agricultural workplaces. In fruit and vegetable warehouses, the task of sorting has received the most attention; however, this research has focused on the physical design parameters of equipment, productivity and work schedule of the sorter, and on the quality of the fruit inspected (Malcolm and DeGarmo, 1953; Nicholson, 1985; Prussia and Meyers, 1989; Meyers 1990; Bollen, 1986; Bollen, 1993; Colquhoun, 1959; Purswell and Hoag, 1974; Faulkner and Murphy, 1973; Miller, 1991). For example, one study found that the rate at which fruit can be sorted is affected by the type of defect (Bollen, 1993). Values range from around 5 fruit per second for simulated products with few defects to one to two fruit per second for real fruit. Another study reported that sorting efficiency decreases if a sorting table is wider than 0.75m (30 inches) (Bollen, 1986). And other ergonomic principles have been found to be important, such as visibility of the table and viewing location of the product (e.g. directly approaching the sorter vs. the side) (Nicholson, 1985; Meyers, 1990; Prussia and Meyers, 1989). Zegers (1989) provides a discussion regarding the mental workload of a sorter, but does not provide any data to support this opinion. Studman (1998) systematically measured physical discomfort among apple sorters and their performance while using a new apple handling system that passed apples directly in front of the sorter. Sorters preferred to work on a table designed so that maximum forward reaching distance was reduced and to sit rather than stand. Sorters also reported a high number of cases of neck and shoulder discomfort at the end of the shift. The Studman study was unable to detect changes in sorter performance due to changes in table design.
Our study is the first to characterize the ergonomic hazards in apple sorting. Sorters’ posture at the sorting table, the reach required to pick up and deposit apples, and the repetition of the task pose a hazard to these workers for neck, hand/wrist, shoulder and back injury. Most sorters lean slightly forward with bent neck and maintain a constant static posture. This position fatigues the neck and back and, since there is no change of posture, the muscles do not have time to recover between muscle contractions. Shoulder discomfort could be related to reaching to the far end of the conveyor and lifting the hand above the shoulder to deposit apples on high conveyors.
Our findings show that more than 50% of sorters reported at least one problem relating to the back, hand/wrist, neck, and/or shoulder and that at least 25% of sorters reported a problem that met our definition of work-relatedness. The symptom survey identified back and shoulder as the most frequently reported work-related problem. Other work-related problems were reported in the hand/wrist and neck sites. This was in basic agreement with the discomfort map where upper back, shoulder, and neck had the highest across shift scores. The discomfort map is an indicator of how workers feel after a given day of work, and it provides body-site specific detail. For example, workers self reported the back as a problem, and the discomfort map results supported this. It is clear that the upper back and shoulder region should be targeted for intervention. Studman (1998) also found that 39% of sorters reported neck, shoulder, and upper back problems and 30% reported lower back and hip discomfort before initial changes were made to the system. Although the studies were designed for different purposes, our findings regarding the location of symptoms (with the exception of hands/wrist) and discomfort level among sorters are in general agreement with Studman (1998).
Although hand/wrist problems appeared to be most severe based on the number of workdays lost in the last year, they did not score as high as the back, neck, or shoulders on the discomfort map. Sorting is considered a light duty job in all three of these packing houses and injured packers are often assigned to sorting during recovery. Additionally, there are reports in the literature that it is a common practice for long-term packers to change jobs to graders/sorters because of the strain of standing all day (Smith, 1963).
Job task observations documented that sorters frequently engaged in hand, arm, and neck postures that could cause injury with highly repetitive tasks. Given a cycle time of 2-4 seconds, a sorter could possibly perform 7,000-14,000 cycles in a shift. Although the force
of lifting apples during sorting is low (<1kg>
The results from the job task observations and symptom questionnaires are only in partial agreement. Sorters reported that back and shoulder were the major body parts of concern from both an acute (body map) and chronic (symptoms as work-related) level. A few risk factors that may contribute to shoulder and back pain were found in the observations (e.g. standing stationary, forearm twist, elbow extension), but problems were found to be greater for other body parts (neck or hands/wrist). Several explanations are possible: 1) analysts observed awkward postures in the neck but the actual symptoms may be felt by workers in the shoulders and upper back region, 2) all companies reported that their light-duty job is sorting, and therefore, some of the symptom reporting by sorters may have been due to nonsorting jobs, 3) the observational checklist has several limitations, which is why it is important to have several measurement methods. Muscle strength testing may be useful to assess job demands and maximum capacities of the various muscle groups that are used specifically during sorting.
4.4.1.6 Washington Ergonomics Rule – Sorter Job
The sorting job was reviewed from the perspective of the Washington State Ergonomics Rule. According to the Ergonomic Rule, a job must first be evaluated to determine whether or not it has tasks that meet the criteria for a “caution zone job” (CZJ). If the job meets the CZJ criteria, it should be further evaluated to identify specific hazardous tasks that can be feasibly remediated. The sorter job was evaluated according to these criteria.
“Caution Zone Job” Criteria
Task Description |
Risk Factor |
Caution Zone Job? |
Pick up apple and move to high conveyor (hand above shoulder) or bin to the side every 2 seconds- 7,000-14,0000/shift |
Highly repetitive; awkward neck postures; elbows elevated |
Yes |
Since the sorter job was found to meet the CZJ criteria, it was further evaluated for specific WMSD hazards. This analysis was done using the criteria from the Specific Performance Approach described in WAC 296-62-05130-Appendix B.
Sorter Job Hazard Analysis
Task Description |
Hazard Category and Criteria |
Is Task Hazardous? |
Pick up apple and move to high conveyor (hand above shoulder) or to bin at side every 2 seconds- 7,000-14,0000/shift |
Highly repetitive-same motion >6 hours/shift? |
Yes |
Awkward neck posture shoulders – raising elbow above shoulder >1/minute?; neck bent 45o? |
No |
According to the criteria outlined in the Ergonomic Rule, hand repetition was above the hazard level for the sorting job and the employer should take action to reduce the hazard.
4.4.1.7 Sorter Recommendations
Reducing hand repetition below the hazard level may be possible through the implementation of regular job rotation. Rotating sorters during the day to other jobs involving less hand repetition may help to mitigate this risk factor. The static posture of the back and neck exhibited by sorters could be relieved if these workers periodically changed from standing to sitting, as was observed in some packing houses. Another way to provide periodic relief from high repetition and static postures would be to provide a micro-break. Colombini (1998) recommends micro-breaks of 10 minutes for every 60 minutes of repetitive work. These micro-breaks could include lunch, regular required break periods, work on non-sorting tasks, as well as periods when the conveyor is down for maintenance or product changes. During these times workers should be encouraged to change positions and stretch. Purswell and Hoag (1974) found that changing a conventional 8-hour shift to a work day with 5 minute breaks every 30 minutes improved sorting accuracy to 85% throughout the day as compared to 60% accuracy during a conventional work day without micro-breaks. Regular rotation in the sorting line position could also make subtle but important changes in worker body posture.
The addition of a foot rail would allow sorters to intermittently stand on one foot with the other foot elevated; this has been found to be useful in reducing back fatigue in other applications (Eastman Kodak Company, 1983). The elbow and shoulder risks could be limited by reducing the width of the conveyor, thus reducing elbow and shoulder extension. Companies in New Zealand have tried new methods of sorting such as using a cascade conveyor sorting technique (Studman, 1998) which reduces the extended reach observed in sorting. Finally, the industry might consider exploring a torso support, an application that has been used in other industries to support a forward bent posture.
Sorting involves standing in one position for long periods. This can lead to fatigue or discomfort in the lower extremities and back. Anti-fatigue floor mats or cushioned shoe
inserts can reduce this fatigue or discomfort. Following are some suggestions for floor mats and platforms:
- mats should compress but not too much – see Appendix G for evaluation of comfort for various mats
- mats should have beveled edges, a non-slip surface, and should not slip on the floor
- if mats must be removed for cleaning, large mats are difficult to handle
- if the workstation is on a raised platform, the surface should be resilient rather than rigid (wood or plastic, not steel). The platform should also have a high ratio of surface to holes (not standing on “knives”)
4.4.2 Segregators
The number of workers in each company segregating filled boxes on pallets ranged from
three to five workers. Companies 1 and 3 located their segregation activities in the same
area as their packing operations, and Company 2 segregated boxes in a separate and colder
(45o F) area away from the packing facility. A conveyor system delivered packed boxes to
the segregation area. Boxes weighed 40-50 pounds with the industry-standard weight being
42 pounds. One segregator pushed a row of boxes on a roller conveyor to other segregators.
The other segregators manually lifted boxes off of the conveyor and placed them on
designated pallets. The workers rotated between pushing the boxes on the conveyor and
stacking the boxes. The boxes were stacked seven layers high with the seventh layer at 80
inches from the floor. Completed pallets were secured with twine and the pallets were
transported by forklift to controlled atmosphere storage or shipping. The conveyor heights
were 29-30 inches. Two to three rows of pallets were arranged on each plant floor. The
amount of room between pallets (for maneuverability) varied at different packing houses.
Approximately 20 to 30 pallets are located in a row depending on production needs and area
available.
The segregation cycle consisted of two tasks: pushing or pulling the box on a roller conveyor towards the pallet, and picking up the box, carrying it to a pallet, and positioning it on the pallet. The full cycle took a mean of 8 seconds at Companies 1 and 3, and 9 seconds at Company 2 (Table 12). The boxes were delivered to the segregation area sporadically and there was sometimes a short break between cycles while workers waited for another box. The average frequency of segregator lifts per minute was 4, with the highest frequency observed being 7. At a rate of 4 lifts per minute, a segregator who was stacking boxes for half of the shift (pushing boxes on conveyor the other half of shift) could lift as many as 1,000 boxes in a shift.
Table 12 Mean Cycle Time Segregating, by Company
Job |
Description Task |
All Companies |
Company 1 |
Company 2 |
Company 3 |
Segregator |
Manually roll box |
162 |
4 |
3 |
66 |
4 |
2 |
37 |
5 |
4 |
59 |
4 |
3 |
|
Pick up box and carry |
192 |
4 |
3 |
70 |
4 |
2 |
62 |
4 |
3 |
60 |
4 |
2 |
|
Total Cycle Time |
8 |
8 |
9 |
8 |
NOTE: Mean cycle time is in seconds; SD - Standard deviation
Figure 4 Segregator Stacking Box on Top Layer of Pallet
4.4.2.1 Job Task Observations
The most problematic risk factors associated with the segregation job were observed when workers stacked full boxes on a pallet. A variety of body postures and activities could produce fatigue and injury, primarily to the back, shoulders, elbows, and wrist. Pushing or pulling the box down the roller conveyor could also stress the back, elbows and wrists. The major risk factors identified from job task observations included: lifting, pushing/pulling, torso twisting, and wrist deviation (Table 13). In most cases, the risks were greater for the right side of the body than the left side (e.g. 41% pinch grip-right vs. 25% pinch grip-left) (Appendix E). The segregation tasks are dynamic and the use of the observational checklist selected for use in this study was not as useful for evaluating this job. Due to the heavy lifting requirement of the segregator job, the NIOSH lifting model and the University of Michigan 3D Static Strength Model were also used to evaluate this job.
Table 13 Percent of Shift Risk Factors were Observed – Segregators
|
Risk Factors |
Contributing Tasks |
% of Shift |
Hands/Wrist |
Wrist flex/extend |
Stack box on pallet, roll box down conveyor |
38% |
|
Hand pinch grip |
Stack box on pallet |
25% |
Elbows |
Full elbow extension |
Stack box on pallet, roll box down conveyor |
28% |
|
Elbow away 45 deg |
Stack box on pallet, roll box down conveyor |
26% |
Back & Shoulders |
Walking |
Stack box on pallet, roll box down conveyor |
93% |
|
Lift/carry |
Stack box on pallet |
47% |
|
Torso twist>20deg. |
Stack box on pallet |
45% |
|
Push/pull |
Roll box down conveyor |
33% |
|
Asymmetric lift |
Stack box on pallet |
31% |
4.4.2.2 Lifting Analysis of Segregators
Predictions using two separate models for assessing lifting requirements were developed to better understand the risks associated with the segregator job: the 1991 NIOSH lifting model and the University of Michigan 3D Static Strength Model. The NIOSH lifting model was used to evaluate the contribution of frequency and distance of lifts to the stresses on the lower back. The University of Michigan 3D Static Strength Model was used to evaluate the forces and stresses on the upper body during lifts that occurred above shoulder height.
The NIOSH lifting equation (Waters, 1994) was designed to assess the risk of low back injury by calculating a Recommended Weight Limit in pounds (RWL) of an object to be lifted. The RWL is the weight that nearly all healthy workers could lift without an increased risk of developing lifting-related low back pain. The RWL includes factors such as distance the box is held out from the body, distance of the hands above the floor, vertical distance the box is lifted from start to end, twisting angle of the lifter’s body, frequency that lifts occur, and quality of the handle. The values for many of these factors changed depending on the pallet row and layer where the box was placed and on how much room there was between pallets to maneuver.
Two factors that had a large effect on the segregator RWL were the pallet layer (height of box at deposition) and how far into the pallet (horizontal distance from the body) that the box was deposited. Figure 5 illustrates that for all segregator lifts the current box weight of 40-50 pounds well exceeds the RWL. For example, at box layer 3, when the box is deposited at approximately waist height, the RWL is 26 pounds. At the highest layer (layer 7) the RWL drops to 16 pounds.
Figure 5 Effect of Box Layers on RWL
To load a pallet, the segregator must lean over and extend their reach to deposit boxes in the center of the pallet, while less leaning (horizontal distance from body) is required to deposit boxes on the outside of the pallet. Figure 6 shows that as the horizontal distance (leaning over the pallet) increases, the RWL decreases. When the box is dropped immediately in front of the worker’s feet the RWL is 26 pounds, whereas it drops to 14 pounds when the box is deposited in the center of the pallet.
Figure 6 Effect of Horizontal Distance on RWL
To assess the potential for injury as a result of segregator lifting requirements, a Lifting Index (LI) was also calculated. The LI provides a relative estimate of the level of back stress associated with a lifting task. The LI is calculated by dividing the box weight by the RWL. With a LI of 1, most workers will be protected from injury. As the LI increases, the potential for injury increases (Waters, 1993). For example at a LI of 1 24% of females and 10% of males have an increased risk of low back pain, while at a LI of 3 99% of females and 75% of males have an increased risk of low back pain. Using the industry standard box weight of 42 pounds, the LI for the segregators’ lifting tasks would range from 1.6 to 2.9. This suggests that there is considerable potential for low back pain resulting from the segregators' box lifting tasks.
3D Static Strength Test. This computerized model, developed by the University of Michigan, was used to evaluate the compressive force on the lower back during lifting above the shoulder (box layers 6 and 7). A static strength analysis was chosen for this job, as the task requires frequent lifting in awkward back and upper body postures. Analyses were conducted for a large or 95th percentile male and an average or 50th percentile male lifting a 45 to 50 pound box. Lifting boxes of this size and weight exceeds the Action Limit (AL) for back compressive force when stacking the first two layers of boxes on the pallet, and exceeds the strength capacity of the shoulders in about 33% of people when stacking the top two layers of boxes. This suggests that segregators are at increased risk for either back or shoulder injury while performing this job in its current configuration.
4.4.2.3 Self-Reported Symptoms
Only 1 of the 13 segregators interviewed reported a work-related problem. Segregators reported primarily back and shoulders symptoms (Table 14). All of the symptoms related to back, shoulder and elbow started with the current job with the exception of one back injury. Five of the 13 segregators interviewed reported shoulder problems; however, only one case was considered tied to a chronic work-related condition (three cases were reportedly from a sudden injury). Forty percent of the shoulder problems required medical treatment and one case was identified as severe, resulting in 30 days of missed work.
Table 14 Self-reported Symptoms – Segregators (n=13)
|
Back # (%) |
Hand/Wrist # (%) |
Neck # (%) |
Shoulder # (%) |
Elbow # (%) |
Problem reported (#) |
3 |
1 |
0 |
5 |
1 |
Problem work related |
0 |
0 |
0 |
1 (20%) |
0 |
From sudden injury |
1 (33%) |
1 (100%) |
0 |
3 (60%) |
1 (100%) |
Started with current job |
2 (66%) |
0 |
0 |
5 (100%) |
1 (100%) |
Pain down leg |
1 (33%) |
NA |
NA |
NA |
NA |
Medical treatment in last year |
0 |
0 |
0 |
2 (40%) |
0 |
Missed work |
1 (33%) |
1 (100%) |
0 |
1 (20%) |
0 |
Total person-days work missed |
2 |
1 |
0 |
30 |
0 |
Workers comp claim filed |
0 |
1(100%) |
0 |
1 (20%) |
0 |
NA – not asked
4.4.2.4 Risk Perception
Segregators mentioned fewer hazards associated with their work than did other workers. Segregators did report concerns about the air quality, including chlorine, carbon monoxide, and dust; lifting hazards; and concerns about slippery floors, forklift speed, and the location of the pallets. One half of the segregators stated that there was little a person could do to prevent work injuries. Segregators did comment that a person should be careful and mentioned use of personal protective equipment, such as back belts, to reduce the risk of injury.
4.4.2.5 Segregator Across Shift Body Discomfort
Segregators showed very little change in across shift discomfort level (Figure 7). However, at the start of the shift 18% of segregators reported high discomfort (a score of 4 or 5) in the knees.
Figure 7 Segregator Cross Shift Body Discomfort Map (n=8)
4.4.2.6 Discussion of Segregator Job
A large body of evidence exists showing the hazards and associated adverse health effects with manual materials handling (NIOSH, 1997). The job task observations and lifting assessment tools clearly indicate that there is potential for musculoskeletal injury to segregators related to their lifting tasks. Job task observations showed that segregators were exposed to the following risk factors (right side dominant): lifting/carrying, flexing wrist, torso twisting, pushing/pulling, elbow extending, and elbow away. Although the number of segregators reporting symptoms in at least one body part was almost 40%, only one case was work-related using the study criteria. It was surprising to find that segregators showed very little change in across shift discomfort level; however, the few segregators who did report symptoms started their shift with a high level of discomfort (4 and 5). Some possible reasons for the lower symptom report rate of or among segregators include: 1) the segregators were the only men in the study, and they may not have felt comfortable disclosing their health problems; 2) the segregators may believe that the musculoskeletal discomfort associated with their work is expected and part of the job; and 3) the segregators are the youngest and most recently hired group of workers in the warehouse, and their lack of symptoms may be due to a healthy worker selection.
4.4.2.7 Washington Ergonomics Rule – Segregator Job
The amount and weight of lifting while segregating exceeds the hazard zone level for lifting according to Appendix B of the Washington Ergonomics Rule. This job was further evaluated for specific WMSD hazards. This analysis was done using the criteria from the Specific Performance Approach described in WAC 296-62-05130-Appendix B.
“Caution Zone Job” Criteria
Task Description |
Risk Factor |
Caution Zone Job? |
Lift 40-50 lb. boxes to pallet 500-800 times per shift |
Frequent & awkward lifting |
Yes |
Some boxes are lifted above shoulder or head height |
Awkward posture - shoulders |
Yes |
Segregator Job Hazard Analysis
Task Description |
Hazard Category and Appendix B
Criteria
|
Is Task Hazardous? |
Lift 40-50 lb. boxes to pallet 500-
800 times per shift |
Frequent heavy & awkward lifting
– box weight limit is 11-15 lbs.1
(depending on pallet layer where
box is placed).
Boxes weigh 40-50 lb. |
Yes |
Some boxes are lifted above shoulder or head height |
Awkward posture, shoulders – Hands above head >1/minute for 4 hours/day |
No |
Weight limit calculated using these assumptions: Unadjusted weight limit of 30 or 40 lbs. depending on pallet layer, 4-5 lifts/minute for 2 or more hours/shift, segregator twists at least 45o on some lifts.
Segregating is considered hazardous using the heavy lifting criteria in Appendix B of the ergonomics rule. An allowable box weight limit was calculated using the formula outlined in Appendix B (unadjusted weight limit X limit reduction modifier X twisting adjustment = recommended box weight limit) and assuming a 45° twist and above the shoulder lift. The calculated weight limit was compared to the weight of boxes currently lifted by segregators.
Calculated weight limits ranged from 11-15 pounds, considerably lighter than the usual box weight lifted by segregators.
The 40-50 pound boxes lifted by the segregators in this study were approximately three times heavier than the allowable box weight limit, using the Appendix B weight limit calculations. If twisting were eliminated or reduced to less than 45 degrees, the box weight limits could increase to 15-18 lbs. If, in addition, the stacking process was modified so that box layers 6 and 7 were not added by lifting above the shoulders, the box weight limit would be 18 pounds. If the frequency of lifting were also reduced to 2-3 lifts per minute, the box weight limit would increase to 20 pounds.
Lifting above the shoulder in this job did not meet the Appendix B criteria for awkward shoulder postures. Segregators lift boxes to the top (seventh) layer on a pallet for approximately 14% (1/7) of all lifts. There were an average of 4 lifts/minute observed, therefore approximately 0.5 lifts/minute (4 lifts per minute x 14%) involved boxes above the head. A over the head lift frequency of over 1 lift/minute is considered hazardous under Appendix B of the Ergonomics Rule.
According to the criteria outlined in the Ergonomics Rule, the segregating job was considered hazardous and the employer must take action to reduce the hazard.
4.4.2.8 Segregator Recommendations
The weight lifted, the frequency of lifting, the height boxes are stacked, and the distance away from the body that boxes are deposited present a serious risk of back and shoulder injury to segregators. The greatest risk occurs when boxes are stacked on the fifth to seventh layer on the pallet. Automatic palletization would be the most efficient way to reduce these risks, but the capital expenditure may not be affordable for smaller packing houses. An alternative engineering solution would be to stack two shorter stacks (one four boxes high and the other three boxes high) and then place one of these stacks on top of the other using a slip sheet push-pull forklift attachment. We have included information on this mechanism and literature on an available forklift retrofit in Appendix F. This solution would require more floor space.
The frequency of lifting and the amount of twisting required to place boxes on pallets are also important factors in the risk of injury. Rotation of segregation tasks with other tasks could be used to limit the duration of lifting. The segregation area layout should be evaluated to determine if there are ways to reduce the amount of turning (where most segregators twist) required to move the box from the conveyor to the pallets. There should be adequate room so that a segregator can turn his body with his feet rather than twisting at the waist.
4.4.3 Packing
Four different types of packing were assessed in the three packing houses in this study. Companies 1 and 2 conducted manual packing of bags and, while companies 1 and 3 conducted semi-automatic bag and tray packing. Some of the assessment tools evaluated the specific jobs done by subjects the day of the evaluation (Observations, Cycle Time, Body Discomfort Map) while other tools evaluated more long-term effects (Symptoms Survey, Risk Perception) to workers who often change jobs from day to day. In this section the long term effects to packers will be presented first, followed by the findings for specific packing jobs.
4.4.3.1 Self-Reported Symptoms
Sixty percent of the packers interviewed reported a work-related musculoskeletal problem to at least one body site. The greatest number of problems occurred at the back, hand/wrist, neck, shoulder, and elbow (Table 15). Seventy to eighty percent of the problems reportedly started with the current job. Over half of the back, hand/wrist, neck, and shoulder problems reported met the criteria for being work related; however, less than 10% had workers compensation claims filed. Less than 25% of problems reported for any body site were acute (sudden) injuries. Back injuries were the most severe injuries based on self-reported medical treatment (29% of reported back problems received medical treatment) and missed work-days (132 person-days). Back injuries reportedly affected work pace for 29% of those reporting. Workers with wand/wrist problems also had a large number of missed workdays (74 person-days) and over half of reported hand/wrist problems involved radiated or nighttime pain. Packers sought medical treatment for 29% of neck injuries.
Packers reported more elbow problems than other workers. Further analysis of packer symptom reporting indicated that many workers who reported elbow problems also reported hand (61%), shoulder (50%), and/or neck (42%) problems.
Table 15 Self-reported Symptoms – Packers (n=67)
|
Back # (%) |
Hand/Wrist # (%) |
Neck # (%) |
Shoulder # (%) |
Elbow # (%) |
Problem reported (no.) |
34 |
28 |
21 |
22 |
26 |
Problem work related |
21 (62%) |
18 (64%) |
12 (57%) |
15 (68%) |
7 (27%) |
Workers comp claim filed |
1 (3%) |
1 (4%) |
2 (10%) |
0 |
0 |
From sudden injury |
6 (18%) |
5 (18%) |
5 (24%) |
4 (14%) |
5 (19%) |
Started with current job |
27 (79%) |
23 (82%) |
15 (71%) |
22 (79%) |
21 (81%) |
Pain down leg |
12 (35%) |
NA |
NA |
NA |
NA |
Pain down arm |
NA |
NA |
12 (57%) |
NA |
NA |
Pain wake from sleep |
NA |
15 (54%) |
NA |
NA |
NA |
Pain up arm |
NA |
18 (64%) |
NA |
NA |
NA |
Trouble opening jars |
NA |
25 (89%) |
NA |
NA |
NA |
Medical treatment in last year |
10 (29%) |
3 (11%) |
6 (29%) |
4 (14%) |
4 (15%) |
Missed work |
7 (21%) |
2 (7%) |
1 (5%) |
2 (7%) |
2 (8%) |
Total person-days work missed |
132 |
74 |
1 |
17 |
17 |
Affected work pace |
10 (29%) |
NA |
NA |
NA |
NA |
Had surgery |
0 |
1 (3%) |
0 |
0 |
0 |
NA – not asked
There were surprisingly few differences between older and younger workers in symptom report rate or by body site (Table 16). Hand/wrist problems did not vary among the three age groups. Younger packers were more likely to report neck problems, while older workers were more likely to report shoulder and elbow problems. Hip and knee complaints were reported considerably less frequently by workers over 50.
Table 16 Symptom Reporting by Age – Packers
Age Range |
Workers Surveyed # (%) |
% of Workers Reporting a Problem |
Back |
Hand/Wrist |
Shoulder |
Elbow |
Neck |
Hip |
Knee |
Foot/Ankle |
< or =35 |
27 (40%) |
52% |
41% |
26% |
26% |
41% |
22% |
30% |
19% |
>35 < 50 |
28 (42%) |
39 |
43 |
36 |
46 |
25 |
32 |
21 |
29 |
>50 |
12 (18%) |
75 |
42 |
42 |
50 |
25 |
8 |
8 |
17 |
All Ages |
67 (100%) |
51 |
42 |
33 |
39 |
31 |
24 |
22 |
22 |
4.4.3.2 Risk Perception
Sixty percent of all concerns reported by packers were related to body discomfort, especially lifting, bending, and pushing and pulling stuck boxes and trays. Packer-reported activities that caused body discomfort included bagging, reaching, and standing. Packers were more likely to report concerns related to legs and feet, back, hand and wrist, shoulder, and neck. In addition, packers mentioned problems with the equipment, such as gaps in the belts where fingers could get caught, or incorrect sizing of the packing horses used to carry full boxes to the conveyer belt.
Company 2 packers were generous in making suggestions about modifications the company could make to improve packing work, the location of packing boxes, trays, and tissues. Packers at Company 1 and Company 3 suggested slowing the pace of the line to prevent injuries. At Company 2, where packing work is piece rate, slowing the conveyor rate was not mentioned.
4.4.4 Specific Packing Activities
4.4.4.1 Manual Tray Packing
The manual packing workstations were similar at Companies 1 and 2. Both companies had circular tubs (13 at Company 1 and 28 at Company 2). The tubs at Company 1 were 50 inches in diameter with the rim 35 inches from the floor, while the diameter and height from floor were 60 inches and 36 inches respectively at Company 2. The packer’s reach to apples in the center of the tub was greatest with the wide diameter tubs. In addition, Company 2 had a series of workstations along a long conveyor where apples moved past the packer in a circular flow. This conveyor was 37 inches above the floor and 24 inches wide. Graded apples were delivered to the tub or conveyor by the computer-controlled sizing conveyor. Workers manually packed both bags and trays from these stations.
Packers were positioned between the tub or conveyor and a cart known as a packing horse that held a cardboard box positioned at a slight angle (Figure 8). Two types of packing horses were observed: a roller style and a sliding-tray style. Flat boxes were folded and placed on the packing horse. Unfolded boxes were retrieved from storage locations that required awkward bending and stooping positions. Once the box was filled, the packer rolled the packing horse to a receiving conveyor and pushed it on the conveyor. The sliding-tray horse required a packer to move the full box by lifting a handle on the packing horse, while pushing the box onto the receiving conveyor with the other hand. The roller style packing horse did not require lifting the box; consequently, pushing onto the receiving conveyor required less effort. The roller style packing horse also had greater height adjustability.
Figure 8 Manual Tray Packing at a Circular Tub
The manual tray packing process involved placing a hard paper tray with indentations into a box and placing apples in the indentations. Four to five trays are required to fill the box, depending on the size of apples being packed. The number of apples per box varied in this study from 64 to 150. The packer typically stood with back and neck slightly bent towards the tub or conveyor. The reach to grab one apple varied with a maximum reach of 21 inches. Apples were picked up in one hand and tossed to the other hand, which was located over the box, and was then positioned into the tray.
The manual tray packing cycle included folding a box, packing, closing, and marking the box, and placing it on the conveyor which took a mean time of 101 seconds with little difference between Companies 1 and 2 (99 vs. 102 seconds) (Table 17). Interestingly, company 2 pays its workers by piecework and company 1 pays by the hour.
Table 17 Mean Cycle Time Manual Tray Packing, by Company
Job |
Task |
All Companies (1-2) |
Company 1 |
Company 2 |
Company 3 |
N |
Mean |
SD |
N |
Mean |
SD |
N |
Mean |
SD |
N |
Mean |
SD |
Manu |
Fold box |
93 |
9 |
4 |
33 |
9 |
4 |
60 |
9 |
4 |
NA |
Pack trays with apples |
114 |
77 |
32 |
34 |
76 |
35 |
80 |
78 |
30 |
NA |
Write on box |
93 |
9 |
5 |
34 |
8 |
3 |
59 |
9 |
5 |
NA |
Push box on conveyor |
93 |
6 |
5 |
34 |
6 |
2 |
59 |
6 |
5 |
NA |
Total cycle time (sec) |
101 |
99 |
102 |
NA |
NOTE: Mean cycle time is in seconds; SD - Standard deviation
NA - not applicable – this company did not do manual packing
4.4.4.1.1 Manual Tray Packing Job Task Observations
Neck position, static standing posture, and upper extremity motions of the hand/wrist, elbow, and forearm were the body risk factors observed during manual tray packing. Packing trays had the greatest number of risk factors (Table 18). The pinch grip was most frequently observed when picking up apples, whether with the right or left hand. The other risk factors related to the hand, elbow, and forearm were noticeably different with regard to the side of the body that was affected; the right side was much more frequently involved in almost all cases with the exception of wrist flexion/extension. For example, the elbow raised away from the right side of the body was observed for 60% of the shift compared with 25% of the shift for the left side of the body (Appendix E). Workers also fully extended the right elbow more frequently than the left (49 % vs. 9%). Most workers used their right hand to pack apples and tended to lean slightly into the tub to extend their reach.
Table 18 Percent of Shift Risk Factors were Observed – Manual Tray
Body Part |
RISK FACTOR |
Contributing Tasks |
% of Shift |
Neck |
Neck extend/flex>15deg. |
Fold box, pack trays |
82% |
|
Neck twist>15deg. |
Pack trays |
53% |
Hands/Wrist |
Pinch grip |
Pack trays |
56% |
|
Radial/ulnar deviation |
Pack trays |
54% |
|
Wrist flex/extend |
Fold box, pack trays |
39% |
Elbows |
Elbow away 45 deg |
Pack trays |
42% |
|
Forearm twist/rotate |
Pack trays |
37% |
|
Full elbow extension |
Pack trays |
29% |
Back |
Stand stationary |
Pack trays |
72% |
|
Torso side bend>20deg. |
Pack trays |
34% |
4.4.4.1.2 Manual Tray Packing Across Shift Body Discomfort
Manual tray packers reported the lowest across shift discomfort scores of all packing jobs. Most problematic areas were feet (.86), hands (.75), and upper (.75) and lower back (.71) (Figure 9).
Figure 9 Manual Tray Packer Across Shift Discomfort Map (n=6)
4.4.4.1.3 Washington Ergonomics Rule – Manual Tray Packer Job
The manual packing job was reviewed from the perspective of the Washington State Ergonomics Rule and was found to meet the CZJ criteria. Manual packing was further evaluated for specific WMSD hazards. This analysis was done using the criteria from the Specific Performance Approach described in WAC 296-62-05130-Appendix B.
“Caution Zone Job” Criteria
Task Description |
Risk Factor & Criteria |
Caution Zone Job? |
Place apple on tray every 0.9 seconds for full shift |
Highly repetitive – same motion every few seconds for more than 2 hours per day? |
Yes |
Make box and cover box with elbows away from body |
Awkward postures – no criteria in Rule |
No |
Stooping to obtain unformed box |
Awkward postures – no criteria in Rule |
No |
Manual Packing Job Hazard Analysis
Task Description |
Hazard Category and Criteria |
Is Task Hazardous? |
Place apple on tray every 0.9 seconds for full shift |
Highly repetitive-same motion >6 hours/shift? |
Yes |
According to the criteria outlined in the Ergonomics Rule, the Manual Packing job was considered hazardous and the employer must take action to reduce the hazard.
4.4.4.2 Manual Bag Packing
Manual bag packing is often done at the same circular tub or conveyor workstations as manual tray packing with the addition of a bagging stand, which holds a scale (not height adjustable) and bagging supplies. The packer places an empty bag on the bagging scale and fills the bag with apples with one hand while holding the bag open with the other hand. Some packers pick up two apples at a time to fill the bag more quickly. When the bag reaches a predesignated weight (or predesignated number of apples), the packer picks up the bag with one hand and spins it and applies a twist or clip tie with the other hand. The bag is then placed in a box and the process is repeated until the box is full. At the time of this evaluation, bag packers were filling 3- or 5-pound bags, 10 to 12 apples were packed per bag, and 8 bags to a box.
The manual bag packing cycle included: folding a box, packing, closing, and marking the box, and pushing the box onto a receiving conveyor. The full cycle took a mean of 159 seconds for Company 1 (Table 19). At Company 2, analysts only timed the bagging portion of the cycle, assuming that folding the box, closing and marking the box, and pushing the box onto the conveyor would take the same amount of time as was measured for manual tray packing activity at Company 2. This procedural change was made in order to have time to complete as many manual bag packer observations as possible. At Company 2, the complete cycle time was nearly three times as fast, 59 seconds, including the calculated post-bagging task. The large difference in cycle times between companies could be due to differences in sizes of apples bagged on the days observed or differences in production rates. The production rate was lower in Company 1 than Company 2 (48 vs. 72 boxes/FTE); Company 1 workers reported the line was moving more slowly than normal on the day of observations.
Table 19 Mean Cycle Time Manual Bag Packing, by Company
Job |
Description of Tasks |
Companies 1-3 |
Company 1 |
Company 2 |
Company 3 |
N |
Mean |
SD |
N |
Mean |
SD |
N |
Mean |
SD |
N |
Mean |
SD |
Manual bag packer |
Fold box |
49 |
6 |
4 |
29 |
6 |
3 |
20 |
7 |
3 |
NA |
Pack bags with apples |
115 |
71 |
63 |
39 |
133 |
25 |
76 |
39 |
52 |
NA |
Write on box |
58 |
12 |
9 |
38 |
15 |
10 |
20 |
8 |
3 |
NA |
Push box onto conveyor |
* |
* |
* |
40 |
5 |
5 |
* |
* |
* |
NA |
Total Cycle Time: |
89 |
159 |
54 |
NA |
NOTE: Mean cycle time is in seconds; SD - Standard deviation
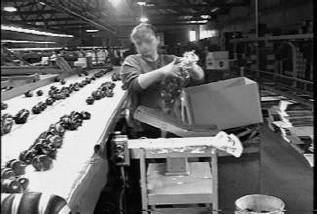
Figure 10 Manual Bag Packer Twist-Tying a Bag
4.4.4.2.1 Manual Bagging Job Task Observations
The upper extremity motions of the hand/wrist, elbow, and forearm, bag lifting, and static standing posture including neck bending were the observed risk factors with the greatest potential for producing musculoskeletal injury (Table 20). The analysis of the observations shows that baggers were using both hands about equally with right hand use slightly more than the left; this is because most packers reached into the tub with the right hand, and thrust the apple into the left hand for placement into the waiting bag (Appendix E). The risk factors observed during manual bagging were similar to manual tray packing; however, two additional factors were observed during manual bagging: lift/carry (right) and asymmetric lift.
Table 20 Percent of Shift Risk Factors were Observed – Manual Bagging
Body Part |
RISK FACTOR |
% of Shift |
Neck |
Neck extend/flex>15deg. |
59% |
|
Neck twist>15deg. |
40% |
Hands/Wrist |
Hand pinch grip |
59% |
|
Hand radial/ulnar deviation |
42% |
|
Wrist flex/extend |
25% |
Elbows |
Forearm twist/rotate |
30% |
|
Elbow away 45 deg |
29% |
|
Full elbow extension |
26% |
Back and Shoulders |
Stand stationary |
58% |
|
Lift/carry |
20% |
|
Asymmetric lift |
24% |
|
Torso side bend>20deg. |
22% |
4.4.4.2.2 Manual Bagging Across Shift Discomfort
Manual bag packers reported the greatest across shift discomfort of the elbow, shoulder, upper back, and neck (Figure 11). These data only represent manual baggers from Company 1 because at Company 2 packers either packed trays all day or did a combination of manual tray and bag packing.
Figure 11 Manual Bag Packer Across Shift Body Discomfort (n=9)
At the start of the shift, 20% of manual bag packers reported high discomfort (a score of 4 or 5 on a scale of 1-5) for the hand/wrist. This pre-shift discomfort may be an indicator of inadequate recovery from the previous shift and may suggest a chronic problem.
4.4.4.2.3 Washington Ergonomics Rule – Manual Bag Packer Job
The manual bagging job was reviewed from the perspective of the Washington State Ergonomics Rule and was found to meet the CZJ criteria. Manual bagging was further evaluated for specific WMSD hazards. This analysis was done using the criteria from the Specific Performance Approach described in WAC 296-62-05130-Appendix B.
“Caution Zone Job” Criteria
Task Description |
Risk Factor & Criteria |
Caution Zone Job? |
Put apple in bag – 13,000 apples/shift |
Highly repetitive – same motion every few seconds for more than 2 hours per day? |
Yes |
Make box and cover box with elbows away from body |
Awkward postures – no criteria in Rule. |
No |
Stooping to obtain unformed box |
Awkward postures – no criteria in Rule. |
No |
Grip apple bag of 3-10 lbs. (palmer or pinch grip) |
High hand force – pinch 2 lb. object or grip 10 lb. object >2 hours/day |
Yes |
Pick up 1,200 bags/shift |
Highly repetitive – same motion every few seconds for more than 2 hours per day? |
Yes |
Manual Bagging Job Hazard Analysis
Task Description |
Hazard Category and Criteria |
Is Task Hazardous? |
Put apple in bag – 13,000 apples/shift |
Highly repetitive – same motion >6 hours/shift |
Yes |
Grip apple bag of 3-10 lbs. (palmaror pinch grip) |
High hand force – pinch grip of 2 lb. object w/ high repetition; any grip of 10 lb. object w/ high repetition |
Yes |
Pick up 1,200 bags/shift |
Highly repetitive – same motion >6 hours/shift |
Yes |
According to the criteria outlined in the Ergonomics Rule, the manual packing job was considered hazardous and the employer must take action to reduce the hazard. Manual bag packing must be modified to reduce repetitive motion and high hand force below the hazard level or to the degree feasible.
4.4.4.3 Manual Packing Discussion
The incidence or prevalence of musculoskeletal disorders has been reported in the literature for many occupations (e.g. meat processors, packers, assembly-line packers, and frozen food factory workers) that require repetitive or intensive use of the hands (Armstrong, 1993). The incidence of muscle-tendon syndrome was 56% (Luopajarvi, 1979) among assembly-line packers in food production who performed repetitive arm work (repetitive motions up to 25,000 cycles per workday). Chiang (1990) found a 40% incidence of carpal tunnel syndrome (according to nerve conduction velocity tests) among workers who packed nonfrozen food using “high” repetitive wrist movements (no specific information on the number of repetitive motions was provided). Amano (1988) reported a 14% incidence of tension neck syndrome among female assembly-line workers who used repetitive arm movements to handle 3,400 shoes per day. Ohlsson (1995) found a statistically significant association between exposure to repetitive work and diagnoses in both the neck/shoulders and elbows/hand among women assembling fuses and other electrical equipment. Several studies have found that workers with exposure to repetitive work of upper extremities and who are paid on a piece-rate system may have increased risk for musculoskeletal disorders (Kuorinka and Koskinen, 1979; Brisson, 1989; and Ohlsson, 1995).
In agricultural warehouses, the application of ergonomic research has been applied to the process of manual packing but limited to citrus crops, such as oranges. Smith (1963) compared the packing rate and cost of packing between a frontal pack method and a side pack method. He found that a frontal packing method was cost-effective, and applied ergonomic principles of work station design and posture to explain his findings. The purpose of the frontal pack method is to eliminate the packers need to lean and twist over a bin when reaching for the fruit. No measurements of worker fatigue, strain, or discomfort were provided in this early study. The frontal pack method is common in citrus warehouses; however, the side pack method is common in the apple and pear packing lines in Washington State. Smith (1963) provides a good description of the advantages and disadvantage of frontal packing of citrus fruit and outlines parameters of the system that are key to reducing worker fatigue and strain. No other studies were found that discussed ergonomic hazards or incidence of musculoskeletal disorders among fruit packers.
Manual apple packers have a static posture of the neck and back as they lean into the tub or conveyor to pick apples. A static posture can produce fatigue because constantly tensed muscles never have an opportunity to recover. The degree of leaning depends on the height of the packer, the dimensions of the tub, and the reach required to grab an apple. A bent neck requires neck muscles to hold the weight of the head – with greater bending producing greater stress – also known as the bowling ball effect. Workstation design that reduces the reach and offers adjustability for workers of different heights would limit bending as well as awkward postures of the elbow and shoulder.
Both tray and bag packing are highly repetitive, with packers handling approximately 13,000 apples per shift (88 apples/box x 150 boxes/shift). Silverstein (1986) found that workers in high repetition/low force jobs had a three-times greater risk of cumulative trauma disorders of the hand and wrist than workers in low repetition/low force jobs; the risk increased to 30 times for high repetition/high force jobs. Manual tray packing would be classified as a high repetition/low force job since there is no lifting of heavy weight or other forceful hand or wrist exertion. In contrast, manual bag packers lift bags of 3-10 pounds more than 1,000 times per shift (8 bags/box x 150 boxes/shift). This could classify manual bag packing as a high repetition/high force job. This may also explain why manual bag packers reported more discomfort at the end of the shift than manual tray packers. On the day of our observations, packers were bagging 3- and 5-pound bags. The discomfort disparity between tray and bag packers might be greater on days when packers were packing heavier bags (up to 10 pounds).
A comparison of discomfort map, job task observations and symptoms data offers insight into which body parts and motions may be important for self reported symptoms (Table 21 and Figure 12). Because most packers do both kinds of manual packing, the symptom data are an amalgamation of tray and bag packing.
Tray packers reported more across shift discomfort of the hands. Tray packing requires more precision in placing apples in tray indentations, and more hand and wrist movement to adjust apples for optimal positioning within the tray. Tray packers must also continuously negotiate over the box lip to place apples in trays. This causes the most hand and wrist bending when placing apples in the bottom tray layers when the tray is deep inside the box. Wrist flexion/extension was observed more frequently in tray packers than bag packers (39% vs. 25%).
Tray packers also reported more across shift discomfort of the lower extremities (feet, calves, and knees). Tray packers stand stationary more frequently than bag packers (72% vs. 58%). The greater neck flexion in tray packers (82% vs. 59%) could also relate to standing for longer periods of time in a static posture. Static positions produce muscle fatigue increasing the potential for discomfort.
Bag packers reported more across shift discomfort of the back, shoulders, neck, and elbows. After a bag is filled, it is picked up to twist and close. The more frequent lift/carry (20% vs. 10%) and asymmetric lift (20% vs. 2%) in baggers as compared to tray fillers relate to picking up the bag. The severity of fatigue from this activity may depend on the weight of the bags lifted.
Manual Tray (N=6) |
|
Manual Bag (N=9) |
Figure 12 Discomfort Map Comparison of Manual Tray and Bag Packing
Table 21 Manual Packer Symptoms and Job Task Observations
Symptoms (% of All
Packers w/ Work-
Related Problem) |
Job Task Observations (% of shift) |
Manual Tray |
Manual Bag |
Back - 31% |
Lift/carry |
10% |
Lift/carry |
20% |
Asymmetric lift |
2% |
Asymmetric lift |
24% |
Torso side bend |
34% |
Torso side bend |
22% |
Stand stationary |
72% |
Stand stationary |
58% |
Hand – 27% |
Hand deviation |
55% |
Hand deviation |
42% |
Wrist flex/extend |
39% |
Wrist flex/extend |
25% |
Pinch grip |
56% |
Pinch grip |
60% |
Shoulder – 12% |
Hand above shoulder |
22% |
Hand above shoulder |
9% |
Neck – 18% |
Neck flex |
82% |
Neck flex |
59% |
The muscle groups of the back, shoulders, neck, and elbows are interrelated and strain on one group can affect other muscle groups. The discomfort reported by manual baggers for these body sites may all be related, at least in part, to lifting bags.
The pre-shift discomfort map may also be used to identify discomfort that may be carried over from previous shifts. Thirty-three percent of manual packers reported a high discomfort score (rating of 4 or 5) at the start of the workday in the hand/wrist and 17% reported pre-shift discomfort in the shoulders.
4.4.4.4 Manual Packer Recommendations
Both manual tray and bag packing use the same tub and conveyor system workstations; so, modifications to the tub and conveyor system would benefit both jobs. Extended reaches and bending into the tub could be reduced by reducing the width of the tub or installing a cone-shaped tub insert or center ring so that apples will roll toward tub edges and thereby be easier to reach. Other workstation changes could reposition the packer from the side to the front of the tub as recommended by Smith (1963).
Manual packing involves standing in one position for long periods. This can lead to fatigue or discomfort in the lower extremities and back. Anti-fatigue floor mats or cushioned shoe inserts can reduce this fatigue or discomfort (Appendix G). Static postures and fatigue could be reduced if packers had the option of leaning or standing supported for part of the time. Sit/stand stools (Appendix H) are available that have been designed for industrial applications where assembly line workers stand at a workstation.
Manual bagging results in considerable hand repetition. Reducing hand repetition below the hazard level may be possible through the implementation of regular job rotation. Job rotation or rest breaks as noted above for sorters would also be beneficial for packers. If the break involved stopping the conveyor, all jobs would benefit from the break schedule. As with sorting, packers should use mini-break times to change position and stretch.
The newer roller tray carts seen in some packing houses do not require a lift to move the box onto the receiving conveyor. The roller tray carts are also more adjustable in height than the older style slide tray carts.
A tray platform could be placed inside the box sleeve, lifting the bottom tray to a position at the top of the box. Each time another tray was added to the box, the platform would lower pneumatically, or with springs or cords, so that the next tray added would be positioned at the top of the box. This modification would keep the tray at the most accessible level and reduce the amount of back and hand/wrist bending observed while loading trays, particularly the bottom tray layers – and may improve production rates.
The duration of time a bagger holds a filled bag could be reduced if the bag could be twisted in place while supported on a lazy-Susan type mechanism. This would reduce the high force hand and asymmetric lifting of the bag. In addition, adhesive or tab closures could be applied mechanically. This equipment would be best placed on a height adjustable pole in front of the worker to reduce the amount of side twisting or bending.
The scale on the bag table was observed to be too high for some packers, creating awkward shoulder and arm positions and wrist/hand bending when placing fruit in the bag. A lower scale that matched the height of the tub lip could reduce arm and shoulder fatigue and possible injury.
In two packing houses unfolded boxes were stored underneath the receiving conveyor. This required packers to twist and bend to retrieve box material. Storing the boxes in a location
4.4.4.5 Semi-automatic Tray Packing
Companies 1 and 3 had semi-automatic packing lines, including both tray packing and bag packing. The tray packing equipment was very similar at the two companies, while the bag packing equipment was similar except that the packers at one company stood while packers at the other company sat on low stools. Tray packing and bag packing are very different processes so they will be discussed separately.
The computer-controlled sizer delivers apples to tray pack lines according to apple grade. The packer faced the 20-inch wide and 40-inch high conveyor, where trays were automatically fed onto the conveyor and apples rolled into the tray from the conveyor above. Packers repositioned apples in the tray indentations for optimal presentation with all apples positioned in the same direction while concurrently sorting out damaged or misgraded fruit, which is deposited on a conveyor above the tray packing line, requiring a 28-inch reach (Figure 13). Filled trays moved to the end of the packing conveyor to the boxing station. Sometimes the packer who arranged trays also worked the boxing station, while at other times a second packer was assigned to that station, depending on the production rate. At times the trays backed up on the conveyor and the continuous line extended to the boxing station. Box packers did not wait for filled trays to come to them; rather, they often pushed or pulled the trays to the end of the conveyor in order to fill the boxes more quickly. Packers pull trays with a pinch grip or push with one or both hands. Filled trays weigh approximately 8 to 12 pounds. A full box contains 4 to 5 trays, depending on the apple size.
At the boxing station, filled trays are picked up and deposited into a preformed cardboard box (Figure 13). Boxes were marked, and pushed onto a conveyor which carried the box to the palletizing area. Company 3 had a load leveler at the boxing station that reduced the awkward postures and reach required to place the first layers of trays into the box. When a box was full, the boxer rotated the box one-quarter turn and pushed it onto a receiving conveyor. A box packer may provide boxing support to two or three packing lines.
Rubber mats of varying degrees of resiliency were observed at some packing stations to reduce back and leg fatigue that often occurs from standing on concrete floors.
Figure 13 Box Filling and Apple Arranging – Semi-automatic Tray Packing
The semi-automatic tray packing cycle consisted of these tasks: arranging apples on the tray, placing the preformed box at the boxing station, and filling the box. The cycle time varied between the two companies – Company 1 had a cycle time of 159 seconds, while Company 3 had a cycle time of 55 seconds. At Company 1, mechanical problems occurred with the semi-automatic tray pack line during the observed work shift. Packers reported that the line pace was slower than usual and observers had a difficult time assessing a complete job cycle because of the slow pace.
Since semi-automatic tray and box packing is sometimes conducted by two different workers, the observation of a cycle sometimes involved both a tray packer and a box packer; consequently, one observation was sometimes of two individuals (Table 22).
Table 22 Mean Cycle Time Semi-automatic Tray Packing, by Company
Job |
Description of Tasks |
Companies 1-3 |
Company 1 |
Company 2 |
Company 3 |
N |
Mean |
SD |
N |
Mean |
SD |
N |
Mean |
SD |
N |
Mean |
SD |
Semi |
Place box |
114 |
6 |
3 |
36 |
6 |
3 |
NA |
78 |
6 |
3 |
Automatic |
Arrange apples in trays |
109 |
41 |
49 |
29 |
93 |
65 |
NA |
80 |
23 |
21 |
Tray Pack |
Load box |
116 |
26 |
19 |
39 |
25 |
29 |
NA |
77 |
26 |
12 |
|
Total Cycle Time: |
73 |
124 |
NA |
55 |
NOTE: Mean cycle time is in seconds; SD - Standard deviation
4.4.4.5.1 Semi-automatic Tray Packing Job Task Observations
Neck position, static standing posture, and upper extremity motion of the hand, wrist, forearm, and elbow were the risk factors observed with the greatest potential for producing musculoskeletal injury (Table 23). The pinch grip used to pull filled trays to the box was of particular concern because it is coupled with high force when pulling 8-12 pound trays with finger muscles. The elbow positions and hands above shoulders relate to the width of the conveyor and position of re-sort conveyors. The full elbow extension occurred when packers extended their arms out to pull the tray toward the boxing end of the conveyor, and when reaching to the farthest side of the conveyor to arrange the apples. A higher percentage of right side use was found with full elbow extension (54% vs. 27%) and pinch grip (55% vs. 38%) as compared to other risk factors (Appendix E). These two risk factors were observed when packers needed to exert some force during product handling, and may be explained by the fact that most packers were right handed and relied on the more dominant hand to do this exertion.
Table 23 Percent of Shift Risk Factors were Observed – Semi-auto Tray
Body Part |
RISK FACTOR |
Contributing Tasks |
% of Shift |
Neck |
Neck extend/flex>15deg. |
Arrange apples on tray, load box |
67% |
|
Neck twist>15deg. |
Arrange apples on tray, load box |
28% |
Hand/Wrist |
Hand |
Pinch grip Load box, arrange apples on tray, place box |
47% |
|
Hand Radial/ulnar deviation |
Arrange apples on tray, load box |
47% |
|
Wrist flex/extend |
Arrange apples on tray, load box |
36% |
Elbow |
Full elbow extension |
Arrange apples on tray, load box |
41% |
|
Elbow away 45 deg |
Arrange apples on tray, load box |
29% |
|
Forearm twist/rotate |
Arrange apples on tray |
27% |
Shoulder |
Hand above shoulder |
Arrange apples on tray, load box |
20% |
Back |
Stand stationary |
Arrange apples on tray, load box |
65% |
4.4.4.5.2 Semi Automatic Tray Packing Across Shift Body Discomfort
Semi-automatic tray packers reported the greatest increase in discomfort in the area of hands/wrist (1.9), upper back (1.7), shoulders (1.6), and feet (1.5) (Figure 14). Their discomfort scores were considerably higher than were the scores for the manual tray packers, although hands, upper back, and feet were high in both groups. It may be that the manual tray packers were engaged in more varied tasks (making boxes and depositing the box on the conveyor) that served as micro-breaks for various muscle groups.
Figure 14 Semi-automatic Tray Packer Across Shift Body Discomfort (n=10)
Further analysis of the pre/post - shift discomfort map data revealed there were differences in the level of discomfort reported by packers at the two companies observed (Table 24). Packers at Company 3 reported more than two times the across shift change did the packers at Company 1. The difference may be due to the slower production pace observed at Company 1 (48 vs. 58 standard boxes/FTE).
Table 24 Across Shift Body Discomfort Semi-automatic Tray Packers
Company
|
Type of Packing |
N |
Across Shift
Change |
Worker
Age |
Yrs at Packing Houses |
1 |
Semi-auto tray |
5 |
0.7 |
34 |
4 |
3 |
Semi-auto tray |
4 |
1.7 |
37 |
9 |
At the start of the shift, 21% of semi-automatic tray packers reported high discomfort (a score of 4 or 5 on a scale of 1-5) for the lower back. This pre-shift body discomfort is an indicator of inadequate recovery from the previous shift and may suggest a chronic problem.
4.4.4.5.3 Washington Ergonomics Rule – Semi-automatic Tray Packers Job
The semi-automatic tray packing job was reviewed from the perspective of the Washington State Ergonomics Rule and was found to meet the CZJ criteria. Semi Automatic Tray Packing was further evaluated for specific WMSD hazards. This analysis was done using the criteria from the Specific Performance Approach described in WAC 296-62-05130- Appendix B.
“Caution Zone Job” Criteria
Task Description |
Risk Factor & Criteria |
Caution Zone Job? |
Constant modest wrist flexion and deviation to arrange apples on tray for full shift |
Highly repetitive – same motion every few seconds for more than 2 hours per day? |
Yes |
Pinch grip to pull 8-10 lb. trays down conveyor 1-5 times/minute* for full shift |
High hand force – pinching 2 lb. object per hand more than 2 hours total per day |
Yes – if 5 times/min.
No – if <5 times/min. |
*Assuming 3 seconds/pull, 5 pulls/minute = 15 seconds/minute or 25% (2 hours) of 8 hour shift
Semi Automatic Tray Packing Job Hazard Analysis
Task Description |
Hazard Category and Criteria |
Is Task Hazardous? |
Constant modest wrist flexion and deviation to arrange apples on tray for full shift |
Highly repetitive-same motion more than 6 hours/shift? |
Yes |
Pinch grip to pull 8-10 lb. trays down conveyor 1-5 times/minute for full shift |
Pinch 2 lb. object with highly repetitive motion more than 3 hours total per day |
No |
According to the criteria outlined in the Ergonomics Rule, the semi-automatic tray packing job was considered hazardous and the employer must take action to reduce the hazard. Semi-automatic tray packing must be modified to reduce repetitive motion below the hazard level or to the degree feasible.
4.4.4.6 Semi-automatic Bag Packing
Semi-automatic bagging equipment was similar at the two companies, with the primary difference being that packers at Company 1 stood while packing and packers at Company 3 sat on low stools (Figure 15). Apples were dispensed from the computer-controlled sizing conveyor to a bagging machine chute. The packer held an empty bag out at about a 60o angle with two hands while waiting for the chute to fill with apples. This required the packer to hold the weight of his/her arms in that position for approximately 2-3 seconds. When the chute was filled with a predetermined weight of apples, the packer depressed a foot pedal to deliver apples into the air-inflated bag. The packer then lifted the 3- to 10- pound bag with one hand, usually using a pinch grip, twisted it, and applied a plastic closure clip using a pinch grip with the other hand (Company 1); or used an extended reach to insert the bag into the twist tie or clip closure machine (Company 3). The bag was then placed onto a conveyor for transport to boxing and palletizing. At Company 1, there was one transporting conveyor to the rear of the packers and another in front running under the bagging machines. Packers at Company 1 alternated between placing bags in front or behind them. At Company 3, all packers placed bags on a conveyor behind their workstations. Depositing apples on the conveyor to the rear of the packer required an extended elbow and twisted forearm, shoulder, and torso.
Figure 15 Semi-automatic Bag Packing at Company 1 (L) and Company 3 (R)
The semi-automatic bag packing cycle included filling the bag, applying the closure, and placing the bag on the conveyor. The mean cycle time was 7 seconds for Company 1 and 9 seconds for Company 3 (Table 25). Working at this rate with only limited breaks, a packer could handle 2,000-3,000 bags in one 8-hour day.
Table 25 Mean Cycle Time Semi-automatic Bag Packing, by Company
Job |
Description of Tasks |
Companies 1-3 |
Company 1 |
Company 2 |
Company 3 |
N |
Mean |
SD |
N |
Mean |
SD |
N |
Mean |
SD |
N |
Mean |
SD |
Semi
Automatic
Bag Packer |
Dispense apples |
160 |
3 |
3 |
80 |
2 |
1 |
NA |
80 |
3 |
4 |
Twist, tie, place bag |
160 |
5 |
3 |
80 |
5 |
2 |
NA |
80 |
6 |
4 |
Total Cycle Time: |
8 |
7 |
NA |
9 |
4.4.4.6.1 Semi-automatic Bagging Job Task Observations
While positioning and filling bags, awkward hand postures were the most frequent risk factor observed (Table 26). When closing the bag and placing it on the conveyor, holding the bag out to the side (asymmetric lift) and wrist, elbow, and torso twisting positions created the greatest potential for musculoskeletal injury. Torso twisting was twice as frequent in baggers in Company 3 as compared to Company 1 (45% vs. 21%). In general, the mechanism for operating the bagging machines were the same in each company; however, the position of the worker was very different. On average, baggers were sitting 34% of the shift (Table 26); however, this does not accurately reflect the work situations at both companies. Workers were standing at Company 1 and sitting at Company 3. Reaching behind the torso activity was substantially different at the two companies (9% for company 1 vs. 29% for company 3). Workers also reached behind the right side (27% vs. 12%) of the body more often than the left (Appendix E).
Table 26 Percent of Shift Risk Factors were Observed – Semi-automatic Bagging
Body Part |
Risk Factor |
Contributing Tasks |
% of Shift |
Neck |
Neck extend/flex>15deg. |
Position and fill bag |
43% |
Hands/Wrist |
Hand Pinch grip |
Position and fill bag, close and place bag |
73% |
|
Hand Radial/ulnar deviation |
Position and fill bag, close and place bag |
27% |
|
Wrist flex/extend |
Close and place bag, position and fill
bag |
21% |
Elbow |
Elbow away 45 deg |
Close and place bag, position and fill bag |
26% |
Back and Shoulders |
Asymmetric lift |
Close and place bag |
36% |
|
Sitting* |
Close and place bag, position and fill bag |
34% |
|
Torso twist>20deg. |
Position and fill bag |
33% |
|
Lift/carry |
Close and place bag |
22% |
|
Reach behind torso |
Close and place bag |
19% |
* Workers were standing at Company 1 and sitting at Company 3.
4.4.4.6.2 Semi-automatic Bagging Across Shift Body Discomfort
Semi-automatic bag packers reported greater across shift body discomfort than did workers in any other job assessed. The most discomfort was reported for the lower back (2.9), shoulders (2.1), upper back (2.1), elbows (2.1), and forearms (1.9) ( Figure 16).
Figure 16 Semi-automatic Bag Packers Across Shift Body Discomfort (n=10)
Further analysis of the discomfort map data revealed there were differences in the level of discomfort reported by packers at the two companies observed (Table 27). The across shift discomfort level reported by Company 3 packers was greater than that reported by packers at Company 1. Company 3 semi-automatic bag packers were older, had worked in packing houses longer, and sat at workstations on low stools. Older workers have slower recovery time when muscles become fatigued (DeZwart 1995) and more years performing these repetitive tasks can cause wear and tear on ligaments and joints which produce longer recovery time and an increasing risk of injury. Sitting on low stools limited the ability to move and re-position body weight – movements that allow redistribution of muscle stress. Sitting on low stools also forced packers to engage in greater torso twisting angles when placing bags on the rear conveyor. Alternatively, a standing station allowed the packer to step back and move the entire body to reach the conveyor rather than twisting the torso.
Table 27 Across Shift Body Discomfort – Semi-automatic Bag Packers
Company |
Type of Packing |
N |
Across Shift Change |
Worker Age |
Yrs at Packing Houses |
1 |
Semi-auto bag |
3 |
1.3 |
24 |
3 |
3 |
Semi-auto bag |
4 |
2.1 |
44 |
10 |
4.4.4.6.3 Washington Ergonomics Standard – Semi-automatic Bag Packers Job
The semi-automatic bagging job was reviewed from the perspective of the Washington State Ergonomics Rule and was found to meet the CZJ criteria. Semi-automatic bagging was further evaluated for specific WMSD hazards. This analysis was done using the criteria from the Specific Performance Approach described in WAC 296-62-05130-Appendix B.
“Caution Zone Job” Criteria
Task Description |
Risk Factor & Criteria |
Caution Zone Job? |
Pick up bag of 3-10 lbs.* (sometimes palmar, sometimes power grip) 2,00- 3,000 bags/shift |
Highly repetitive – same motion every few seconds for more than 2 hours total per day? |
Yes |
Hold unsupported arms out at 60o angle for 3 out of every 8 seconds for full shift |
No criteria in the Rule |
No |
* Assume 5 seconds of each 8-second cycle (more than 4 hours/day)
Semi Automatic Bagging Job Hazard Analysis
Task Description |
Hazard Category and Criteria |
Is Task Hazardous? |
Pick up bag of 3-10 lbs.* (sometimes palmar, sometimes power grip) 2,000 to 3,000 bags/shift |
High hand force-pinch of 2 lb. or any grip of 10 lb. with high repetition more than 3 hours total per day |
Yes |
*Assume 5 seconds of each 8-second cycle (more than 4 hours/day)
According to the criteria outlined in the Ergonomics Rule, the semi-automatic bagging job was considered hazardous and the employer must take action to reduce the hazard. Manual bag packing must be modified to reduce repetitive motion and high hand force below the hazard level or to the degree feasible.
4.4.4.7 Semi-automatic Packing Discussion
The production process of packing apples into trays or bags has been automated to some extent. Automation appears to decrease the physical load and repetition of packing apples into trays and bags. The semi-automatic processes in the participating companies reduced small repetitive motion because each apple is not handled separately. This moves the unit of repetition to the bag or tray. Most notably, the number of tasks that a worker performed and the cycle times for these tasks has decreased in semi-automatic packing. Although the same set of muscle groups are used (shoulders, arms, and hands) in semi-automated packing as in the manual process, the working postures changed to a more static nature, and the level of across shift discomfort was noticeably higher. Machinery, equipment, and workstation layout of semi-automatic tray packing was much different than was observed for manual packing. The impact of automation on workers’ health and working postures has received little attention in the literature. Several studies focused on the stress associated with machine paced work, and reported higher frequency of psychological and behavioral strain among workers engaged in automated or semi-automated processes. (Wilkes, 1981; Amick and Celentano, 1991; and Wands and Yassi, 1993).
Semi-automatic tray packers maintained fairly static neck and back positions that were slightly bent and leaning into the conveyor. Arranging apples on the tray required modest and continual hand and wrist bending and twisting. These static postures may result in fatigue, since they offer no opportunity for tensed muscles to relax and recover. When the packer was responsible for both tray arranging and box filling there was a break from the continual static postures. Packers should be encouraged to frequently change position and stretch as they work in order to reduce the effects of static posture.
Box fillers often pulled filled apple trays down the conveyors to the boxing station rather than wait for the trays to move to the boxing station. This allowed the workers to fill the boxes more quickly; however, when conducting this activity, workers used a pinch grip to pull the 8-10 pound trays. Since this is a high repetition task (600-700 trays/shift), it could be classified as a high repetition/high force task with significant increased risk of hand and wrist cumulative trauma disorder (Silverstein, 1986). The filled trays will be delivered to the box filling station automatically if the box filler waits for the tray to be pushed along the conveyor by the trays behind them. Alternatively, some box fillers used a hand on each side of the tray to push/pull the tray down the conveyor rather than using a pinch grip. This method for manually moving the trays is preferable to the pinch grip because it uses the larger and stronger muscles of the forearm rather than those in the fingers.
Semi-automatic bagging is a highly repetitive and high-force job. Working at a rate of seven bags per minute with only limited breaks, a packer handled 2,000-3,000 bags in a work shift. Semi-automatic baggers hold their hands out in front of their bodies while the apples drop into the bag, which requires holding the weight of their arms at about a 60o angle for approximately one third of the cycle time. They also held the weight of the full apple bag (3-10 pounds) while applying the closure tab, just as the manual bag packers do. The severity of fatigue from this activity would depend on the weight of the bags lifted.
Semi-automatic packers reported the greatest number of problems in the back and hand/wrist regions of the body. By combining information from the general symptoms questionnaire, the discomfort map, and observations, more details about the semi-automatic bag packer was elicited. Semi-automatic tray packers reported the most across shift discomfort of the hands (Figure 14). Job task observations indicated tray packers demonstrated three of the four hand risk factors. Tray packing required more precision in placing apples in tray indentations, and more hand and wrist movement to adjust apples for consistent position within the tray. Tray packers also reach with an elbow fully extended when adjusting apples in the tray row farthest from them, and this may be responsible for some of the reported discomfort in the elbows and upper shoulder regions.
Semi-automatic bagging risk factors (Table 28) and body discomfort were compared to that reported by semi-automatic tray packers (Figure 17). Bag packers had more frequent lifting risk factors than did tray packers (22% vs. 8% for lift and carry and 36% vs. 3% for asymmetric lift). Bag packers lifted filled bags in one hand while applying clip closures with the other hand. Bag packers were more likely to twist their torso (33% vs. 18%) and reach behind (27% vs. 3%) to place the bags on a moving conveyor than were tray packers. Twisting and reaching behind the torso occurred regardless of whether the bag packer was sitting or standing; however, sitting limited the ability to use the legs to step back and reposition the body thus reducing the degree of back twisting.
Table 28 Semi-automatic Packer Symptoms and Job Task Observation
Symptoms (% of All Packers w/ Work- Related Problem) |
Job Task Observations (% of shift) |
Semi-Automatic Tray |
Semi-Automatic Bag |
Back – 31% |
Lift/carry |
8% |
Lift/carry |
22% |
Asymmetric lift |
3% |
Asymmetric lift |
36% |
Torso twist |
18% |
Torso twist |
33% |
Sitting |
0% |
Sitting |
34% |
Standing |
65% |
Standing |
17%* |
Shoulder - 22% |
Reach behind torso |
3% |
Reach behind torso |
27 % |
Hand – 27% |
Hand deviation |
47% |
Hand deviation |
27 % |
Wrist flex/extend |
36% |
Wrist flex/extend |
21% |
Pinch grip |
47% |
Pinch grip |
73% |
Elbow - 10% |
Full elbow extension |
41% |
Full elbow extension |
18% |
* bag packers at Company 3 were sitting
The stress of these awkward postures combined with the static motion and weight of the bags may produce fatigue to the shoulders and back. Semi-automatic bag packers reported the highest across shift discomfort of the back, shoulders, neck, and elbows. Bag packers also reported high discomfort in the back and shoulders (Figure 17). Bag packers reported greater across shift discomfort by the end of the shift than did workers in any other job assessed. Packers at Company 3 reported the greatest across shift body discomfort in the back and shoulder region. At Company 3, the combination of sitting on low stools during an entire shift and twisting the back to handle the bags may create greater discomfort.
The muscle groups of the back, shoulders, neck, and elbows are interrelated and strain on one group can affect other groups. The discomfort reported by semi-automated baggers in these body sites may all be related, at least in part, to holding up the weight of their arms in a static posture and to lifting filled bags. Corlett and Manenica (1980) found that no posture can be maintained without rest. Others have found that alternating between standing and sitting is more beneficial than maintaining a single posture for prolonged periods of time.
Semi-automatic Tray (N=9) |
Semi-automatic Bag (N=7) |
Figure 17 Across Shift Body Discomfort: Semi-automatic Tray Packing and Bagging
4.4.4.8 Semi-automatic Packing Recommendations
Remaining in a static posture for extended periods creates fatigue for both semi-automated tray and bag packers. The recommendations for floor mats (Appendix G) and sit/stand stools (Appendix H) are applicable for all prolonged standing activities. Rest breaks would be beneficial for packers as well as sorters. If the break involved stopping the conveyor, all jobs would benefit from the brief break. Packers should use frequent mini-break times to change position and stretch.
An arms-extended position to hold the bag in place creates fatigue in the shoulders and back. Some of the bagging machines were designed with a drop-down bag chute. These machines allowed the operator to stand close to the machine, thereby reducing the angle and distance arms were held away from the body. At machines where greater arm extension was needed, a reciprocating armrest could be added to the workstation (see Appendix I for a commercially available example). To reduce the time the bag is held by the operator, a lazy Susan type mechanism could be designed to support the bag of apples as it is twisted and the closure tag attached.
Workstations with the conveyor positioned in front of the operator should be explored because they may eliminate the back and elbow twisting observed when the conveyor was located behind the packer. Alternatively, a slide chute could be installed to the right of each workstation directed to the rear of the conveyor. This would allow the packer to deposit the filled bag onto the conveyor without turning. Chutes could be hinged to ease access to the work area.
Twisting backward from the sitting position is a hazard for the back. When standing, the packer can take a step at a backward angle, at least reducing the angle of back twisting. If baggers are sitting at the bag machine, we highly recommend that bag-receiving conveyors be positioned in front of the machine.
Applying a twist tie to each bag involves a pinch grip and twisting of the forearm, which may be repeated as many as 2,000-3,000 times each shift. Machines are available that can attach adhesive or tab closures to the bags. This equipment should be positioned in front of the operator to avoid twisting.
The bag machines use a one-size-fits-all design. Ideally workstations should be adjustable to accommodate a variety of worker statures or allow workers to customize the work area. Other, low-cost solutions may include provision of adjustable 2- to 6-inch platforms for shorter workers.
Rotating the trays 90 degrees to place the long edge toward the packer could reduce the reach distance for automatic tray packing workers. A bar could be installed along the back edge of the conveyor to push the tray toward the packer. The box to be filled could also be rotated 90 degrees and the box filler would change position to a location facing the length of the conveyer. This would eliminate long reaches and twisting for the box filler.
High hand forces are required when packers pull trays down the conveyor. We propose two ways to reduce this risk factor: training for packers and modification of the equipment. Awareness training can be employed to explain the risk of pinch gripping and describe alternate methods for moving trays down the conveyor. Some packers used both hands to slide trays rather than pinch grip. Two-handed sliding is much less hazardous because larger muscles of the forearm are employed rather than the small muscles of the fingers. Another alternative is to wait for the trays to reach the conveyor end automatically. Trays left on the roller tray will be pushed to the end by the trays behind them. The disadvantage of this method is that trays cannot be loaded into boxes as quickly if the line is not delivering trays one after another. To engineer out the pinch grip motion, the roller tray portion of the conveyor could be replaced with a faster take-away. A light-switch cut-off could be installed at the end to stop the conveyor when the trays reach the box.
Back to Table of Contents
Disclaimer and Reproduction Information: Information in
NASD does not represent NIOSH policy. Information included in
NASD appears by permission of the author and/or copyright holder.
More